What is Sand Casting in Engineering?
Sand casting, also known as sand mold casting, is one of the oldest and most widely used metal casting processes in the field of engineering. It involves the use of sand as the primary mold material to create intricate metal components. This technique is favored for its versatility, cost-effectiveness, and ability to produce complex shapes in various metal alloys.
At the core of sand casting is the process of creating a mold from a mixture of sand and a binder material, typically clay. The sand grains are compacted around a pattern, which is a replica of the part to be cast. This pattern can be made from various materials, including wood, metal, or plastic. Once the mold is formed and the pattern is removed, it leaves a cavity that accurately represents the desired component.
One of the major advantages of sand casting is its flexibility. The process allows for the creation of large parts that can weigh hundreds of pounds, as well as intricate designs with fine details. This is particularly useful in industries where custom and complex geometries are needed, such as automotive, aerospace, and art.
The sand used in the casting process is typically silica sand, which is both abundant and inexpensive. The addition of a binder helps hold the sand grains together, allowing the mold to maintain its shape under the weight of the molten metal. After the mold is prepared, molten metal is poured into the cavity. Once it cools and solidifies, the mold is broken apart to reveal the cast part.
Advantages of Sand Casting
Sand casting offers numerous benefits, making it a preferred choice among engineers. One of the key advantages is its cost-effectiveness. The materials required for sand molds are relatively cheap, and the manufacturing process can be carried out without the need for expensive equipment. For low to medium production runs, sand casting can be more economical compared to other casting methods.
what is sand casting in engineering
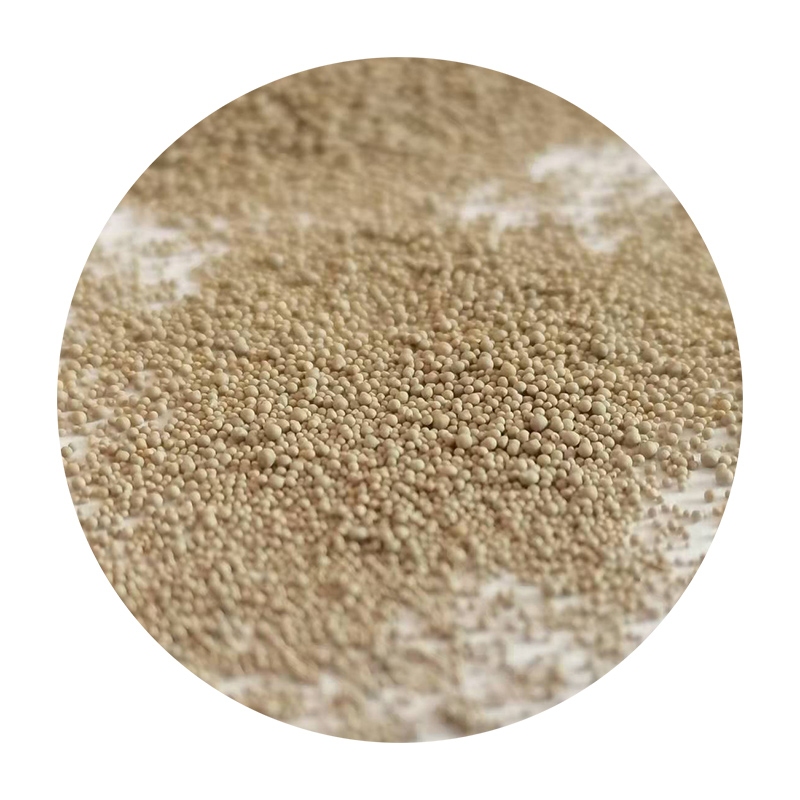
Another significant advantage is the ability to cast a wide range of materials, including ferrous and non-ferrous alloys. This versatility allows manufacturers to produce parts tailored to specific applications and performance requirements. Furthermore, the sand casting process can accommodate various casting sizes, from small precision components to large industrial parts.
Disadvantages of Sand Casting
Despite its many advantages, sand casting is not without its limitations. One of the main drawbacks is the surface finish of the cast parts. Compared to other casting methods, such as investment casting or die casting, sand casting typically results in rougher surfaces, which may require additional machining for certain applications. Furthermore, the process is not suitable for high-volume production due to the time-consuming nature of mold preparation and the longer cycle times.
Additionally, the dimensional accuracy of sand-cast parts can be less precise than that achieved by other methods, which may pose challenges in certain engineering applications where tight tolerances are required.
Conclusion
In conclusion, sand casting is a fundamental technique in the field of engineering, providing a versatile and cost-effective solution for producing metal components. Its ability to create complex shapes and accommodate various alloys makes it an invaluable method across multiple industries. While it does have limitations in terms of surface finish and accuracy, continued advancements in technologies and materials are helping to mitigate these challenges, ensuring that sand casting remains a relevant and widely used process in modern manufacturing. This enduring method reflects the ingenuity and adaptability of engineering practices throughout history.
Post time:Aug . 12, 2024 05:38
Next:Techniques for Smoothing 3D Prints Through Sanding and Other Finishing Methods to Enhance Quality