Sand in Casting The Backbone of Metal Foundry Processes
Casting is a pivotal manufacturing process that allows the production of complex shapes and components in various industries, from automotive to aerospace. At the heart of this process lies an essential material sand. Known for its unique properties, sand plays a fundamental role in shaping and forming metal castings. This article delves into the significance of sand in casting, discussing its types, processes, and the advantages it brings to metal foundry operations.
Types of Sand Used in Casting
The two primary types of sand used in casting are green sand and resin-coated sand. Green sand, a mix of sand, clay, and water, is the most common type in foundries. This versatile medium retains moisture, allowing it to be easily molded into intricate shapes. The clay present in green sand provides binding properties, which lend strength to the mold and enable it to withstand the pressure of molten metal.
On the other hand, resin-coated sand is often utilized in more precise applications. This type of sand is coated with a resin that hardens when heated, forming a strong mold. The accuracy and surface finish of parts produced using resin-coated sand are generally superior to those made with green sand. Each type of sand offers unique properties that can be tailored to the specific requirements of various casting processes.
The Casting Process
The casting process generally begins with the preparation of the sand mold. In green sand casting, a pattern of the desired part is placed in a mold box, and the green sand is packed around it. The pattern is removed, leaving a cavity into which molten metal will be poured. In resin-coated sand casting, the sand mix is formed around the pattern, heated to harden the resin, and then the pattern is pulled out, creating a mold.
sand in cast
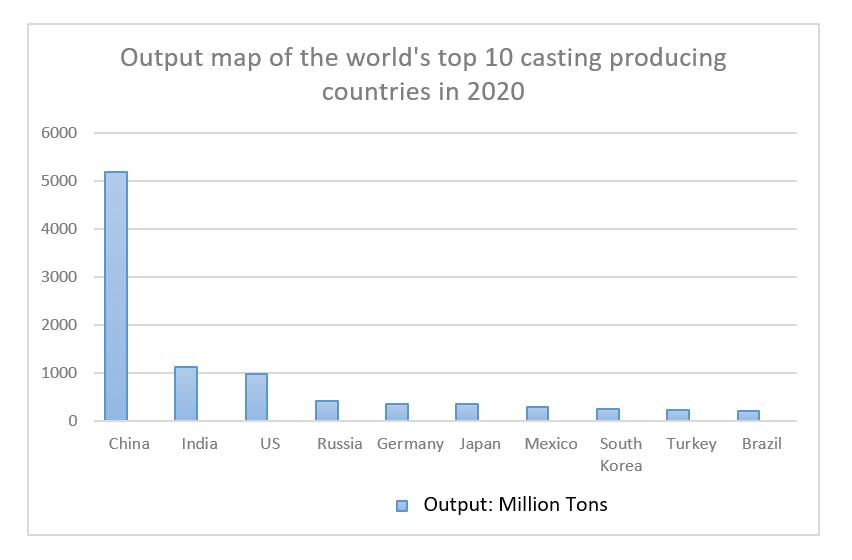
Once the molds are prepared, the next step involves melting the metal. Different metals, including aluminum, iron, and bronze, can be used, each with specific melting points and characteristics. The molten metal is then poured into the mold cavity, where it takes the shape of the pattern. After the metal has cooled and solidified, the sand mold is broken away to reveal the cast part.
Advantages of Using Sand in Casting
Sand as a molding material offers several distinct advantages. Firstly, it is readily available and cost-effective. This affordability makes it an ideal choice for large production runs and various casting applications. Secondly, sand has high thermal conductivity, enabling it to withstand the temperatures of molten metals without significant breakdown. This property is crucial for producing detailed and accurate castings.
Moreover, the recycling capability of sand enhances its sustainability in manufacturing. After casting, the sand can be cleaned and reused multiple times, thereby reducing waste and the need for new materials. This is particularly beneficial in modern foundries striving for environmentally friendly practices.
Conclusion
In summary, sand is an indispensable material in the casting process, providing both versatility and practicality. Its various types cater to different casting requirements, while its unique properties enhance the strength, accuracy, and cost-effectiveness of the final products. As technology advances and the demand for precise casting increases, the role of sand in casting will continue to evolve, ensuring that it remains a cornerstone of metal foundry operations worldwide. The future may even see innovations in sand formulations and recycling methods, further solidifying its place in the manufacturing landscape.
Post time:Aug . 09, 2024 05:00
Next:A Journey Through the Enchanting World of Sand and Its Mystical Cast Characters