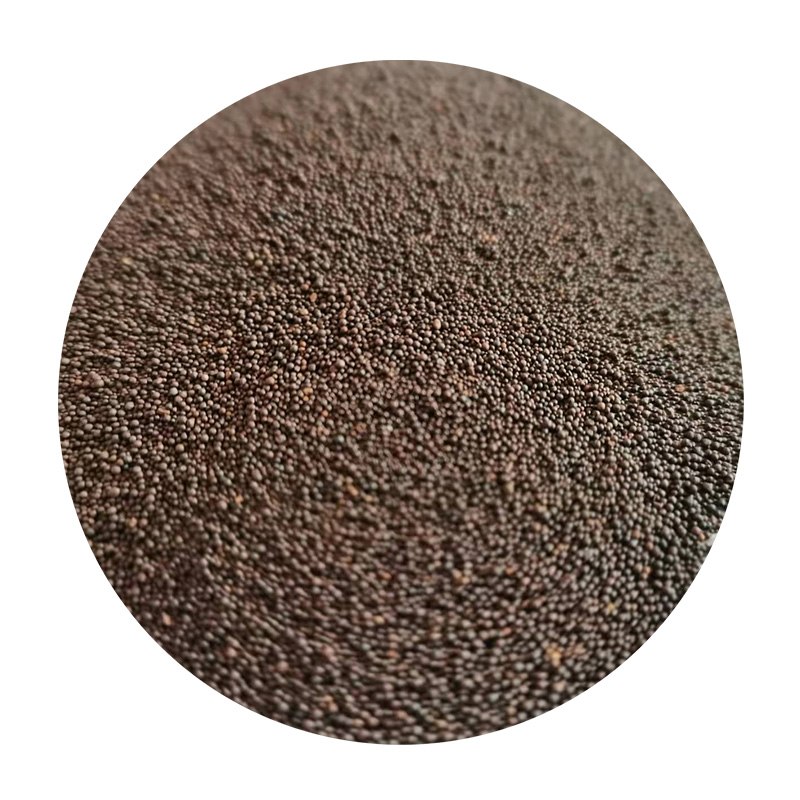
different types of sand casting. The shell mold is then heated to remove the pattern and create a cavity that is filled with molten metal. Shell molding is often used for high-precision parts that require a smooth surface finish. Investment casting is a type of sand casting that involves creating a wax pattern, coating it with a ceramic shell, and then melting out the wax to leave a hollow cavity that is filled with molten metal. Investment casting is often used for complex parts that require tight tolerances and a high level of detail. Each type of sand casting has its own advantages and limitations, and the choice of technique will depend on factors such as the size and complexity of the part, the desired surface finish, and the volume of production. Regardless of the type of sand casting used, the process relies on the ability of the sand mold to hold its shape and withstand the heat and pressure of the molten metal as it is poured into the cavity. In conclusion, sand casting is a versatile and cost-effective method of metal casting that offers a wide range of options for producing metal components. By understanding the different types of sand casting techniques available, manufacturers can choose the best method for their specific needs and achieve the desired outcome for their project. Post time:Jul . 12, 2024 02:41
Next:Materials used in the lost foam casting process for creating intricate metal products