The Metal Sand Casting Process An Overview
Metal sand casting is a versatile and widely used manufacturing process that plays a critical role in producing intricate components across various industries, including automotive, aerospace, machinery, and more. This technique involves creating a mold from sand, which is then used to form metal parts through a series of systematic steps. This article provides an overview of the metal sand casting process, highlighting its advantages and applications.
The Basic Steps of Metal Sand Casting
1. Designing the Pattern The process begins with creating a pattern, which is a replica of the final component. Patterns can be made from metal, wood, or plastic, and they are typically slightly larger than the final product to account for metal shrinkage during cooling.
2. Preparing the Mold Once the pattern is ready, the next step is to prepare the mold. This involves compacting sand around the pattern to create a mold cavity. The sand mixture is usually composed of silica sand, clay, and water, which gives it the ability to hold shape and withstand the molten metal's heat.
3. Creating the Cores For complex shapes, cores may be necessary to create internal features within the casting. Cores are also made from sand and added to the mold to form cavities.
4. Assembling the Mold After preparing the mold and cores, the next step is to assemble them. The two halves of the mold are joined together, and any necessary gating systems, which allow the molten metal to flow into the mold, are integrated.
5. Pouring the Metal The mold is then heated, and molten metal is poured into it. The metal could be aluminum, iron, or any other alloy, depending on the requirements of the final product. The temperature and composition of the molten metal are carefully controlled to ensure the casting's quality.
6. Cooling Once the mold is filled, the metal is allowed to cool and solidify. Cooling times vary based on the thickness of the casting and the type of metal used.
metal sand casting process
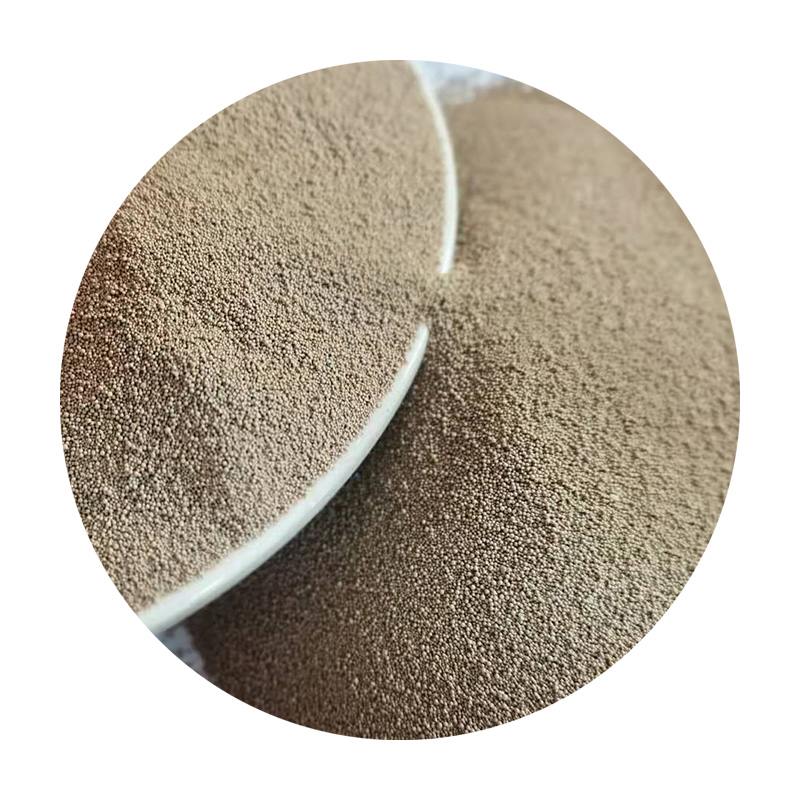
7. Breaking the Mold After adequate cooling, the mold is broken apart to reveal the cast component. Any sand leftover from the casting process is removed, typically using vibration or mechanical shaking methods.
8. Finishing Touches Finally, the cast part is cleaned and may undergo further processing, such as machining, polishing, or surface treatment, to achieve the desired surface finish and dimensional accuracy.
Advantages of Metal Sand Casting
Metal sand casting offers several advantages, making it a popular choice for manufacturers. One of the primary benefits is its ability to produce complex shapes and large components with high precision. The flexibility of the sand mold also allows for easy modifications and adaptations during the design phase.
Another significant advantage is its cost-effectiveness, especially for low to medium production volumes. The sand used for casting is relatively inexpensive, and the patterns can often be reused for multiple cycles. Additionally, sand casting has a high tolerance for different metals and alloys, giving manufacturers the ability to choose materials that best meet their product specifications.
Applications of Metal Sand Casting
Metal sand casting is utilized in numerous applications, including the production of engine blocks, transmission cases, pump housings, and a variety of structural components. Its versatility makes it essential in industries such as automotive, aerospace, construction, and plumbing, where reliable and durable metal parts are critical.
In conclusion, the metal sand casting process is a robust manufacturing method characterized by its flexibility, cost-effectiveness, and capability to produce intricate parts. As technology advances, ongoing innovations in materials and techniques continue to enhance the efficiency and quality of sand casting, ensuring its place in modern manufacturing.
Post time:Aug . 13, 2024 21:41
Next:Exploring the Innovations and Services of the Golden Sands Company in the Coastal Industry