Metal Sand Casting An Overview of the Process and Its Advantages
Metal sand casting, a time-honored manufacturing process, has played a pivotal role in the production of metal parts and components for various industries. This process dates back thousands of years and continues to thrive due to its unique advantages and adaptability. In this article, we will explore the intricacies of metal sand casting, its applications, benefits, and the innovations that are shaping its future.
The Sand Casting Process
At its core, metal sand casting involves creating a mold from sand, into which molten metal is poured to form a desired shape. The process begins with the preparation of a pattern, typically made of metal or plastic, which reflects the final product's dimensions. The pattern is then used to create a mold in a mixture of sand and a binder, which holds the particles together.
Once the mold is formed, it is split into two halves, allowing the pattern to be removed. This step is crucial, as it ensures that the mold can be assembled and disassembled without damage. After the pattern is removed, the two mold halves are secured, and molten metal—often made from alloys such as aluminum, iron, or bronze—is poured into the cavity. After the metal cools and solidifies, the mold is broken away to reveal the cast part.
Advantages of Metal Sand Casting
1. Versatility One of the most significant benefits of metal sand casting is its ability to produce complex shapes and intricate designs. This flexibility allows manufacturers to create a wide range of components, from small intricate parts to large heavy-duty items.
2. Cost-Effectiveness Sand casting is generally more economical than other metalworking processes, especially for low to medium production volumes. The raw materials—sand and metal—are relatively inexpensive, and the process requires less specialized equipment, reducing overall production costs.
3. Material Variety Sand casting can accommodate virtually any metal alloy, making it suitable for a diverse array of applications. This includes ferrous and non-ferrous metals, enabling its use in automotive, aerospace, and industrial machinery sectors.
metal sand casting
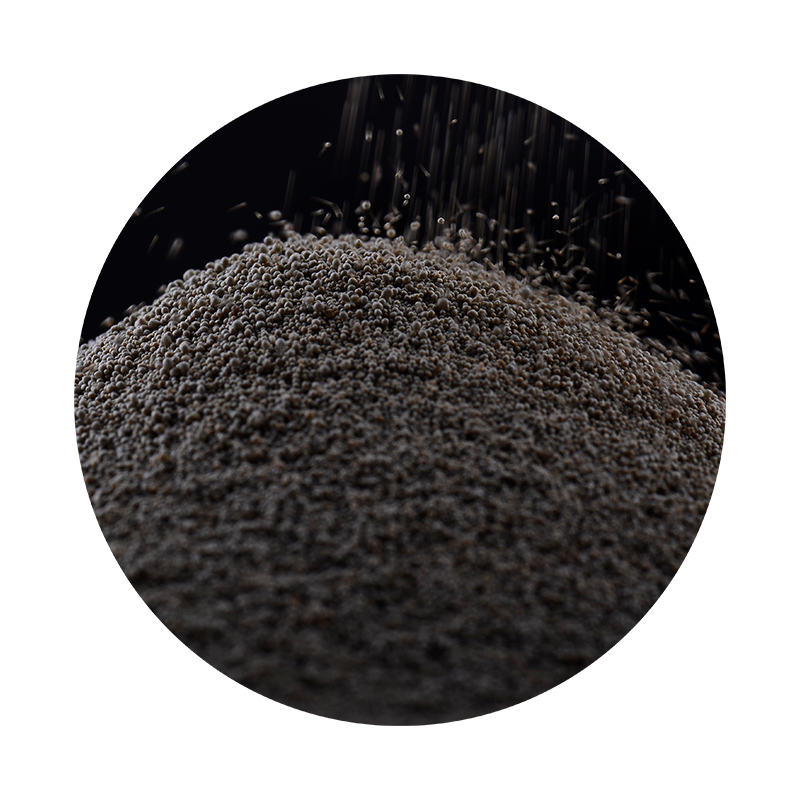
4. Large Production Capabilities With advancements in technology, sand casting can cater to large production runs, allowing businesses to meet industrial demands effectively. The process can be automated, increasing efficiency and ensuring consistent quality.
5. Recyclability Another advantage of sand casting is the environmentally friendly aspect of the materials used. The majority of the sand used in the process is reusable, contributing to sustainability in manufacturing. Moreover, scrap metal from the casting process can be melted down and reused, minimizing waste.
Innovations Influencing Sand Casting
In recent years, advancements in technology have begun to influence the sand casting industry significantly. Computer-aided design (CAD) software allows for precise modeling, which enhances the accuracy of patterns and molds. Additionally, the integration of 3D printing is revolutionizing sand casting by creating complex mold shapes that were previously difficult to achieve with traditional methods.
Moreover, the ongoing development of more effective binders and sand mixtures is improving the overall quality of casts, leading to fewer defects and enhanced surface finishes. Techniques such as vacuum-assisted sand casting minimize air entrapment in the molds, producing denser and stronger parts.
Applications of Metal Sand Casting
The applications for metal sand casting are virtually limitless. In the automotive industry, it is used for engine components, transmission housings, and more. In aerospace, it helps in manufacturing turbine parts and structural components. Other industries, such as construction and manufacturing, also rely on sand casting for creating valves, pumps, and various machinery parts.
Conclusion
Metal sand casting remains a cornerstone of the manufacturing landscape, blending tradition with innovation. Its versatility, cost-effectiveness, and ability to produce intricate designs make it an invaluable process across various industries. As technology continues to advance, the future of metal sand casting looks promising, poised to meet the evolving needs of modern manufacturing while maintaining its rich historical significance. As manufacturers embrace these innovations, the potential for enhanced quality and efficiency will likely propel metal sand casting to new heights in the years to come.
Post time:نومبر . 24, 2024 07:05
Next:sand castings supplier