Sand Casting Process An Overview
Sand casting is one of the oldest and most widely used metal casting processes in the manufacturing industry. This versatile technique is esteemed for its ability to produce complex shapes with high precision and excellent surface finish. The process involves several key steps and materials, making it an essential method for producing metal components in various sectors, including automotive, aerospace, and machinery.
Materials Used in Sand Casting
The primary material used in sand casting is the molding sand, which is typically a mixture of silica sand, clay, water, and other additives. The most common types of sand include green sand, which contains moisture and is used for molding, and resin-bonded sand, which uses a resin to bind the sand grains together. The choice of sand depends on the specific requirements of the casting process, including the type of metal being cast and the desired properties of the final product.
Steps in the Sand Casting Process
1. Pattern Making The first step in the sand casting process is creating a pattern of the desired part. The pattern is usually made from materials such as wood, metal, or plastic and is an exact replica of the final product. Patterns can be either solid or split, depending on the complexity of the design.
2. Mold Preparation The next step is preparing the mold. The molding sand is packed around the pattern to create a mold cavity. This process involves compacting the sand firmly to ensure it holds the shape. Once the sand is packed, the pattern is removed, leaving a cavity that will form the shape of the final casting.
3. Core Making In cases where hollow sections are required, cores made of sand are created. These cores are placed within the mold cavity to form internal features and provide additional shapes that cannot be achieved with the mold alone.
sand casting process
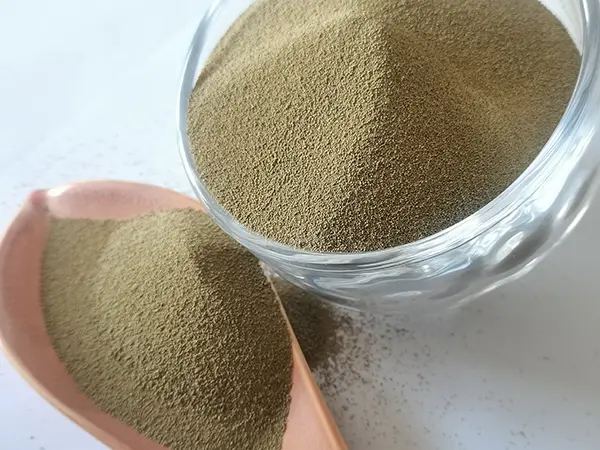
4. Melting and Pouring After the mold and core (if needed) are prepared, the chosen metal is melted in a furnace at a controlled temperature and then poured into the mold cavity. The type of metal depends on the application and can range from aluminum and iron to bronze and zinc.
5. Cooling and Solidification Once the molten metal is poured into the mold, it begins to cool and solidify. The cooling rate can significantly affect the properties of the final casting, so it’s controlled based on the metal being used and the design specifications.
6. Mold Removal and Finishing After the metal has fully solidified, the mold is broken away, revealing the cast part. This part may require additional finishing processes, such as machining, grinding, or surface treatment, to achieve the desired dimensions and surface quality.
Advantages and Applications
Sand casting offers several advantages, including its ability to produce large and heavy parts, low tooling costs, and adaptability for producing a wide range of shapes and sizes. Additionally, the process is suited for both small batch productions and large-scale manufacturing.
Due to its flexibility and efficiency, sand casting is employed in various applications, including engine blocks, frames, and complex industrial components. Industries like automotive, machinery, and aerospace benefit significantly from this manufacturing process due to its cost-effectiveness and the ability to produce intricate designs.
Conclusion
In conclusion, sand casting remains a cornerstone of manufacturing, demonstrating its relevance and utility even in the modern industrial landscape. The combination of traditional techniques with advancements in materials and technology ensures that sand casting will continue to play a vital role in producing high-quality metal components across multiple industries for years to come. Its simplicity, efficiency, and versatility make it an enduring choice for engineers and manufacturers alike.
Post time:Jul . 20, 2024 11:50
Next:Enhancing Precision and Quality in Sand Casting Techniques for Improved Manufacturing Outcomes