Lost-foam casting is an innovative and efficient method of metal casting that has gained popularity in various industrial applications due to its unique advantages. This process involves creating a foam pattern from polystyrene or another suitable material, which is then encased in a sand mold. After the mold is assembled, molten metal is poured into it, causing the foam pattern to vaporize and creating a cavity that takes the shape of the original foam.
One of the primary benefits of lost-foam casting is its ability to produce highly intricate designs with excellent dimensional accuracy. Traditional casting methods often require extensive machining to achieve the desired finish, whereas lost-foam casting minimizes this need. The foam pattern can be easily manipulated to create complex shapes and internal structures, allowing for greater design freedom in industries such as automotive, aerospace, and art.
Another significant advantage of lost-foam casting is the reduction of waste material
. In conventional casting processes, excess metal often leads to the creation of scrap, which can be costly and inefficient. Lost-foam casting eliminates this issue since the entire foam pattern is consumed during the casting process. This not only contributes to a more sustainable manufacturing process but also helps companies reduce their overall production costs.lost-foam casting
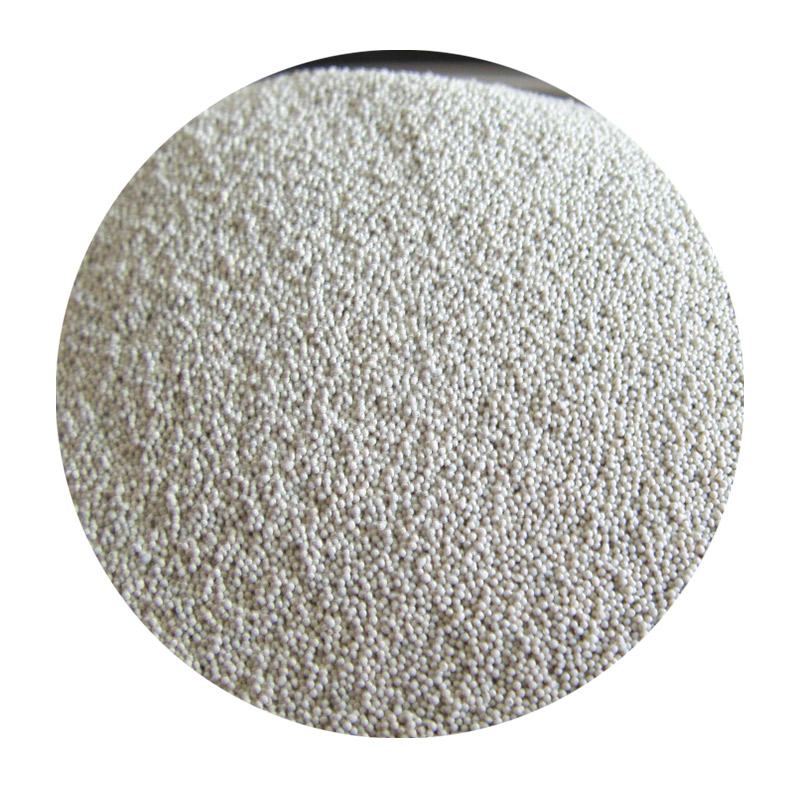
Moreover, the lost-foam technique allows for rapid prototyping. Designers can quickly produce foam patterns for testing and validation, speeding up the development process. This responsiveness is especially crucial in today's fast-paced manufacturing environment, where time-to-market can significantly impact a company's competitive edge. Manufacturers can adapt designs on-the-fly, responding to feedback from testing without the extensive lead times often associated with traditional tooling.
However, like all processes, lost-foam casting has its challenges. The choice of foam material must be appropriate to prevent combustion during the pouring of molten metal. Additionally, controlling the temperature and pouring speed is essential to avoid defects in the final cast. Despite these challenges, advances in technology and materials continue to improve the efficiency and reliability of lost-foam casting.
In conclusion, lost-foam casting represents a significant advancement in the field of metal casting. Its ability to produce complex shapes with high dimensional accuracy, reduce waste, and allow for rapid prototyping makes it an attractive option for many industries. As technology evolves, the use of lost-foam casting is likely to expand, paving the way for new innovations and applications in the manufacturing sector. This process not only highlights the importance of efficiency and sustainability in production but also showcases the creative possibilities within modern engineering.
Post time:نومبر . 24, 2024 07:15
Next:metal sand casting