Understanding Sand Casting Definition and Process
Sand casting is a widely used metal casting process that involves pouring molten metal into a mold made from sand. This process has been a cornerstone in manufacturing since ancient times, owing to its simplicity, versatility, and cost-effectiveness. In this article, we will explore the definition of sand casting, the materials involved, the steps of the casting process, its advantages, and applications.
Definition of Sand Casting
At its core, sand casting is a method of producing metal parts by pouring molten metal into a mold that is composed of sand. The sand is typically mixed with a binder to give it the desired strength and cohesiveness. When the molten metal cools and solidifies, it takes the shape of the mold, yielding a cast part that can be further processed.
Materials Used in Sand Casting
The primary materials in sand casting are the mold itself, usually made of a mixture of sand and a bonding agent, and the metal that will be cast, which may include aluminum, bronze, iron, or steel. The sand used in the casting process is typically silica sand due to its high melting point and ability to withstand the heat of molten metal. Other additives, such as clay or oil, may be included to improve the properties of the sand.
The Sand Casting Process
The sand casting process can be broken down into several key stages
1. Pattern Making The first step involves creating a pattern that is a replica of the final product. Patterns can be made from wood, metal, or plastic, and may be single or multiple piece designs depending on the complexity of the part.
2. Mold Preparation After the pattern is made, it is used to create the mold. This can be done by packing sand around the pattern to form a mold cavity. The mold is often made in two halves, which allows for easy removal of the pattern.
3. Core Making For parts that require internal cavities, cores made of sand are created and placed inside the mold. Cores are made using a similar sand mixture and help define internal features of the final casting.
sand casting definition
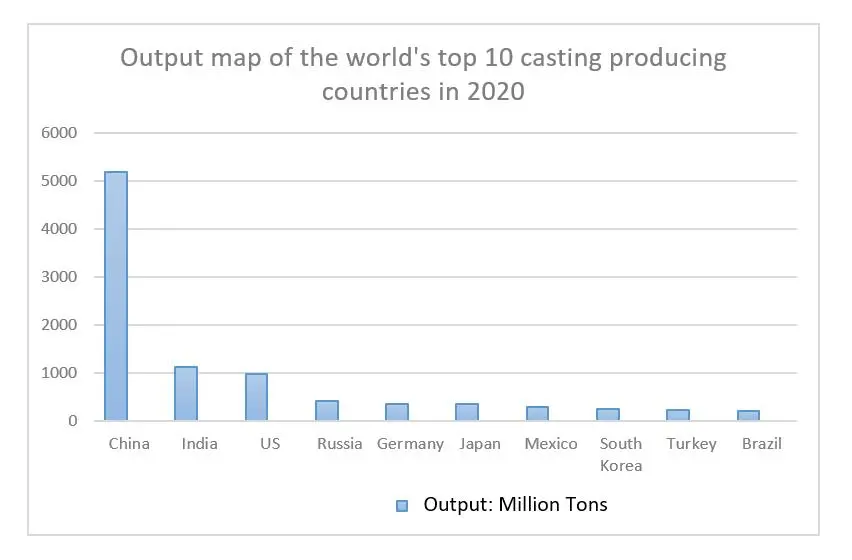
4. Melting and Pouring The metal is melted in a furnace until it reaches a suitable temperature, at which point it is poured into the prepared mold. The pouring operation must be performed quickly to ensure the metal does not cool before filling the mold.
5. Solidification and Cooling Once the molten metal is poured in, it begins to cool and solidify. This can take anywhere from a few minutes to several hours, depending on the size and type of metal.
6. Mold Removal After the metal has fully solidified, the mold is broken away to reveal the cast part. This step may require cleaning processes to remove any remaining sand.
.
7. Finishing Operations The final step often involves machining, sanding, or other methods to refine the surface quality of the casting, ensuring it meets the desired specifications.
Advantages of Sand Casting
Sand casting offers several advantages, including
- Cost-Effectiveness It requires relatively low capital investment and is suitable for low to medium volume production runs. - Versatility This process can be used for a wide range of metals and allows for the casting of large and complex shapes. - Flexibility Adjustments can be made quickly, allowing manufacturers to respond efficiently to changes in design or production needs.
Applications of Sand Casting
Sand casting is utilized in various industries, including automotive, aerospace, and construction. It is commonly used to produce parts such as engine blocks, pump housings, and decorative items.
In conclusion, sand casting is an essential metalworking technique that combines traditional craftsmanship with modern production techniques. Its ability to create complex shapes from a variety of metals makes it invaluable in numerous manufacturing sectors, thus ensuring its continued relevance in today's industrial landscape.
Post time:Aug . 13, 2024 10:20
Next:Comparison of Sand Casting and Investment Casting Techniques in Metal Manufacturing Processes