Understanding Sand Casting and Its Importance
Sand casting, also known as sand mold casting, is one of the oldest and most versatile metal casting processes used today. This technique involves creating a mold out of fine sand and then pouring molten metal into that mold to create various components. The simplicity of the process, combined with the use of readily available materials, has made sand casting a popular choice in numerous industries, including automotive, aerospace, and machinery manufacturing.
The Process of Sand Casting
The sand casting process begins with the creation of a pattern, which is a replica of the object to be cast. This pattern can be made from various materials, including wood, metal, or plastic. The pattern is then placed in a molding box, and sand is packed around it to form a mold. Traditionally, the sand used in this process is a mixture of silica sand, clay, and water, which gives it the necessary properties to retain shape and withstand high temperatures.
Once the sand is compacted around the pattern, it is carefully removed to leave a cavity in the shape of the object to be cast. The mold is typically divided into two halves (the cope and the drag) to facilitate easy removal of patterns and to allow for adequate pouring of molten metal. After the pattern is removed, the two halves of the mold are reassembled, and the molten metal is poured through a pouring basin and into the mold cavity.
After the metal cools and solidifies, the sand mold is broken away to reveal the completed cast part. This part may require further finishing processes, such as grinding, cleaning, or machining, to meet specific tolerances and surface standards.
Benefits of Sand Casting
sand casting sand
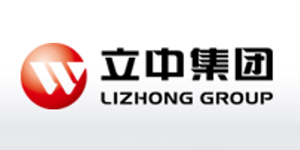
One of the primary advantages of sand casting is its flexibility. It can accommodate a wide range of metal alloys, including aluminum, brass, iron, and steel, making it suitable for various applications. Additionally, the process can produce large castings, which would be challenging to fabricate using other methods.
Sand casting is also cost-effective, especially when producing small to medium-sized batches. Since the molds can be reused and the materials used are relatively inexpensive, manufacturers can achieve a reasonable cost per unit. Moreover, the nature of sand allows for easy modifications to the mold structure, enabling rapid prototyping and adjustments to designs without significant overhead.
Another significant benefit of sand casting is its ability to produce complex shapes and intricate designs. The granular nature of the sand allows it to conform to the details of the pattern, making it easy to replicate intricate designs that may be difficult to achieve with other casting methods.
Challenges and Considerations
Despite its advantages, sand casting does come with some challenges. One such challenge is the potential for defects, such as sand inclusion, air pockets, or surface imperfections. These issues can arise from improper mold preparation or inadequate handling of energy during the casting process. Therefore, achieving high-quality castings requires expertise in mold-making, pouring techniques, and post-processing.
In conclusion, sand casting is a vital manufacturing process that continues to play a significant role in various industries. Its versatility, cost-effectiveness, and ability to produce complex shapes make it an invaluable technique for manufacturers worldwide. As technology advances, so too does the potential for sand casting, with innovations in materials and methods paving the way for improved efficiency and quality in metal casting. Whether for small-scale applications or large industrial components, sand casting remains a cornerstone of metal fabrication.
Post time:Aug . 01, 2024 05:33
Next:The Advantages and Applications of Lost Foam Casting in Modern Manufacturing Techniques