What Is Sand Casting?
Sand casting, also known as sand molded casting, is a versatile and widely used manufacturing process for producing metal parts and components. This method has been utilized for centuries and involves creating a mold using sand, which is then filled with molten metal to form a desired shape. The simplicity, cost-effectiveness, and adaptability of sand casting make it a favorite among manufacturers, particularly for low to medium production volumes.
The Sand Casting Process
The sand casting process begins with the preparation of the mold. The mold comprises two halves, referred to as the cope and the drag. Sand mixed with a binder, often clay or resin, is compacted into a mold box to create the impressions. In many cases, the mold is created around a pattern, which is typically a replica of the object to be cast. Patterns can be made from various materials, including wood, metal, or plastic, depending on the desired accuracy and durability.
Once the mold is formed, a pouring cup and sprues are added to allow the molten metal to enter the mold cavity. After the mold is complete, the next step is to melt the metal to be cast, which can range from aluminum and bronze to iron and steel. The molten metal is then poured into the opening of the mold and allowed to cool and solidify.
After the metal has cooled sufficiently, the mold is broken apart to retrieve the cast part. This may involve shaking, hammering, or using specialized tools to separate the halves of the mold. Finally, the finished casting will often require some post-processing, such as cleaning, machining, or surface treatment, to achieve the final specifications.
Advantages of Sand Casting
One of the significant benefits of sand casting is its ability to produce complex shapes. The flexibility of sand allows for intricate designs that may be challenging to achieve with other casting methods. Additionally, sand casting is suitable for a wide range of metal alloys, making it applicable in various industries, including automotive, aerospace, and construction.
what is a sand casting
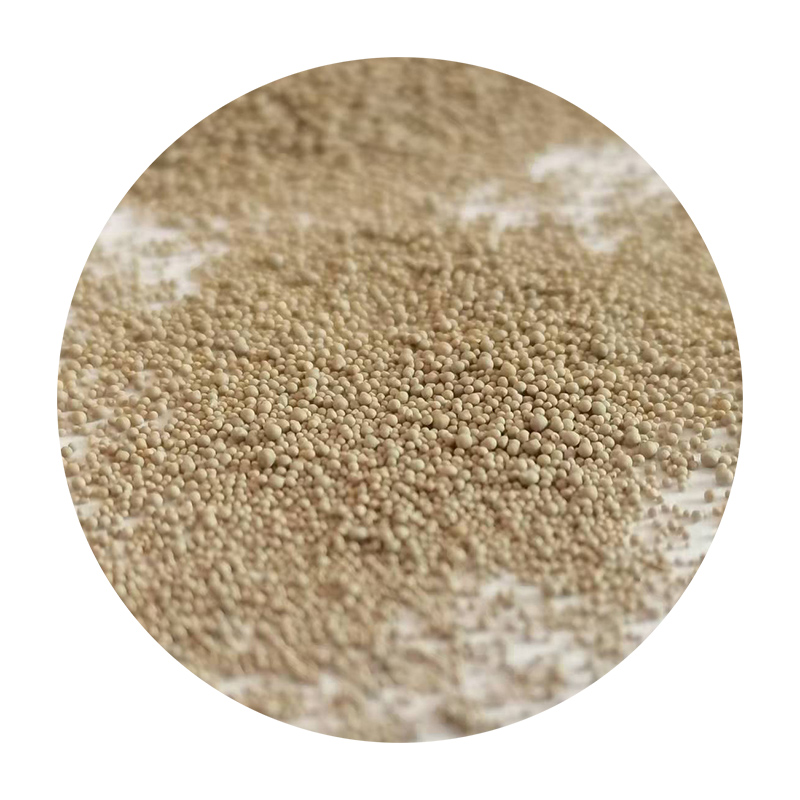
Cost efficiency is another advantage. The raw materials required for sand casting, such as sand, binder, and metal, are relatively inexpensive. Moreover, the process can be scaled to accommodate both small-scale and large-scale production. This adaptability allows businesses to meet specific production needs without incurring substantial costs.
Another noteworthy aspect of sand casting is its environmental friendliness. The sand used in casting can often be reclaimed and reused in multiple cycles, reducing waste and promoting sustainability within the manufacturing process.
Challenges in Sand Casting
Despite its numerous advantages, sand casting is not without challenges. One of the primary issues is achieving high dimensional accuracy. Because the sand can shift or settle, there may be slight variations in the final product. This limits the application of sand casting in industries that require tight tolerances.
Surface finish is another concern. The texture of the sand can result in rough surface finishes on the cast item, which may necessitate additional machining or polishing steps. While these challenges exist, advancements in technology and techniques continue to improve the quality of sand casting.
Conclusion
In conclusion, sand casting is a time-tested manufacturing process that plays a vital role in metal component production. Its ability to accommodate complex shapes and a diverse array of materials, coupled with cost-effectiveness, makes it an invaluable method in modern manufacturing. As technology continues to evolve, sand casting is likely to see improvements in precision and surface quality, further enhancing its standing in the industrial sector. Whether it’s for crafting intricate machinery parts or developing large-scale structures, sand casting remains a foundational technique in the world of manufacturing.
Post time:Aug . 21, 2024 04:58
Next:Exploring Innovations in Sand-Based 3D Printing Technology and Applications