What Is Sand Casting?
Sand casting, also known as sand mold casting, is one of the most widely used metal casting processes in the manufacturing industry. This method involves creating a mold from sand and pouring molten metal into that mold to produce a desired component or product. The versatility and cost-effectiveness of sand casting make it a popular choice for a variety of applications, from small scale hobbyist projects to large industrial components.
The Process of Sand Casting
The sand casting process begins with the preparation of the mold. The first step is to create a pattern of the object that is to be cast. The pattern is usually made from materials such as wood, plastic, or metal, and is slightly larger than the final product to account for shrinkage as the metal cools. This pattern is then inserted into a mixture of sand and a binding agent, typically clay, to create a mold. The sand mixture is compacted around the pattern to form a cavity that replicates the details of the desired object.
Once the mold is prepared, the next step involves removing the pattern, which leaves behind a hollow cavity in the sand. The mold is then typically split into two halves, allowing for easier removal of the pattern and pouring of the metal. After the pattern is removed, the two halves of the mold are reassembled and held together, often using pins or clamps to ensure they stay aligned.
The molten metal, which can be made from a variety of materials including aluminum, iron, and bronze, is then poured into the mold through a sprue, a channel that allows the metal to flow into the cavity. The metal is left to cool and solidify, which can take anywhere from a few minutes to several hours, depending on the type of metal and the thickness of the casting.
Once the metal has cooled, the mold is broken apart to reveal the cast object. This process may involve shaking, blasting, or manual removal of the sand. After the casting is extracted, any imperfections are often addressed through finishing processes such as grinding, sandblasting, or machining to achieve the desired surface finish and dimensions.
what is a sand casting
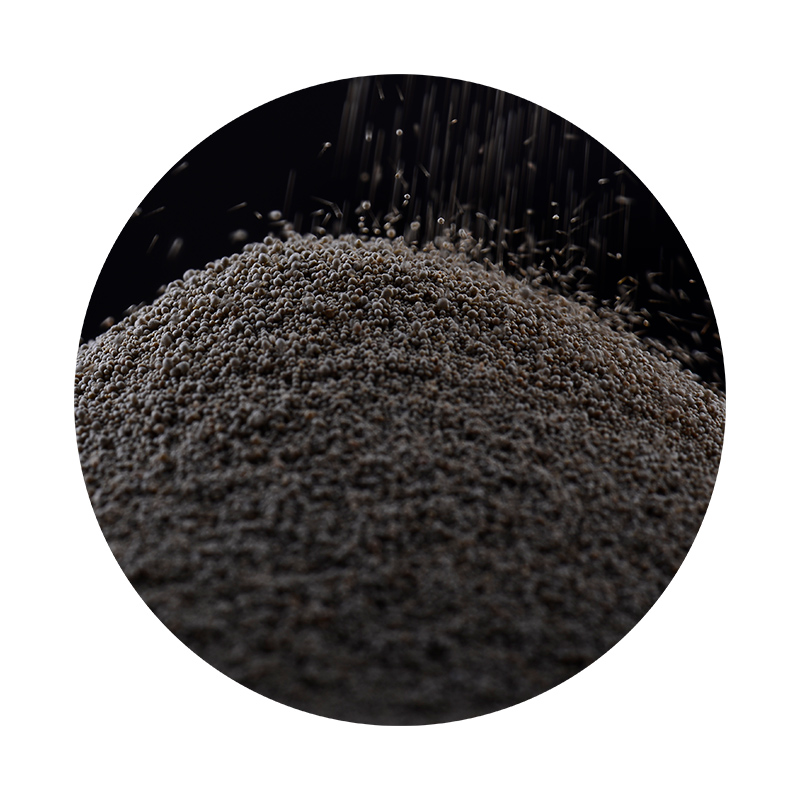
Advantages of Sand Casting
Sand casting offers several advantages that contribute to its widespread use. One of the most significant benefits is its cost-effectiveness. The materials required for sand casting, primarily sand and binder, are relatively inexpensive and readily available. Additionally, the process can be easily scaled for both large and small production runs, making it suitable for a wide range of industries.
Another major advantage is the ability to cast complex shapes and sizes. The flexibility of sand molds allows for intricate designs that may be difficult or impossible to achieve with other casting methods. Furthermore, sand casting is compatible with various metals and alloys, providing manufacturers with a broad spectrum of materials to choose from.
Applications of Sand Casting
Sand casting is utilized across multiple industries, including automotive, aerospace, marine, and art industries. Common applications include engine blocks, pump housings, and intricate sculptures. Its adaptability to different materials and designs has positioned sand casting as a vital technique in the production of custom and prototype parts.
Conclusion
In summary, sand casting is a foundational manufacturing process that plays an essential role in producing a wide array of metal components. With its cost-effectiveness, flexibility, and versatility, sand casting continues to be a preferred method for many applications, ensuring its place in the manufacturing landscape for years to come. Whether you are an industrial manufacturer or a hobbyist, understanding sand casting can open up new avenues for creativity and innovation in metalworking.
Post time:Aug . 14, 2024 04:11
Next:Specifications for High-Performance Resin Coated Sand in Industrial Applications and Manufacturing Processes