Sand Casting of Cast Iron An Overview
Sand casting is one of the oldest and most versatile manufacturing processes known to man. This method has been utilized for centuries to create complex metal parts, and it remains a popular choice in modern foundries, particularly for the casting of cast iron components. The basic principle behind sand casting involves creating a mold from a mixture of sand and a binding agent, into which molten metal is poured. This article will delve into the sand casting process specifically for cast iron, highlighting its advantages, applications, and the nuances involved in achieving high-quality castings.
The Sand Casting Process
The sand casting process begins with the creation of a mold. The primary material used for this purpose is silica sand, which is preferred for its excellent properties, including availability, cost-effectiveness, and ability to withstand high temperatures. The sand is mixed with a binder, typically clay or chemical agents, to help the grains stick together and maintain the mold's shape.
Once the mold is formed, it is divided into two halves the cope (top half) and the drag (bottom half). The pattern, usually made from metal or wood and designed to the specifications of the final product, is placed in the drag to create a cavity. The cope is then added, and the two halves are aligned. After ensuring the mold is securely held, cores may be added if the casting requires hollow sections.
Next comes the melting of cast iron, which is typically done in a furnace. Cast iron has a higher carbon content than steel, making it fluid when molten and easier to mold. Once the iron reaches the desired temperature, it is poured into the mold through a designated pouring cup and sprue, filling the cavity and taking the shape of the pattern.
After the molten metal cools and solidifies, the sand mold is broken away to reveal the cast iron component. The final product may require cleaning and finishing processes, including grinding, machining, or surface treatments, to meet specified tolerances and achieve the desired surface finish.
Advantages of Sand Casting for Cast Iron
sand casting cast iron
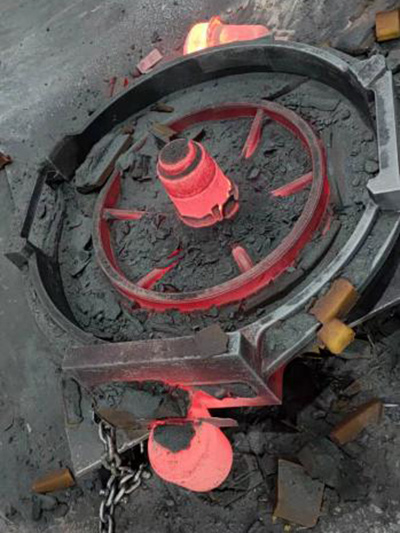
One significant advantage of sand casting is its ability to produce intricate shapes with relatively low costs. This process can accommodate a wide variety of sizes, from small components to large industrial machine parts. Furthermore, because sand molds can be reused multiple times, the production costs can be lowered over time.
Another benefit is the thermal stability of cast iron, which allows for excellent dimensional accuracy and surface finish in finished parts. Cast iron's properties, such as wear resistance and excellent machinability, make it a favored material in engineering applications.
Applications of Sand Cast Iron
Sand casting is widely used in various industries, particularly in automotive, aerospace, and machinery manufacturing. Components such as engine blocks, cylinder heads, and various machine parts are routinely produced through sand casting. Additionally, creative industries often leverage sand casting for art pieces and sculptures, showcasing the diverse applications of cast iron.
Challenges and Considerations
Even though sand casting has numerous advantages, there are challenges associated with the process. Proper mold design and preparation are critical to prevent issues such as sand adhesion and uneven cooling, which can lead to defects in the final product. Foundries must also carefully manage the melting and pouring process to minimize oxidation and contamination of the molten metal.
In conclusion, sand casting of cast iron remains a cornerstone of manufacturing due to its efficiency, adaptability, and cost-effectiveness. As technology advances, innovations in sand casting techniques and materials continue to enhance the quality and capabilities of cast iron products, ensuring its relevance in modern industry.
Post time:Aug . 06, 2024 14:02
Next:Exploring the Role of Sand in Foundry Processes and Its Impact on Casting Quality