The Importance of Foundry Sand in Metal Casting
Foundry sand is a fundamental component in the metal casting industry, playing a crucial role in the production of various metal components and products. This specialized sand is primarily used in molding and core-making processes, allowing manufacturers to create intricate shapes with high precision and excellent surface finish. With its unique properties, foundry sand contributes to the efficiency and quality of metal casting operations, making it an essential material in manufacturing.
What is Foundry Sand?
Foundry sand is a high-quality silica sand that has been processed to meet specific industry standards. It is characterized by its grain shape, size, and purity, which are critical properties that affect its performance in foundry applications. The most commonly used type of foundry sand is silica sand, which can withstand high temperatures and possesses excellent thermal conductivity. This makes it suitable for casting metals such as iron, aluminum, and steel.
Types of Foundry Sand
There are several types of foundry sand based on their composition and treatment
. The most common types include1. Green Sand This is a mixture of sand, clay, and water, and is one of the most traditional forms of foundry sand. It is easy to mold and recycle, making it cost-effective for many foundries.
2. Furan Resin Sand This type of sand uses a furan resin binder, providing superior surface finish and dimensional accuracy. It can be used for complex shapes and intricate designs.
foundry sand pdf
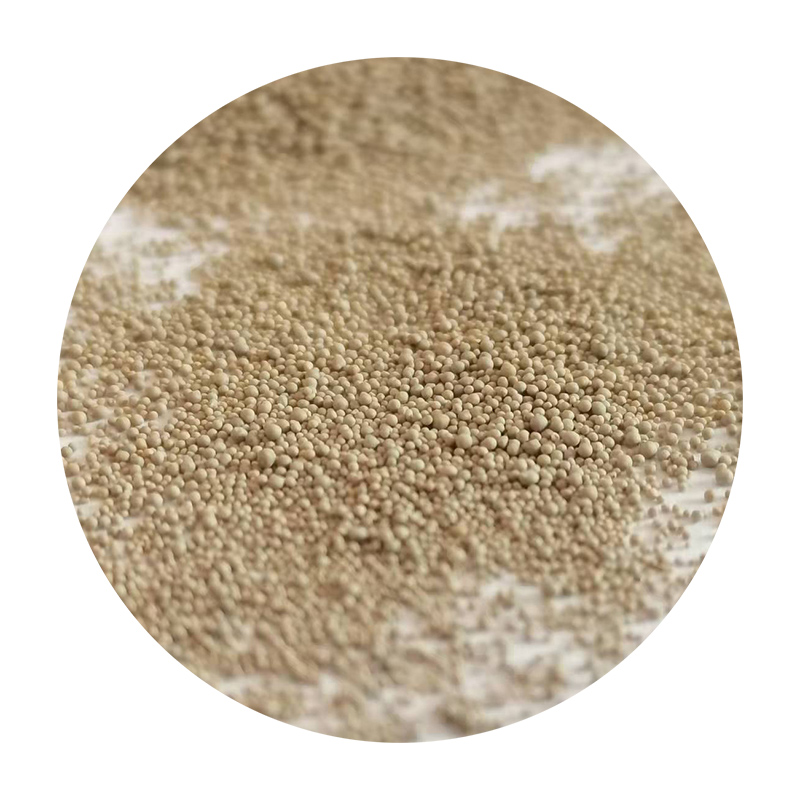
3. Synthetic Sand Manufactured sand that is engineered to closely mimic natural sands, offering consistent quality and properties. It is increasingly popular due to its environmental advantages and reusability.
4. Chromite Sand Known for its unique high thermal stability, chromite sand is often used for casting high-performance alloys and in steel foundries.
Application of Foundry Sand
The primary application of foundry sand is in the production of molds and cores used in the metal casting process. The sand mixture is formed into a mold that encases the metal; once poured, the sand holds the shape until the metal cools and solidifies. Foundry sand also aids in creating cores, which are used to form internal cavities in cast parts, allowing for complex shapes without compromising structural integrity.
Environmental Considerations
While foundry sand plays a vital role in casting processes, it is essential to address environmental concerns associated with its use. After it has been utilized in casting, foundry sand can often be recycled and reused in different applications, reducing waste and promoting sustainability. Many foundries have adopted practices that minimize the environmental impact of foundry sand disposal, repurposing it for construction projects, land reclamation, and other uses.
Conclusion
In summary, foundry sand is an indispensable material in the metal casting industry, providing the necessary properties for high-quality molds and cores. Its versatility, coupled with the ability for recycling and reuse, makes it a valuable resource for effective and sustainable manufacturing processes. As technology continues to advance in the foundry sector, the development of new sand mixtures and recycling techniques will further enhance the efficiency and environmental friendliness of metal production, solidifying the role of foundry sand in modern casting practices.
Post time:Aug . 14, 2024 04:26
Next:Exploring the Effects of Sand Sintering on Material Properties and Applications in Engineering