Foundry Molding Sand An Essential Component in Metal Casting
Foundry molding sand plays a crucial role in the metal casting industry, serving as the primary medium for forming molds into which molten metal is poured. The properties and quality of this sand can significantly influence the final product, making it a key consideration for foundries worldwide. Understanding the characteristics, types, and processing of molding sand is essential for achieving high-quality castings.
Types of Foundry Molding Sand
The most commonly used molding sand is silica sand, owing to its abundance and favorable properties. Silica sand is composed primarily of silicon dioxide (SiO2) and is highly valued for its thermal stability, strength, and refractoriness. However, foundries may also utilize other types of molding sand, such as clay-based sand, resin-coated sand, and synthetic sands.
Clay-based sands, particularly those combined with bentonite clay, are widely used for their ability to retain moisture, which enhances the sand's plasticity and strength. This type of molding sand is often used for producing green sand molds, where the mold is not baked or dried before casting. On the other hand, resin-coated sands are treated with phenolic or furan resins, which provide superior strength and surface finish, making them ideal for intricate designs and thin-walled castings.
Properties of Molding Sand
foundry molding sand
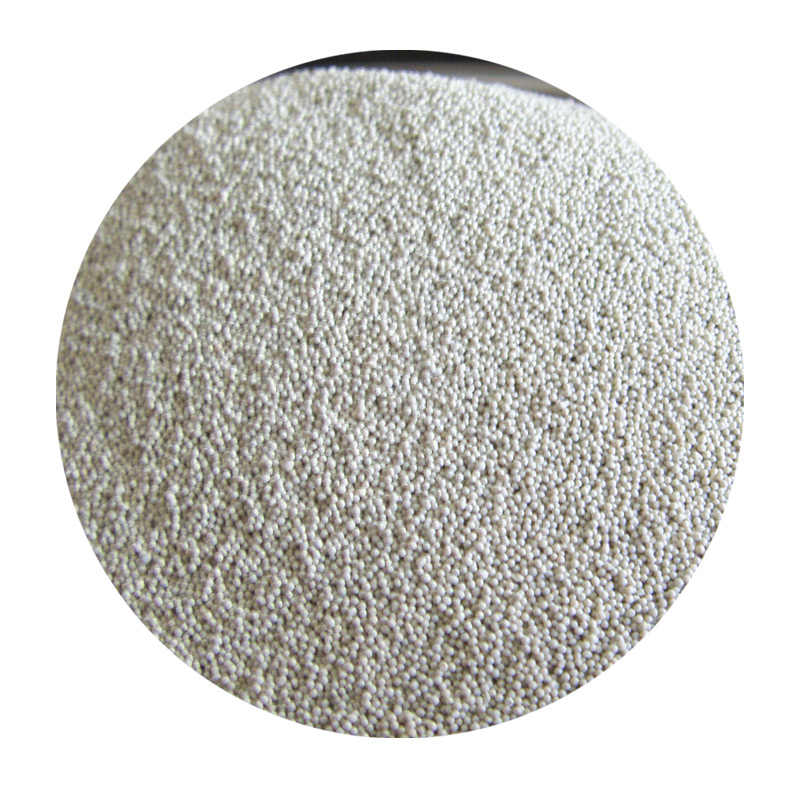
The effectiveness of foundry molding sand is determined by several key properties, including grain size, grain shape, moisture content, and bonding strength
. The grain size influences the surface finish and detail of the casting; finer grains produce smoother surfaces while coarser grains can enhance strength but may lead to rougher surfaces. The shape of the sand grains is also significant; round grains typically flow better and provide more uniform density in the mold.Moisture content is another critical factor, as it affects the sand’s ability to retain shape and resist the pressure of the molten metal. There is an optimal moisture range that foundries must maintain to ensure proper sand behavior. Additionally, the bonding strength is essential to hold the mold together under the weight of the molten metal, preventing deformation or collapse during the casting process.
Processing and Reclamation
After use, molding sand can be reclaimed and reused, making it a cost-effective material in the foundry industry. Modern foundries have developed sophisticated reclamation processes involving mechanical and thermal methods to remove impurities and restore the sand's desirable properties. This not only enhances sustainability but also reduces the overall environmental impact of sand extraction and processing.
Conclusion
In summary, foundry molding sand is a vital material in the metal casting process, influencing the quality and characteristics of the final product. Understanding the different types, properties, and processing techniques of molding sand enables foundries to optimize their operations and ensure the production of high-quality castings. As the industry evolves, innovations in molding sand technology will continue to play a significant role in enhancing casting performance and sustainability.
Post time:Oktoba . 11, 2024 08:52
Next:Techniques for Achieving Smooth Finishes on 3D Printed Models