Understanding Foundry Sand Significance and Applications
Foundry sand is a key material used in the metal casting industry, playing an essential role in the production of various complex metal components. Its unique properties and significance in the manufacturing process make it a valuable resource, impacting the quality of cast products while also influencing the economic and environmental aspects of foundry operations.
What is Foundry Sand?
Foundry sand primarily refers to high-quality silica sand that has been specifically treated to ensure it meets the rigorous demands of the casting process. It is characterized by its fine grain, high strength, and ability to retain moisture, making it ideal for use in the molding and core-making processes. Foundry sand can be classified into two main types green sand and resin-bonded sand. Green sand consists of silica sand mixed with clay and water, creating a moldable mass suitable for many metal casting applications. In contrast, resin-bonded sand uses synthetic resins as a binder, which hardens through a chemical reaction when exposed to heat.
Properties of Foundry Sand
The effectiveness of foundry sand is largely dependent on its physical and chemical properties. Silica content is paramount, as it directly affects the strength and thermal stability of the molds. The grain shape and size distribution also play a crucial role; well-graded sands with round grains perform better than angular, poorly sorted sands. Additionally, the refractoriness of the sand is critical, ensuring it can withstand the extreme temperatures of molten metal without breaking down.
Applications in Metal Casting
foundry sand meaning
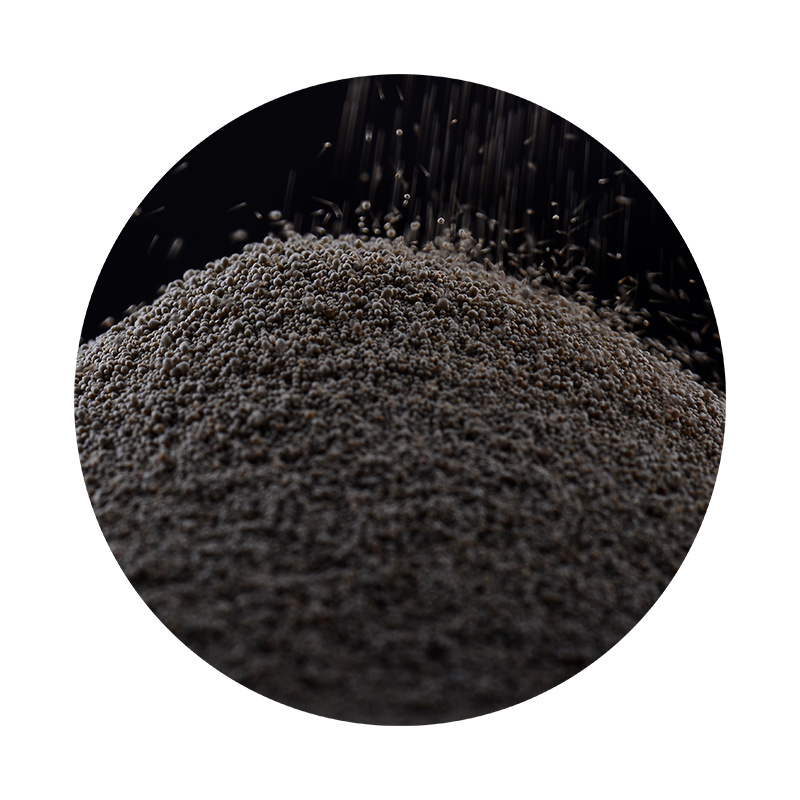
Foundry sand serves multiple functions in metal casting. As a molding material, it supports the hundreds of tons of metal that may be poured into a mold. It allows for intricate shapes and details to be reproduced faithfully, ensuring the final products meet precise specifications. The sand also aids in the cooling process of cast metals, influencing the strength and surface quality of the finished parts. Castings produced with foundry sand are utilized in various industries, including automotive, aerospace, and manufacturing, underscoring its importance across multiple sectors.
Economic Impact
The economic implications of foundry sand are significant. Using this material can drastically reduce production costs and improve operational efficiency by allowing faster mold-making and casting processes. Recycling foundry sand has become a vital practice in the industry. Traditionally, spent foundry sand has been disposed of in landfills, posing environmental challenges. However, with innovative recycling methods, spent foundry sand can be reprocessed and reused in various applications, including construction and roads, thereby reducing waste and lowering material costs.
Environmental Considerations
Sustainable practices in foundry operations are increasingly vital, and foundry sand recycling contributes positively to this effort. The reuse of sand not only conserves natural resources but also minimizes the environmental footprint of foundry operations. Additionally, because foundry sand is predominantly composed of silica, its reuse in other industries helps mitigate the demand for raw material extraction, thereby preserving ecosystems.
Conclusion
In summary, foundry sand is a critical material in the metal casting industry, offering unique properties that enhance the quality and efficiency of manufacturing processes. Its applications extend beyond traditional casting to innovative recycling efforts that promote sustainability. As the foundry industry continues to evolve, the importance of foundry sand in enhancing production methods and contributing to environmental sustainability cannot be overstated. Understanding its role opens avenues for further innovation and improvement in industrial practices, securing its place as a fundamental component in modern manufacturing.
Post time:Aug . 15, 2024 10:38
Next:Exploring the Innovations and Applications of Sand-Based 3D Printing Technology in Various Industries