Materials Used in Sand Casting
Sand casting is a widely used metal casting process that involves pouring molten metal into a sand mold to create a desired object. This technique is favored for its versatility and cost-effectiveness, making it suitable for both small-scale and large-scale productions. The materials used in sand casting play a critical role in the overall quality and success of the final product. This article explores the key materials used in the sand casting process, including sand, binders, additives, and the metals themselves.
Sand
The primary material in sand casting is the sand used to create the mold. Typically, silica sand is preferred due to its high melting point and excellent flowability. Silica sand contains a high percentage of silicon dioxide, making it resilient under high temperatures. Additionally, the grain size of the sand influences the surface finish and dimensional accuracy of the cast object. Coarse sand can create a rougher finish, whereas finer grains provide a smoother surface. Moreover, the shape of the sand grains also affects the packing density and permeability of the mold, which is crucial for gas escape during the casting process.
Binders
To hold the sand grains together and ensure the integrity of the mold, binders are used in the sand mixture. The most common binder in sand casting is clay, particularly bentonite clay, which has excellent adhesive properties. Mixing clay with sand creates a plasticity that allows the mold to retain its shape while enabling easy removal after casting. In addition to clay, other binders such as chemical binders or resin-coated sand are employed in specific applications to enhance mold strength and reduce the need for moisture. These alternatives can improve the dimensional accuracy of complex shapes, although they may come at a higher cost.
what materials are used in sand casting
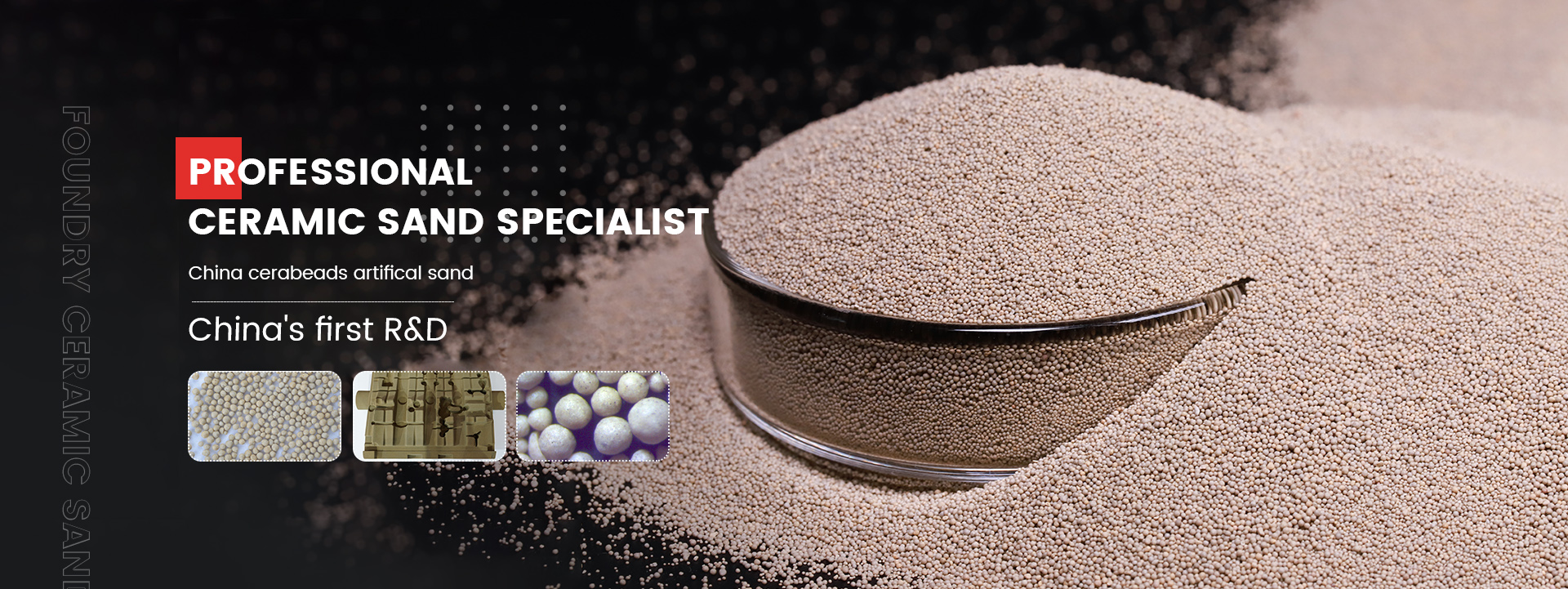
Additives
Various additives may also be incorporated into the sand mixture to enhance specific properties of the mold. For instance, coal dust or carbon can be added to improve the thermal conductivity of the mold, which helps in achieving a better surface finish. Other additives might include additives for controlling the moisture content or improving flow characteristics. The choice of additives truly depends on the requirements of the casting, such as the desired surface finish and mechanical properties of the final product.
Metals
The final component of the sand casting process is the molten metal that is poured into the mold. A variety of metals can be used in sand casting, including cast iron, aluminum, bronze, and steel. The choice of metal depends on the application and desired characteristics of the final product, such as strength, ductility, and corrosion resistance. Each metal has its own melting temperature and properties, influencing the overall process and the quality of the cast piece. Care must be taken to match the mold material, binder, and metal to ensure compatibility throughout the casting process.
Conclusion
In conclusion, the materials used in sand casting—sand, binders, additives, and metals—are integral to the success of the casting process. Understanding the properties and interactions of these materials allows manufacturers to optimize the casting process for various applications. As technology advances, the development of new materials and techniques continues to enhance the capabilities of sand casting, making it a valuable process in modern manufacturing.
Post time:Aug . 29, 2024 17:55
Next:sand casting cast iron