Understanding Sand Casting and Its Importance in Manufacturing
Sand casting, a versatile and widely used metal casting process, has been a cornerstone of industrial manufacturing for centuries. It involves the creation of a mold from a mixture of sand, clay, and water in which molten metal is poured to form components of various shapes and sizes. Sand casting is known for its ability to produce complex geometries and large parts with excellent dimensional accuracy. This process is integral to various industries, including automotive, aerospace, and construction, providing essential components for both high-volume production and custom applications.
The Sand Casting Process
The sand casting process typically begins with the creation of a pattern, which is a replica of the desired final product. Patterns are usually made of durable materials such as wood, metal, or plastic. Once the pattern is ready, it is used to form a mold. The mold is created by packing sand around the pattern, forming both halves of the mold, known as the cope and the drag. The sand mixture is often treated with a bonding agent to improve strength and prevent collapse.
After the mold is prepared, the pattern is removed, leaving a cavity in the sand that corresponds to the shape of the desired part. The next step involves pouring molten metal into the mold cavity. The metal is heated in a furnace until it reaches a liquid state and is then carefully poured into the mold, where it fills the cavity and takes on the desired shape. Once the metal cools and solidifies, the mold is broken apart, and the casting is removed.
Advantages of Sand Casting
One of the primary advantages of sand casting is its versatility. It can accommodate a wide range of metals, including iron, aluminum, and copper alloys, making it suitable for diverse applications. Additionally, the process is cost-effective, especially for larger castings or lower production runs, as the materials and tools required are relatively inexpensive compared to other casting methods.
sand casting company
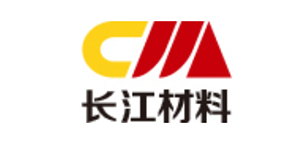
Moreover, sand casting offers excellent flexibility in design. Engineers and designers can create intricate designs and geometries that might be challenging to produce using other techniques. This capability is particularly significant in industries where performance and functionality are critical, such as in automotive and aerospace component manufacturing.
Applications Across Industries
Sand casting is employed in several industries for various applications. In the automotive sector, it is used to produce engine blocks, transmission housings, and other critical components that require durability and strength. In aerospace, sand casting allows for the manufacturing of lightweight components that can withstand extreme conditions. The construction industry frequently utilizes sand casting for creating large structural components, such as beams and columns, due to the method's efficiency in producing high-strength parts.
Challenges and Innovations
Despite its numerous benefits, sand casting is not without challenges. Surface finish and dimensional accuracy can sometimes be concerns, particularly when compared to more precise methods like investment casting. However, advancements in technology and materials are constantly improving sand casting processes. Innovations such as computer-aided design (CAD) and computer numerical control (CNC) machining are increasingly being integrated into the sand casting workflow, enhancing precision and efficiency.
Conclusion
In summary, sand casting remains a fundamental process in modern manufacturing, valued for its versatility, cost-effectiveness, and ability to produce complex geometries. As industries continue to evolve, the sands of time reveal that this ancient technique will likely adapt and thrive, playing a crucial role in the production of a diverse array of components for years to come. Understanding the intricacies of sand casting not only highlights its significance in the manufacturing landscape but also underscores the importance of continual innovation in this field.
Post time:Oktoba . 11, 2024 09:09
Next:foundry molding sand