What is Sand Casting?
Sand casting, also known as sand mold casting, is one of the oldest and most widely used metal casting processes. It involves creating a mold from special sand mixtures to produce metal parts and components. This versatile and cost-effective method is particularly favored in industries for producing complex shapes and large components.
History of Sand Casting
The origins of sand casting can be traced back to ancient civilizations. Archaeological evidence suggests that the Egyptians used sand casting techniques for creating intricate bronze tools and artifacts. Over the centuries, the process has evolved, incorporating modern technologies and materials, yet the fundamental principles remain largely unchanged.
How Sand Casting Works
The sand casting process begins with the creation of a pattern, which is a replica of the desired part. The pattern is typically made from a durable material, such as wood or metal, and is designed to be slightly larger than the final product to account for metal shrinkage during cooling.
Once the pattern is ready, a mold is prepared using a mixture of sand and a binder, which helps hold the sand together. The sand is packed around the pattern in a two-part mold, with one half being the cope (top half) and the other being the drag (bottom half). After removing the pattern, the mold cavity is created.
Next, molten metal is poured into the mold cavity through a system of channels known as gates and risers. The metal fills the mold, taking the shape of the cavity. Once the metal has cooled and solidified, the mold is broken apart to reveal the cast part.
Advantages of Sand Casting
what is a sand casting
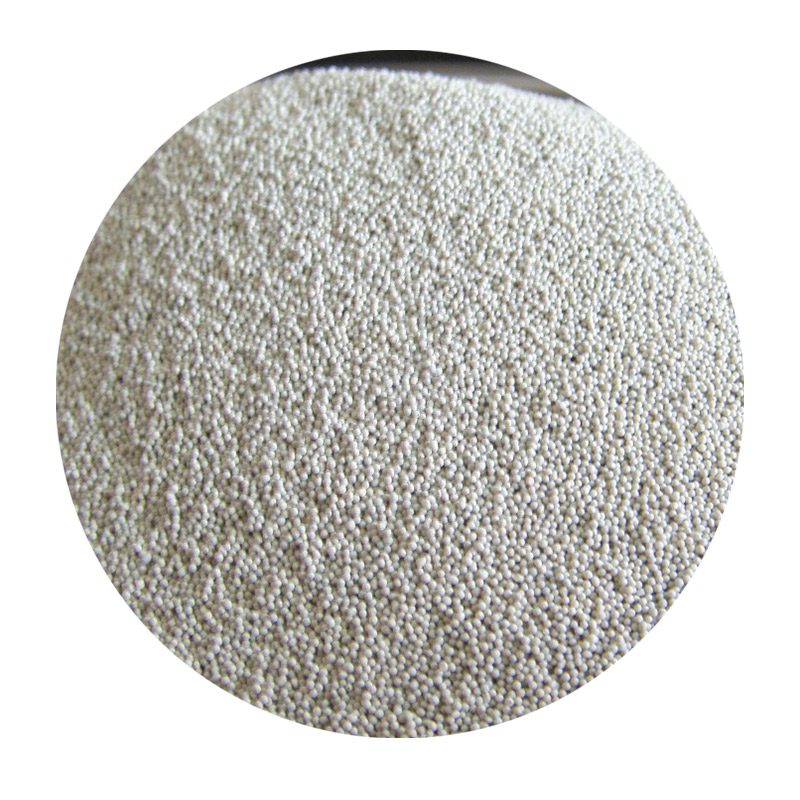
Sand casting offers several advantages
1. Versatility It can accommodate a wide range of metals, including aluminum, iron, steel, and bronze, making it suitable for diverse applications. 2. Complex Shapes The process allows for the production of intricate designs that would be difficult to achieve with other methods. 3. Cost-Effective Sand casting is often less expensive than other casting processes, particularly for low to medium volume production. 4. Large Parts This method can produce large components, and the molds can be scaled to various sizes. 5. Quick Turnaround Patterns can be made relatively quickly, allowing for rapid production cycles.
Applications of Sand Casting
Sand casting is widely used across various industries. It is prevalent in automotive, aerospace, and manufacturing sectors for producing parts like engine blocks, gearbox cases, and valve bodies. Additionally, sand casting is also utilized for art and sculpture, where artists create unique pieces through the casting process.
Challenges and Considerations
Despite its many advantages, sand casting does have some challenges. The surface finish of cast parts might not always be smooth, requiring secondary processing to achieve the desired quality. Moreover, the process also entails careful control of the cooling rate to prevent defects such as warping or cracking.
Conclusion
In conclusion, sand casting is a fundamental method in the field of manufacturing, known for its simplicity and effectiveness. Its rich history, versatility, and effectiveness in producing complex shapes make it an indispensable technique in both traditional and modern industries. As advancements in technology continue, sand casting is likely to enhance its capabilities, expanding its applications in the future.
Post time:Aug . 01, 2024 01:14
Next:Exploring the Benefits and Drawbacks of the Sand Casting Manufacturing Technique for Metal Parts