The Steel Sand Casting Process An Overview
Steel sand casting is a widely used manufacturing process that combines the qualities of steel with the versatility of sand molds to produce intricate and robust metal components. This traditional yet effective technique has been employed in various industries, from automotive to aerospace, due to its ability to create complex shapes with excellent dimensional accuracy.
Understanding the Sand Casting Process
At its core, the sand casting process involves creating a mold from a mixture of sand, clay, and water. The process begins with the production of a pattern, which is a replica of the final object to be cast. This pattern is usually made of metal, plastic, or wood, and its dimensions are slightly larger than the final product to account for shrinkage during cooling.
Once the pattern is ready, it is placed within a flask, a container that holds the sand mix. The sand is then compacted around the pattern, and once it hardens, the pattern is removed, leaving a cavity that mirrors the shape of the original pattern. This empty cavity is what will be filled with molten steel.
Preparation and Pouring
Before pouring, the sand mold might undergo a process called core making, where additional sand shapes are created to form internal passages or hollow sections in the casting
. These cores are placed into the mold to ensure that the final product meets design specifications.The next step involves melting the steel at high temperatures, typically in an electric arc furnace or a induction furnace, where it reaches the desired temperature for pouring. The molten steel is then carefully poured into the prepared sand mold, filling the cavity created by the pattern. This stage requires skill, as controlling the flow of molten metal is crucial to prevent defects such as air pockets or incomplete fillings, which can compromise the strength and integrity of the final casting.
steel sand casting process
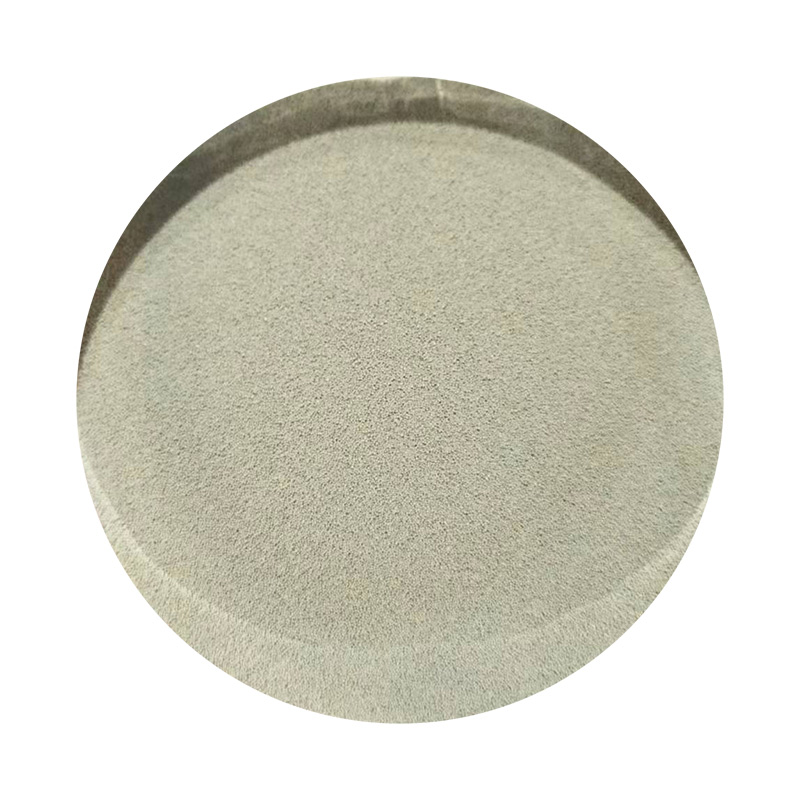
Cooling and Finishing
After the molten steel is poured, it needs time to cool and solidify. The cooling rate can affect the microstructure of the steel, which in turn influences its mechanical properties. Once the steel has cooled sufficiently, the sand mold is broken away to reveal the casting. This stage is usually followed by several finishing processes, including trimming excess material, grinding, and surface treatment to achieve the desired finish and tolerances.
Advantages and Applications
One of the primary advantages of steel sand casting is its adaptability. It can produce a wide range of parts with varying sizes and geometries, making it suitable for prototyping as well as large-scale production. The process can also accommodate various steel grades, including carbon steel, alloy steel, and stainless steel, allowing for versatility in application.
Some of the common applications of steel sand casting include the manufacture of engine blocks, pump housings, gear housings, and various components in the construction and machinery sectors. The durability and strength of steel castings make them ideal for heavy-duty applications subjected to high stress and wear.
Conclusion
In conclusion, steel sand casting is an essential process in modern manufacturing, marrying traditional methods with contemporary engineering designs. Its ability to produce complex steel components with exceptional strength and durability ensures its continued relevance across multiple industries. As technology advances, innovations in materials and techniques are likely to further refine the steel sand casting process, paving the way for even more sophisticated applications in the future.
Post time:Aug . 18, 2024 14:51
Next:Advantages of Sand Casting in Manufacturing Processes and Its Impact on Production