Lost Foam Casting An Innovative Approach to Metal Casting
Lost foam casting is a specialized metal casting process that has gained traction in recent years due to its unique advantages and efficiencies. This method, which utilizes a foam pattern, offers significant enhancements over traditional casting techniques, making it a preferred choice for various manufacturing applications.
The process begins by creating a pattern out of a polystyrene foam, which is an inexpensive and easy material to mold and shape. This foam pattern is an exact replica of the final metal part, allowing for intricate designs and complex geometries that can be challenging to achieve with traditional methods. Once the foam pattern is created, it is coated with a thin layer of a refractory material, which serves as the mold. This coating must be carefully applied to ensure that it can withstand the high temperatures of molten metal without breaking.
After the coating has dried, the foam pattern is placed into a flask and heated, causing it to vaporize when molten metal is poured into the mold. The vaporization process eliminates the need for a core or additional molds, which simplifies the casting process. The molten metal takes the place of the foam, filling the void left behind and ultimately forming a solid metal part that mirrors the original foam pattern. This process allows for a seamless and clean casting, reducing the likelihood of defects such as air pockets or misalignments.
One of the key advantages of lost foam casting is its capability for producing intricate parts with excellent surface finishes. This method significantly reduces the machining time required post-casting, as the dimensional accuracy is often higher than that achieved by conventional sand casting processes. The absence of draft angles, a necessity in many traditional casting techniques, further allows for more complex designs without sacrificing quality.
lost foam casting
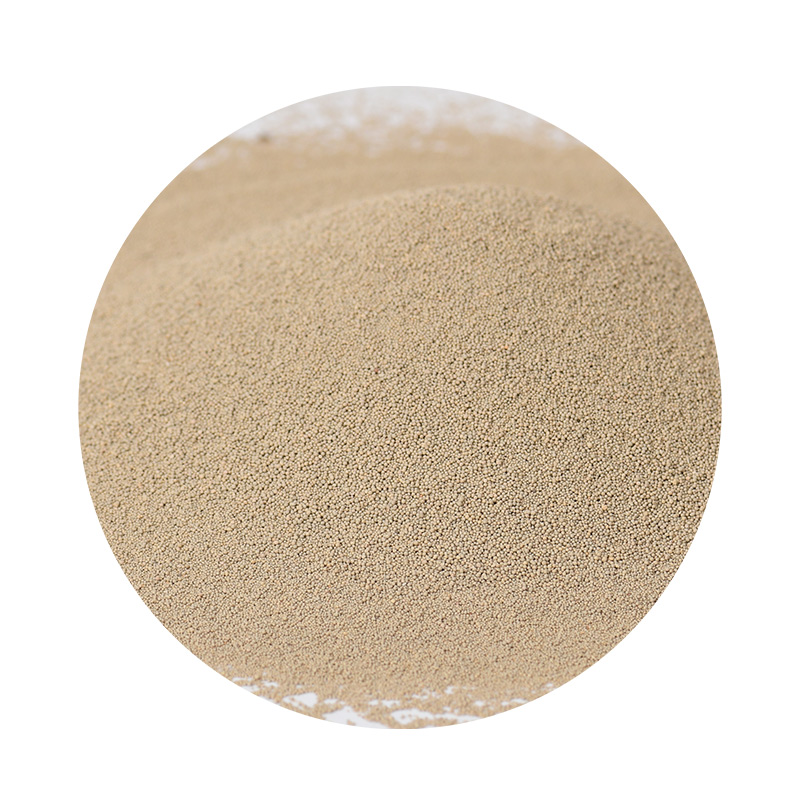
Additionally, lost foam casting presents substantial economic benefits. The process reduces waste, as the foam can be completely replaced by metal without creating excess scrap. This not only conserves raw materials but also lowers costs associated with waste disposal. Furthermore, the efficiency of lost foam casting can lead to shorter lead times, allowing companies to respond to market demands more swiftly.
Moreover, the flexibility of lost foam casting makes it an attractive option for a variety of industries, ranging from automotive to aerospace and consumer products. Its versatility allows for the casting of both ferrous and non-ferrous metals, broadening its applicability in various sectors. As manufacturers continue to seek ways to innovate and streamline production, lost foam casting stands out as a forward-thinking solution.
As with any manufacturing process, there are challenges associated with lost foam casting. These can include the initial costs of creating foam patterns and the need for precise temperature control during the pouring process to maintain metal quality. However, ongoing advancements in technology and materials science are likely to address these challenges, making lost foam casting an even more viable option for a broader range of applications.
In summary, lost foam casting is a cutting-edge method that brings together precision, efficiency, and versatility. Its capacity to produce complex designs with minimal waste makes it a favored choice in modern manufacturing. As industries continue to evolve and adapt to the demands of the global market, lost foam casting will undoubtedly continue to play a crucial role in shaping the future of metal casting.
Post time:Aug . 22, 2024 00:52
Next:The Significance of Sand Casting in Modern Manufacturing Processes