What is Sand Casting?
Sand casting, also known as sand mold casting, is a versatile and widely used metal casting process that involves using sand as a mold material. This technique has been utilized for thousands of years and remains popular in modern manufacturing due to its cost-effectiveness and the ability to create complex shapes with relative ease.
The Process of Sand Casting
The sand casting process typically consists of several key steps
1. Pattern Creation The first step in sand casting involves creating a pattern, which is an exact replica of the final part to be cast. Patterns can be made from various materials like wood, metal, or plastic. They are designed with some dimensional allowances to account for metal shrinkage during cooling.
2. Mold Preparation The next step is preparing the sand mold. The sand used in casting is usually a mixture of sand grains, clay, and water, which helps bind the grains together. The mold is created by packing this sand mixture tightly around the pattern to form a cavity. Once packed, the mold is split into two halves (cope and drag) for easy removal of the pattern.
3. Casting After the mold is prepared and the pattern is removed, the mold cavities are ready for pouring. Molten metal, heated to a specific temperature, is poured into the mold, filling the cavity to create the final shape. This step requires precision to avoid defects and ensure that the mold is filled completely.
4. Cooling and Solidification Once the molten metal is poured into the mold, it begins to cool and solidify. The cooling time depends on the thickness and type of metal being used. During this phase, it is essential to control the cooling process to avoid internal stresses and defects.
what is sand casting
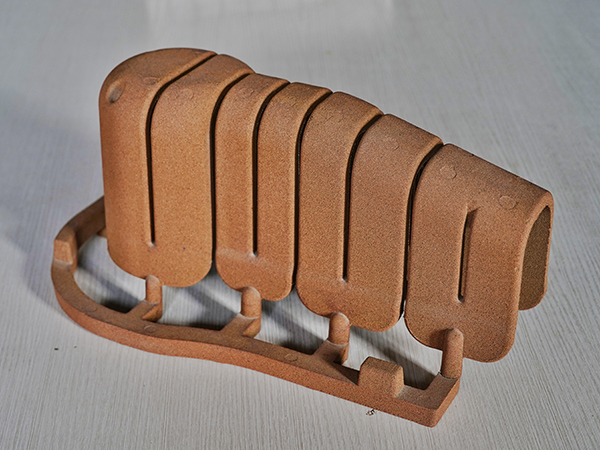
5. Mold Removal After the metal has cooled and solidified, the sand mold is broken apart to reveal the cast part. The sand can often be reused, making this a sustainable option for many foundries.
6. Finishing The final step in the sand casting process is finishing the cast part. This can involve cleaning, machining, and other processes to achieve the desired surface finish and tolerances.
Advantages of Sand Casting
Sand casting offers several advantages that make it a preferred choice in many industries
- Cost-effectiveness Compared to other casting methods, sand casting is relatively inexpensive, particularly for small to medium-sized production runs. - Versatility This method can be used to cast a wide range of metals and alloys, including aluminum, iron, and magnesium, allowing for flexibility in material choice. - Complex Geometries Sand casting is capable of producing intricate designs and shapes that would be challenging to achieve with other casting methods. - Low Initial Investment The tooling and equipment requirements for sand casting are less costly than those for processes like die casting, making it accessible for small businesses and startups.
Applications of Sand Casting
Today, sand casting is used in various industries, from automotive to aerospace, machinery, and art. It serves as a foundation for producing durable components, such as engine blocks, frames, and decorative items. Its capability to produce both short-run prototypes and larger production batches places it at the forefront of foundry operations.
In summary, sand casting is a fundamental metalworking process that combines simplicity with efficiency, making it a critical technique in manufacturing and engineering. Its enduring legacy and adaptability highlight its significant role in the evolution of casting technology, enabling designers and engineers to bring their ideas to fruition in a tangible form.
Post time:Aug . 13, 2024 18:24
Next:Exploring Diverse Applications and Benefits of Sand Casting in Modern Manufacturing Industries