Understanding How Sand Casting Works
Sand casting is one of the oldest and most versatile metal casting processes, widely used in manufacturing industries today. This method relies on the creation of a mold from sand mixed with a bonding agent to form shapes for metal casting. The simplicity and adaptability of sand casting have made it a favored choice for producing metal components across various sectors including automotive, aerospace, and machinery.
The Sand Casting Process
The sand casting process begins with the creation of a pattern. A pattern is a replica of the desired final product and is typically made from materials like metal, plastic, or wood. The pattern is used to form a mold cavity in which the molten metal will be poured. The mold is made up of two halves the cope (top half) and the drag (bottom half). These two halves create a complete mold when assembled.
Once the pattern is in place, sand is mixed with a bonding agent (usually clay and water) to create a mixture that can hold its shape. This sand mixture is packed around the pattern to form the mold. The packing process can be done manually or through mechanized methods. After the sand is packed tightly enough, the pattern is removed, leaving behind a cavity that matches the shape of the desired component.
Next, the two halves of the mold are assembled and any necessary gates and risers are added. Gates are channels that allow the molten metal to flow into the mold, while risers act as reservoirs to counteract shrinkage as the metal cools and solidifies. At this stage, the mold is ready to accept molten metal.
The choice of metal is crucial in sand casting, as various metals have different properties and solidification times. Common materials include aluminum, iron, and bronze. The metal is melted in a furnace and then poured into the mold through the gates. Depending on the metal's specific properties and the size of the cast, the cooling process can take anywhere from minutes to several hours.
how sand casting works
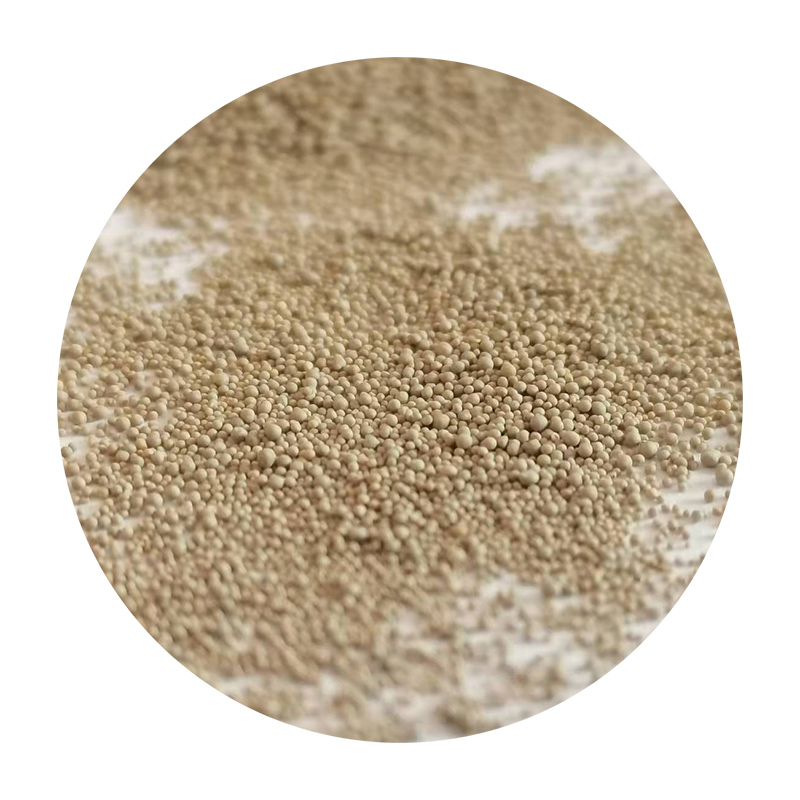
After the metal has solidified, the mold is broken apart to retrieve the casting. This process is often done with hammers or vibrating tables, given the strength of the sand mold. The quality of the cast component is then assessed, and any finishing processes such as grinding, polishing, or machining may be applied to meet the final specifications.
Advantages of Sand Casting
One of the primary advantages of sand casting is its cost-effectiveness, especially when it comes to low-volume production. The materials required, such as sand and commonly used bonding agents, are relatively inexpensive and readily available. Moreover, sand molds can be reused, which reduces waste and costs associated with material.
Sand casting also offers significant design flexibility. Complex shapes can be achieved with relative ease, accommodating intricate designs that would be challenging to produce using other methods. This ability to create diverse forms makes sand casting a preferred choice for custom parts, prototypes, and large components.
Additionally, it is worth noting that sand casting is capable of producing large parts that can weigh hundreds of tons, a capability that few other casting techniques can match.
Conclusion
In summary, sand casting is a time-honored process that combines simplicity, adaptability, and efficiency, making it an essential method in the manufacturing of metal components. Its ability to produce complex shapes at low costs plays a vital role in various industries, ensuring the continued relevance of sand casting in modern metalworking. As technology advances, innovations in sand casting techniques and materials promise to enhance the quality and capabilities of this traditional process, making it an exciting field for future developments.
Post time:Aug . 21, 2024 17:06
Next:Tips for Smoothing and Finishing Ceramic Surfaces Effectively