The Resin Sand Casting Process An Overview
Resin sand casting, also known as resin-bonded sand casting, is a highly versatile and efficient metal casting process that combines traditional sand casting techniques with modern advancements in materials science. This method is favored across various industries due to its ability to produce high-quality castings with excellent dimensional accuracy and surface finish. The resin sand casting process has several distinct advantages, making it an integral part of modern manufacturing.
At the heart of the resin sand casting process is the use of a special synthetic resin that binds sand grains together. Unlike traditional green sand casting, which relies on moisture as a binder, resin sand casting utilizes a two-part resin system that can be cured through heat. This innovation allows for the production of molds that are not only strong and durable but also capable of withstanding higher temperatures during metal pouring.
The process begins with the preparation of the sand mixture. Fine silica sand is combined with a thermosetting resin and a hardening catalyst. The mixture is then thoroughly blended to ensure that each sand grain is coated with the resin. This uniform coating is crucial for achieving the desired properties in the final mold. Once the sand is mixed, it is typically compressed into a mold using a pattern, which can be made of metal, plastic, or any other suitable material.
One of the key benefits of using resin sand is its ability to create intricate and complex geometries. The molds produced can capture fine details and produce smooth surface finishes that often require little to no additional machining. This is particularly advantageous in industries where precision is critical, such as automotive, aerospace, and heavy machinery.
resin sand casting process
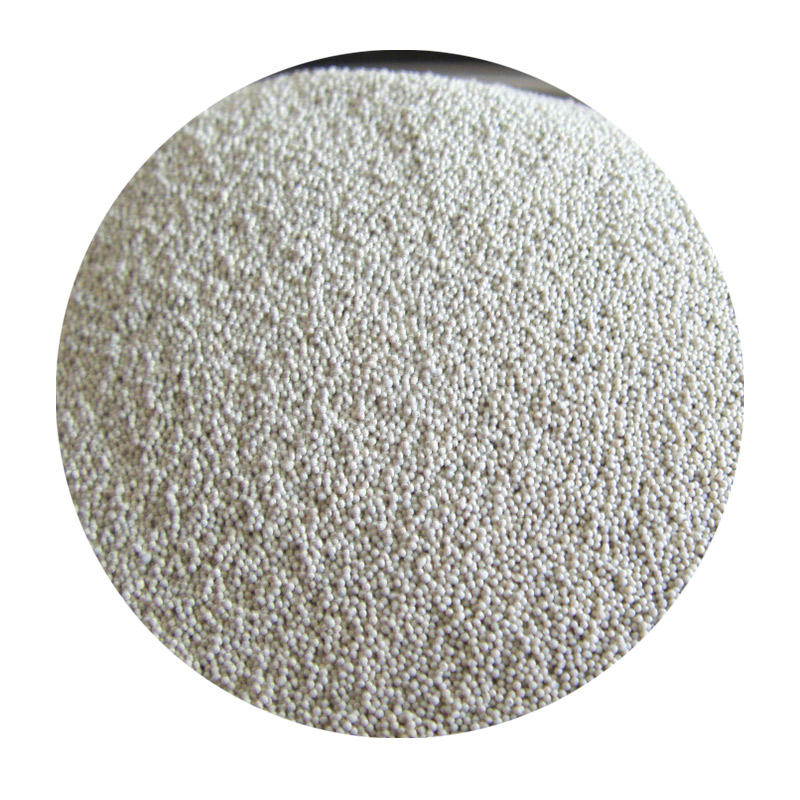
After the mold is formed, it undergoes a curing process, usually achieved through the application of heat. The heat activates the chemical reaction in the resin, hardening the binder and forming a sturdy mold. This curing process dramatically reduces the time required to produce a mold compared to conventional methods, leading to shorter production cycles and increased efficiency.
Once the mold is ready, metal is poured into it, typically in liquid form. Common metals used in resin sand casting include iron, aluminum, and various alloys. The molten metal fills the cavity created by the mold, taking on its shape as it cools and solidifies. After the metal has cooled sufficiently, the mold is carefully broken away to reveal the finished casting.
Post-processing of the castings may be necessary, depending on the application. This could involve operations such as sandblasting, machining, or surface finishing to enhance the appearance and performance of the final product. Nevertheless, many users of resin sand casting find that the initial surface finish is often satisfactory enough for certain applications, saving time and cost in production.
In summary, resin sand casting is a dynamic and efficient method for producing high-quality metal castings. With its ability to create complex shapes and provide superior surface finishes, it remains an invaluable process in the manufacturing industry. As technology continues to advance, the resin sand casting process will likely evolve, offering even more capabilities and efficiency for future applications. Whether in the production of intricate automotive components or robust industrial parts, resin sand casting has firmly established itself as a preferred choice for manufacturers seeking reliability and precision in their casting needs.
Post time:Aug . 08, 2024 04:15
Next:Understanding the Process and Techniques Involved in Sand Casting for Metal Parts Production