The Significance of Foundry Casting Sand in Metalworking
Foundry casting sand plays a pivotal role in the metalworking industry, serving as a critical material in the casting process. It is used to create molds that shape molten metal into desired forms, making it essential for producing everything from intricate machinery components to large structural parts. This article explores the properties, types, and uses of foundry casting sand, highlighting its importance in manufacturing processes.
Properties of Foundry Casting Sand
Foundry casting sand is characterized by its unique properties that make it suitable for mold making. The most common type of sand used is silica sand due to its high melting point, providing thermal stability when exposed to the heat of molten metal. Additionally, the sand must have excellent bonding properties, granulation, and permeability. Bonding agents are often added to improve the strength of the mold, allowing it to withstand the pressure and temperature during casting.
Moreover, the size and shape of the sand particles significantly influence the mold’s quality. Fine sand can create detailed, smooth surfaces, while coarser grains are used for larger, simpler casting applications. The ability to retain moisture in the sand mix is also vital, as it affects the sand's compactness, thus influencing the final cast's accuracy and finish.
Types of Foundry Casting Sand
There are several types of foundry casting sand, each suited for different applications. The most prevalent is green sand, a mixture of silica sand, clay, and water. Green sand molds allow for good strength and collapsibility, making them ideal for a variety of casting processes. They are particularly popular in the production of iron and steel castings.
foundry casting sand
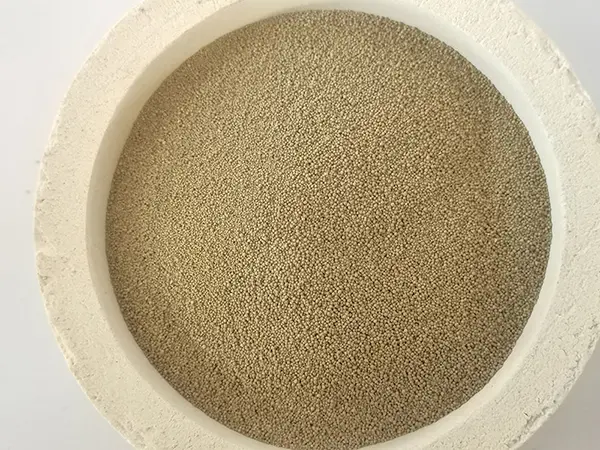
Another commonly used type is resin sand, which employs synthetic resin as a bonding agent. This type of sand offers superior strength and produces high-quality castings with excellent surface finish. Resin sand is often used for more precise applications, such as automotive parts and intricate industrial components.
Shell sand is another variant, formed into a thin shell by applying a resin-coated sand to a heated pattern. This process results in excellent dimensional accuracy and surface detail, making it suitable for less complex molds that require higher production speeds.
The Role of Foundry Casting Sand in Manufacturing
Foundry casting sand is indispensable in mass production processes. It facilitates the creation of molds that can be reused multiple times, contributing to efficient manufacturing practices and cost reductions. The choice of sand and its properties directly affect the quality of the final product. Poor-quality sand can lead to casting defects such as pitting, shrinkage, or dimensional inaccuracies.
Environmentally, advancements in foundry sand recycling practices are making a significant impact. Used foundry sand can be cleaned and reused in various applications, including construction and road building, thereby reducing waste and promoting sustainability.
Conclusion
In summary, foundry casting sand is crucial to the metalworking industry, combining its physical properties, various types, and its significant role in manufacturing processes to produce high-quality castings. With ongoing innovations in sand formulation and recycling methods, the future of foundry casting sand looks promising. Its adaptability continues to support a wide range of industries, ensuring that foundry casting remains a key component of modern manufacturing. As demands for precision and sustainability grow, so too will the importance and development of casting sand technologies.
Post time:Nov . 10, 2024 10:18
Next:Exploring the Current Market Trends for Gold and Sand Prices