The Resin Sand Casting Process An Innovative Approach to Metal Casting
Resin sand casting is a modern and efficient method used in the foundry industry for producing metal castings with high precision and excellent surface finishes. This process is characterized by its unique use of resin-bonded sand, which offers several advantages over traditional green sand casting methods. In this article, we will explore the key elements of the resin sand casting process, its benefits, and its applications in various industries.
The Process
The resin sand casting process begins with the preparation of the molding sand. This sand is composed of fine silica sand mixed with a phenolic resin binder and a hardener. Unlike traditional sand casting, which uses water to bind the sand, the resin provides superior strength and stability. The mixture is thoroughly blended to achieve a uniform consistency.
Once the sand mixture is prepared, it is packed into a mold box around a pattern of the desired casting. The pattern is often made of metal or plastic and is designed to create the exact shape of the final product. The resin binder is activated through heat, which cures the sand mixture, creating a solid mold. This curing process typically occurs at temperatures ranging from 150°C to 200°C (302°F to 392°F), allowing for rapid mold production and turnover.
After the mold has been cured, the pattern is removed, leaving a hollow cavity that corresponds to the shape of the desired casting. The mold can then be assembled, and molten metal is poured into the cavity. Once the metal has cooled and solidified, the mold is broken away to reveal the final casting.
Advantages
One of the most significant advantages of resin sand casting is the superior surface finish it provides. The use of resin allows for tighter tolerances and reduces the need for extensive machining, which can save both time and costs. Additionally, resin sand molds can withstand higher pouring temperatures, enabling the use of a wider range of metals.
resin sand casting process
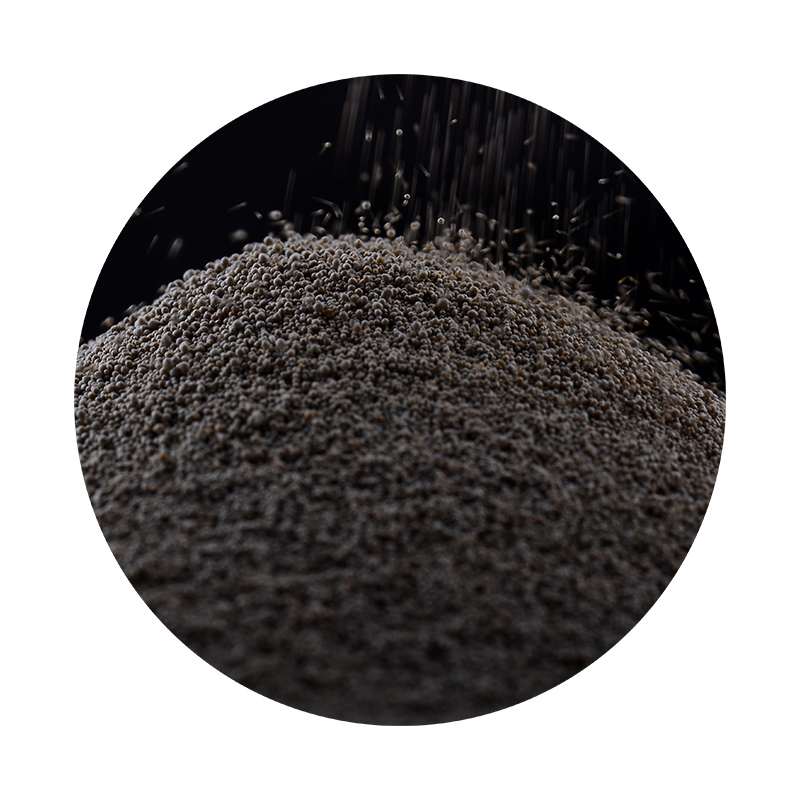
Another key benefit is the speed of the process. The rapid curing time of resin sand allows for faster production cycles, which is particularly valuable in industries requiring high volumes of casting in short time frames. Resin sand casting also produces less waste, as molds can be reused multiple times, contributing to sustainability efforts in manufacturing.
The process is also highly versatile, capable of producing complex shapes and intricate designs. This versatility has made resin sand casting a popular choice in various industries, including automotive, aerospace, and machinery manufacturing. Its ability to replicate fine details and features has led to the production of high-quality components that meet rigorous industry standards.
Applications
Resin sand casting is widely used in the automotive industry for producing engine blocks, transmission housings, and other critical components. Its ability to provide precise dimensions and smooth surfaces is essential for the performance and safety of these parts. In the aerospace sector, parts produced through resin sand casting are subject to strict regulations, making this method ideal for creating lightweight yet robust components that can withstand extreme conditions.
Moreover, the construction of intricate molds makes resin sand casting suitable for artistic applications, such as sculptures and decorative elements. Its adaptability to different materials allows artists and designers to explore innovative designs that push the boundaries of traditional casting methods.
Conclusion
In conclusion, resin sand casting is a sophisticated method that brings together efficiency, precision, and versatility in metal casting production. Its advantages over traditional techniques make it an indispensable tool in various industries, driving innovation and enhancing the quality of manufactured components. As technology and materials continue to evolve, the resin sand casting process is likely to play an even more significant role in the future of manufacturing.
Post time:Aug . 13, 2024 23:53
Next:Innovative Techniques and Applications in Resin Bonded Sand Casting for Enhanced Metal Casting Performance