Dry Sand Casting Process An Overview
Dry sand casting is a widely utilized metal casting process that leverages sand as the primary material for creating molds. This method stands out for its ability to produce high-quality castings with excellent surface finishes and dimensional accuracy. It is widely used in various industries, including automotive, aerospace, and manufacturing, due to its efficiency and effectiveness.
The Basics of Dry Sand Casting
In dry sand casting, the sand used for making the molds is mixed with a binding agent, typically a thermosetting resin. Unlike green sand casting, which uses moist sand, dry sand ensures that there is no moisture in the mold, allowing it to maintain its strength and integrity during the casting process. The dry sand is usually baked or cured in an oven to achieve a solidified state before pouring in the molten metal.
Materials Used
The primary material for the mold is silica sand, which provides high thermal resistance and excellent flowability. The binding agents, such as phenolic resin or other polymers, not only enhance the bonding of sand grains but also contribute to the strength and durability of the mold. The consistent and controlled preparation of the sand mixture is essential in achieving desirable casting outcomes.
Steps in the Dry Sand Casting Process
1. Pattern Making The first step involves creating a pattern, typically made of metal or plastic, which replicates the dimensions of the final product. The pattern is designed to include allowances for shrinkage and machining.
2. Mold Preparation The dry sand is mixed with the binding agent and typically cured in a heated environment to form a rigid mold. The strength of dry sand molds allows them to withstand high pouring temperatures of molten metal.
dry sand casting process
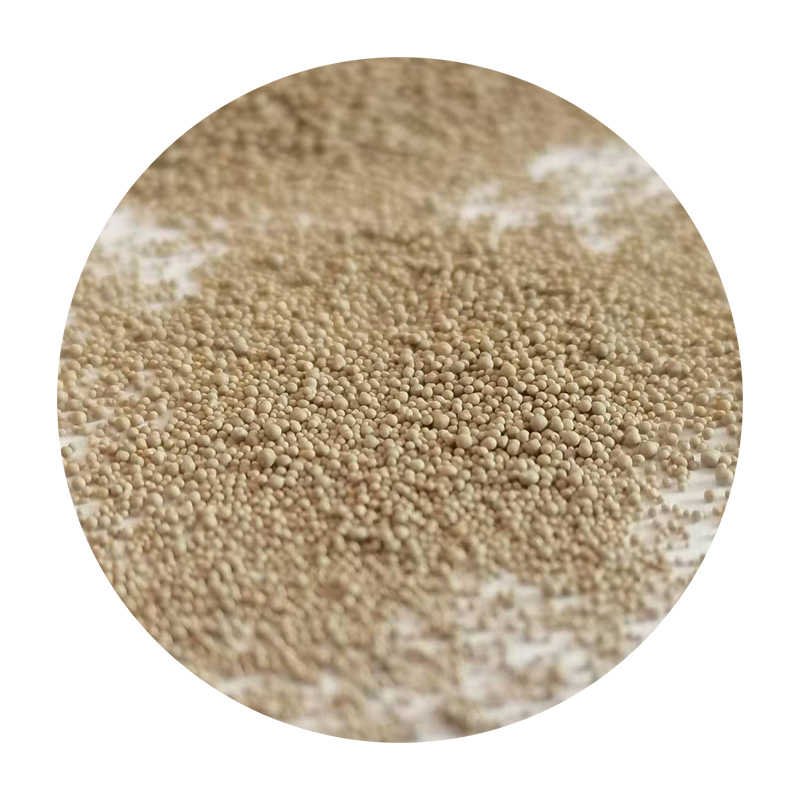
3. Core Making If the design requires hollow sections, cores are made separately using the same dry sand process. Cores are essential for creating internal geometries and are placed within the mold before pouring the metal.
4. Pouring Once the mold is prepared and any necessary cores are in place, molten metal is poured into the mold cavity. The absence of moisture in dry sand reduces the risk of defects such as gas porosity, leading to a higher-quality casting.
5. Cooling and Solidification After pouring, the molten metal should be allowed to cool and solidify. The solidification process can be monitored to prevent defects and ensure that the metal takes the intended shape.
6. Mold Removal Once the metal has cooled sufficiently, the mold is broken apart to reveal the casting. This step may require manual or mechanical assistance, depending on the size and complexity of the casting.
7. Finishing The final step of the dry sand casting process involves removing any excess material, cleaning the casting, and conducting any final machining or surface treatments to achieve the desired finish.
Advantages of Dry Sand Casting
One of the primary advantages of dry sand casting is its ability to produce detailed and accurate castings. The dry sand's rigidity allows for sharper contours and finer details, making it suitable for complex designs. Furthermore, the process minimizes defects related to moisture, such as gas entrapment and shrinkage cavities. The durability of dry sand molds also allows for multiple uses, reducing material waste and overall production costs.
Conclusion
The dry sand casting process represents a significant advancement in the field of metal casting. By utilizing a mold made from dry sand mixed with a binding agent, manufacturers can produce high-quality, intricate castings with superior surface finishes. As industries continue to innovate and demand more precise and efficient production methods, dry sand casting will undoubtedly remain a valuable option for engineers and manufacturers alike. It exemplifies how traditional techniques can be adapted and improved to meet modern challenges in production and design.
Post time:Jul . 23, 2024 14:39
Next:Finding Reliable Suppliers for High-Quality Sand Casting Services in Your Industry Needs