Sand Casting A Versatile Metal Casting Process
Sand casting, also known as sand molded casting, is one of the oldest and most widely used metal casting processes in the manufacturing industry. Its simplicity and versatility make it an ideal choice for producing a wide variety of metal parts, from small components to large industrial products. This article will delve into the sand casting process, its advantages, applications, and factors to consider for successful outcomes.
The Sand Casting Process
The sand casting process begins with the creation of a mold from a mixture of sand, clay, and water. The mold consists of two halves the cope (top half) and the drag (bottom half). The pattern, which is a replica of the final product, is typically made of metal, plastic, or wood and is used to form the cavity in the sand. The pattern is placed in the sand mixture, which is then compacted around it to create the mold.
Once the mold is prepared, the pattern is removed, and the two halves of the mold are secured together. Molten metal is then poured into the cavity created by the pattern. After the metal has solidified, the mold is broken apart to retrieve the casting. The final step involves cleaning and finishing the casting, which may require additional machining or surface treatment to meet specific requirements.
Advantages of Sand Casting
Sand casting offers several advantages that make it a preferred method for many manufacturers
1. Cost-Effectiveness The materials used in sand casting, primarily sand and clay, are inexpensive and readily available. Additionally, the process does not require expensive equipment, making it accessible for both small and large-scale production.
2. Versatility Sand casting can accommodate a wide range of metals, including aluminum, iron, steel, and bronze. This versatility allows manufacturers to produce diverse products tailored to various industries, such as automotive, aerospace, and construction.
3. Complex Geometries The sand casting process is ideal for creating complex shapes and intricate designs that may be challenging to achieve with other manufacturing methods. The adaptability of the sand mold allows for fine details and large variations in size.
sand casting
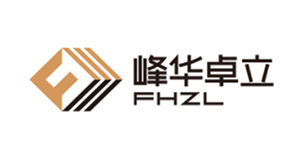
4. Low Initial Setup Costs Unlike other casting processes that may require expensive tooling and machinery, sand casting can be initiated with minimal upfront investment. This low barrier to entry makes it attractive for startups and custom job shops.
Applications of Sand Casting
Sand casting is used in numerous industries due to its flexibility and efficiency. Common applications include
- Automotive Parts Components such as engine blocks, transmission cases, and various housings are often produced using sand casting. - Marine Products Sand casting is commonly utilized to create parts for boats and ships, such as fittings and propellers. - Industrial Equipment Many pieces of heavy machinery and equipment, including pumps, valves, and gears, are manufactured using the sand casting process. - Arts and Crafts Sand casting is also employed in creating sculptures and decorative items, showcasing the artistic potential of this versatile process.
Factors for Successful Sand Casting
To achieve high-quality castings, several factors should be considered during the sand casting process
- Mold Quality The quality of the sand mold significantly impacts the final product. Proper mixing, compaction, and moisture content are crucial for mold integrity. - Pattern Design The design of the pattern should account for factors like shrinkage and expansion of the metal during cooling. Precision in pattern making ensures the accuracy of the final casting. - Metal Pouring The temperature and technique used to pour the molten metal are critical to prevent defects such as cold shuts and misruns.
Conclusion
Sand casting remains a key method for metal fabrication, combining cost-effectiveness with the ability to produce complex and varied components. Its versatility across different industries, coupled with a relatively straightforward process, ensures that it will continue to play a vital role in manufacturing for years to come. By understanding its advantages and challenges, manufacturers can make informed decisions to optimize their casting processes and achieve superior results.
Post time:Jul . 29, 2024 04:02
Next:Optimizing Sand Casting Process in Manufacturing Facilities for Enhanced Efficiency and Quality Control