Sand Casting A Fundamental Metal Casting Process
Sand casting, also known as sand molded casting, is one of the oldest and most widely used metal casting processes. It has been a fundamental method employed in various industries for producing metal parts due to its simplicity, adaptability, and cost-effectiveness. This process is particularly favored for its ability to create complex shapes and large components that require minimal tooling.
The basic principle of sand casting involves creating a mold from a mixture of sand, clay, and water. The process begins with designing a pattern, typically made from materials such as metal, plastic, or wood, which resembles the desired final product. This pattern is used to create a cavity in the sand mixture, which forms the mold where the molten metal will be poured.
Sand Casting A Fundamental Metal Casting Process
One of the primary advantages of sand casting is its flexibility in producing parts of various sizes and geometries. It is capable of accommodating intricate designs that may be challenging to achieve through other manufacturing methods. Additionally, because the mold can be easily altered or remade, sand casting is an ideal process for prototypes or low-volume production runs.
sand casting metal process
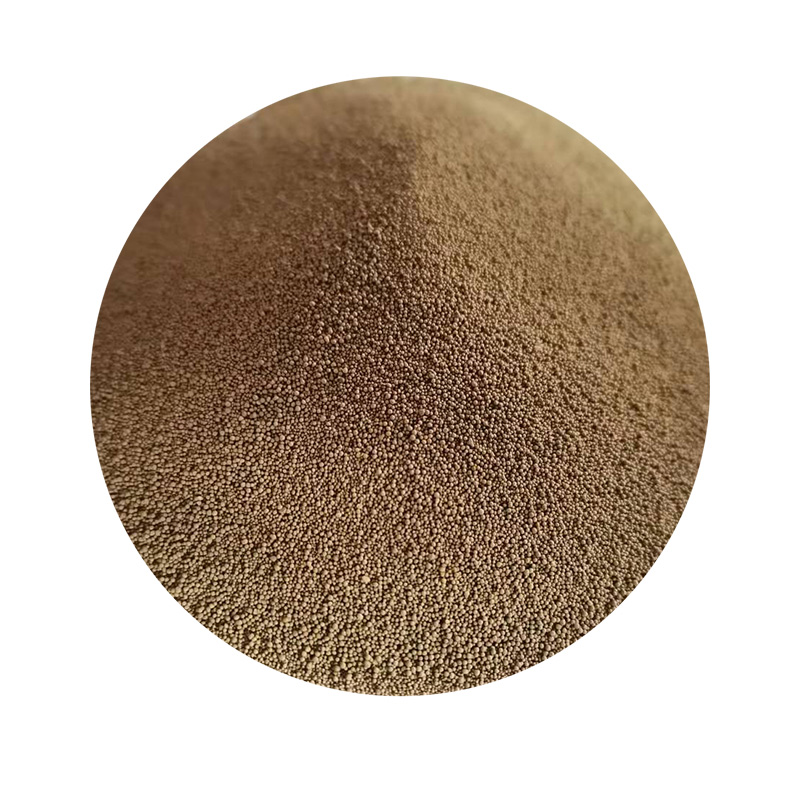
The next stage involves melting the metal, which can be aluminum, iron, bronze, or other alloys, depending on the specifications of the final product. The molten metal is then carefully poured into the cavity of the mold through a gating system designed to control the flow and minimize defects.
After the molten metal cools and solidifies, the sand mold is broken apart to reveal the cast component. This stage requires care to prevent damage to the newly formed part. The resulting casting generally requires additional finishing processes, such as sandblasting, machining, or surface treatments, to achieve the desired surface quality and dimensions.
Despite its many benefits, sand casting is not without its limitations. One of the significant challenges is the potential for defects such as sand inclusions, porosity, or dimensional inaccuracies. To mitigate these issues, careful attention must be paid to the mold design, sand mixture, and pouring techniques. Modern advancements in technology, such as computer simulations and improved materials, have significantly enhanced the consistency and quality of sand castings.
In conclusion, sand casting remains a cornerstone of the metalworking industry, providing a reliable and cost-efficient method for producing a wide variety of metal components. Its versatility and capability to fabricate complex shapes make it indispensable, especially in sectors like automotive, aerospace, and general manufacturing. As technology evolves, sand casting continues to adapt, integrating new techniques and materials that enhance its efficiency and product quality. Whether crafting large industrial components or intricate designs for specialized applications, sand casting is an enduring process that meets the demands of modern manufacturing.
Post time:Aug . 12, 2024 12:34
Next:Exploring Various Materials Employed in the Sand Casting Process for Improved Manufacturing Efficiency