The Sand Foundry Process A Comprehensive Overview
The sand foundry process plays a critical role in the manufacturing industry, particularly in the production of metal castings. This age-old method is characterized by its ability to produce complex shapes with high precision and is favored for its cost-effectiveness and versatility. This article aims to explore the key stages of the sand foundry process, its applications, and the advantages it offers.
Understanding Sand Casting
Sand casting, the primary method used in the sand foundry process, involves creating a mold from a mixture of sand and a binding agent, usually clay, mixed with water. The process begins by designing the pattern, which is a replica of the final product, often made from wood, metal, or plastic. The pattern is used to create an impression in the sand mixture, forming the mold cavity.
The Mold Creation
The first step in the sand foundry process involves preparing the mold. The sand is compacted around the pattern, often in a two-part mold (cope and drag) to allow for easy removal. The ability to reuse sand, combined with its high melting point, makes it an ideal choice for casting various metals including aluminum, iron, and bronze.
Once the sand is compacted around the pattern, the sand mold is carefully removed to reveal the cavity. To ensure the accuracy of the final product, the mold is checked for defects, any necessary adjustments are made to ensure a smooth surface. The two halves of the mold are then secured in place before the molten metal is poured.
Pouring and Cooling
The next stage in the sand foundry process is the pouring of molten metal into the mold. Care must be taken to control the temperature of the metal and the pouring speed, as these can significantly impact the quality of the casting. Once the metal is poured, it is allowed to cool and solidify, a process which can take several minutes to hours depending on the thickness of the casting.
sand foundry process
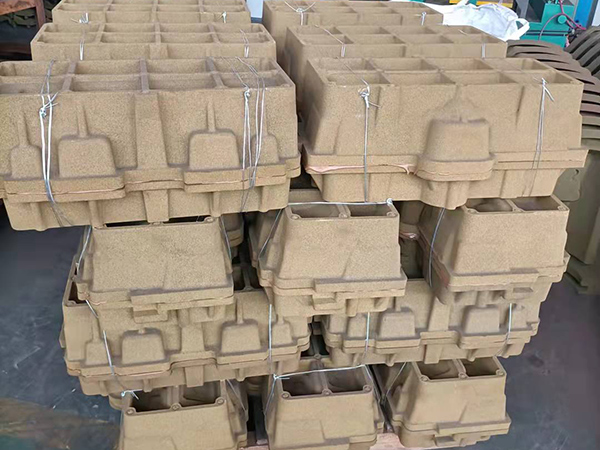
During the cooling phase, reactions may occur between the metal and the sand, which can lead to various casting defects if not correctly managed. To mitigate these potential issues, foundries often conduct thorough testing and quality checks throughout the manufacturing process.
Finishing Touches
After the metal has cooled and solidified, the next step is to remove the casting from the mold. This is done by breaking away the sand, a process that can be facilitated by mechanical vibration or manual methods. Once the casting is removed, it typically requires further processing, such as trimming, grinding, or machining, to achieve the desired finish and dimensions.
Applications and Advantages
The applications of the sand foundry process are vast and varied, ranging from automotive parts to industrial machinery, and even artistic sculptures. Its popularity can be attributed to several key advantages. First, the process allows for the creation of intricate designs that would be difficult or impossible to achieve with other manufacturing methods. Additionally, the use of sand as a mold material is affordable, making the process economically viable for both large-scale production and smaller operations.
Moreover, sand molds can be reused multiple times, contributing to sustainability and reducing waste in the manufacturing cycle. The sand foundry process also accommodates various metal types, making it versatile for different industries.
Conclusion
In conclusion, the sand foundry process remains a cornerstone of metal casting technology, offering a blend of precision, cost-effectiveness, and versatility. As industries continue to evolve, the sand foundry process is likely to adapt and innovate, solidifying its relevance in modern manufacturing. Whether it’s crafting essential components for vehicles or creating unique art pieces, the sand foundry process will continue to play a vital role in shaping the materials we rely on daily.
Post time:Aug . 06, 2024 07:57
Next:Benefits of Sand Casting in Modern Manufacturing Processes and Its Impact on Efficiency