Understanding the Sand Casting Process
Sand casting, one of the oldest and most versatile metal casting processes, is widely used in the manufacturing industry to produce intricate metal parts. This method involves creating a sand mold into which molten metal is poured, allowing the metal to take the shape of the mold once it cools and solidifies. With its relatively low cost and capability to produce complex geometries, sand casting is a favored choice for both small and large-scale production.
Process Overview
The sand casting process begins with the creation of a pattern, which is a replica of the desired part. The pattern is typically made of metal, plastic, or wood and is slightly larger than the finished product to accommodate the metal's shrinkage as it cools. Once the pattern is prepared, it is placed into a mold box, which holds the sand.
The mold is made from a mixture of sand, clay, and water. The clay binds the sand particles together, allowing the mold to maintain its shape during the pouring of the molten metal. This mixture is packed around the pattern in the mold box, ensuring that every detail of the pattern is captured in the sand. After the mold is formed, the pattern is removed, leaving a cavity in the shape of the part.
Pouring and Cooling
With the mold cavity prepared, the next step is to pour the molten metal into the mold. The metal, which can be made from various alloys such as aluminum, iron, or bronze, is heated to a temperature where it becomes liquid. The molten metal is then carefully poured into the mold through a designated opening known as the sprue.
what is sand casting process
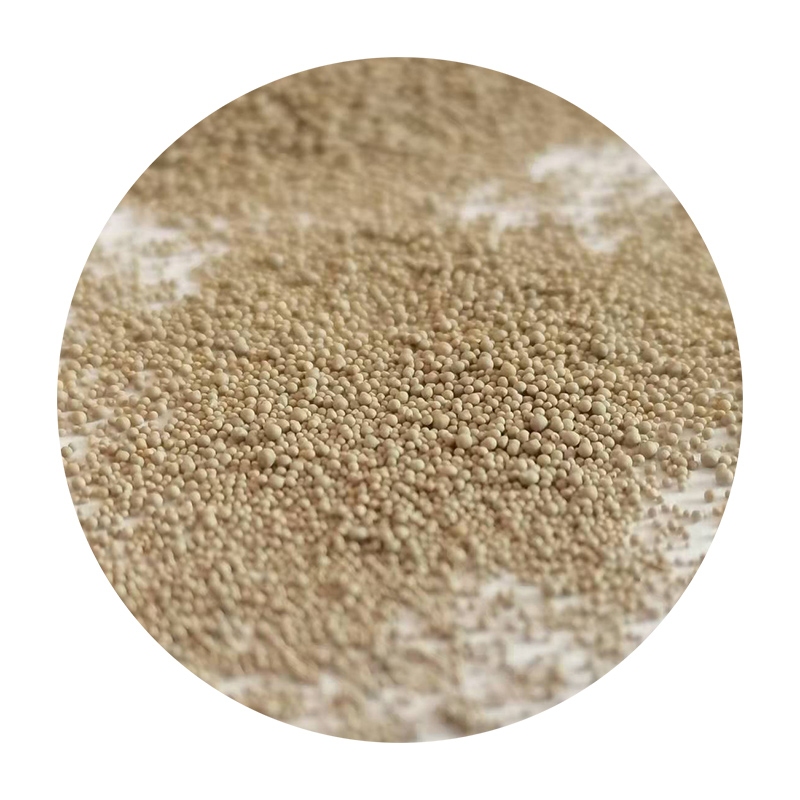
As the metal fills the mold cavity, it cools and solidifies, taking on the shape of the pattern. This cooling process can take anywhere from a few minutes to several hours, depending on the size and thickness of the casting. Once the metal has fully cooled, the mold is broken apart, and the sand is removed, revealing the cast part.
Advantages and Applications
Sand casting offers several advantages that make it a popular choice among manufacturers. One of the most significant benefits is its low cost. The materials used for making molds are inexpensive, and the process itself can be adapted for both short runs and mass production. Additionally, the process can accommodate a wide variety of shapes and sizes, making it suitable for producing complex parts that would be difficult or impossible to create using other methods.
Applications of sand casting are vast and diverse, ranging from automotive components and marine parts to aerospace applications and industrial machinery. Industries benefit from sand casting due to its ability to produce large parts efficiently, while still allowing for high precision and a good surface finish.
Challenges and Considerations
Despite its numerous advantages, sand casting is not without its challenges. Quality control is crucial, as defects such as sand inclusions, shrinkage cavities, and surface imperfections can occur if proper procedures are not followed. Additionally, the process can be time-consuming, particularly for larger castings or when multiple patterns are involved.
In conclusion, sand casting remains a fundamental method in the manufacturing landscape. Its advantages in cost-effectiveness and versatility make it a popular choice for producing a wide range of metal parts. As technology advances, improving the efficiency and precision of the sand casting process will further enhance its relevance in modern manufacturing, ensuring that it continues to meet the demands of various industries.
Post time:Jul . 29, 2024 05:06
Next:Understanding the Essential Components Involved in the Sand Casting Process for Metal Fabrication