Understanding the Sand Casting Process
Sand casting is a widely-used manufacturing process that allows for the creation of complex metal components. This technique, which dates back thousands of years, harnesses the unique properties of sand for molding materials, making it a reliable option for producing metal parts in various industries, including automotive, aerospace, and machinery.
At its core, the sand casting process involves creating a mold from sand that can retain its shape when metal is poured into it. The process is relatively simple and consists of several key stages pattern making, molding, pouring, cooling, and finishing.
Pattern Making
The first step in the sand casting process is to create a pattern, which is a replica of the final product to be cast. Patterns are typically made from materials such as wood, metal, or plastic, and they must be slightly larger than the finished part to account for shrinkage during cooling. The pattern is essential, as it establishes the internal and external features of the cast part.
Molding
Once the pattern is ready, the next stage involves forming the mold. This is achieved by compacting sand around the pattern. The sand used in this process is usually a mixture of silica sand, clay, and water, which gives it the necessary binding properties. The mold is created in two halves the cope (top half) and the drag (bottom half). After placing the pattern in the drag, the sand is packed around it to form a cavity. The cope is then placed over the drag, aligning the two halves to form a complete mold.
During this stage, additional features, such as risers and gates, may be included in the design. Risers are reservoirs that provide extra molten metal to compensate for shrinkage during cooling, while gates allow the molten metal to flow into the cavity.
what is sand casting process
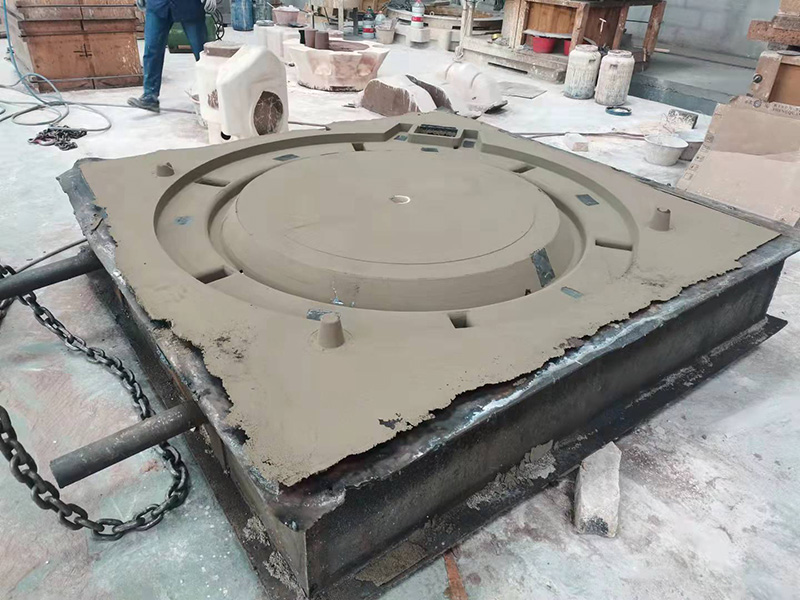
Pouring
With the mold prepared and assembled, the next step is pouring the molten metal into the mold cavity. The metal is typically heated in a furnace until it reaches a liquid state. Once the metal is sufficiently molten, it is carefully poured into the mold through the gate system. This stage requires precision and timing, as improper pouring can lead to defects in the final product, such as incomplete filling or trapped air pockets.
Cooling
After pouring, the molten metal must be allowed to cool and solidify within the mold. Cooling times can vary based on the type of metal used and the thickness of the cast part. Once the metal has fully cooled and solidified, the mold is broken apart to reveal the cast item.
Finishing
The final step in the sand casting process involves finishing the cast part. This may include trimming excess metal (known as flash), sanding surfaces to achieve a smooth finish, and machining critical features to precise dimensions. At this stage, any necessary inspection and quality control measures are also conducted to ensure that the part meets the required specifications.
Conclusion
In summary, sand casting is a versatile and effective process for creating metal components. Its simplicity, combined with the ability to produce complex shapes and sizes, makes it an attractive option for manufacturers. By understanding the intricacies of the sand casting process—from pattern making to finishing—businesses can leverage this traditional technique to produce high-quality parts tailored to their specific needs. As technology advances, sand casting continues to evolve, incorporating modern methods while maintaining its foundational principles, ensuring its relevance in contemporary manufacturing.
Post time:Nov . 10, 2024 10:28
Next:Foundry Casting Sand for Optimal Metal Mold Production and Quality Assurance