Materials Used for Sand Casting
Sand casting is one of the oldest and most widely used manufacturing processes for producing metal parts. This versatile method allows for intricate designs and the ability to create various shapes and sizes, making it a popular choice across multiple industries, including automotive, aerospace, and consumer goods. The success of sand casting largely relies on the materials used, which determine the quality and properties of the final product.
1. Sand
The primary material in sand casting is, as the name suggests, sand. The most commonly used type of sand is silica sand, primarily due to its high melting point, availability, and excellent flowability, which allows for the creation of detailed molds. To enhance the performance of the sand, it is often mixed with bonding agents such as clay. The clay aids in holding the sand particles together, improving the mold's strength and durability. Common clay used includes bentonite, which has excellent binding properties and helps the mold withstand the pressure of molten metal.
2. Bonding Agents
Aside from sand, bonding agents play a critical role in sand casting. These agents help to strengthen the sand mixture, allowing for better shape retention during the pouring of molten metal. Clay is the most traditional bonding agent, but other materials can be used as well, such as resin-coated sands, which provide enhanced strength and lower gas permeability. This results in cleaner surfaces on the final casting, reducing the need for post-processing. Additionally, chemical binders that cure at room temperature can also be utilized to create more complex molds and cores that traditional methods may not support.
3. Metal Alloys
The choice of metal alloy significantly influences the casting process, as well as the properties of the final product. Common metals used in sand casting include aluminum, iron, and bronze. Aluminum is particularly favored due to its lightweight nature and resistance to corrosion. Cast iron, known for its excellent castability and strength, is predominant in machinery and automotive applications. Bronze, while more expensive, provides superior wear resistance and is often used in components that require durability and low friction.
materials used for sand casting
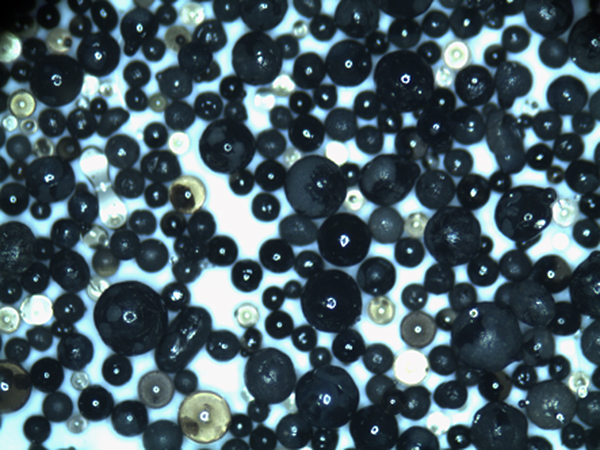
4. Additives
To improve the casting process and the resulting properties of the castings, additives can be included in the metal alloy. These may include elements like silicon, which improves fluidity and reduces shrinkage during cooling, or magnesium, which enhances strength and ductility. These additives allow manufacturers to tailor the properties of the cast metal more precisely, adapting to specific requirements of the final application.
5. Release Agents
To ensure a smooth demolding process, release agents are often applied to the mold surfaces. These agents reduce friction between the metal casting and the mold, making it easier to remove the completed part without damaging it. Common release agents include oils, waxes, and silicone-based compounds, and their use can greatly affect the surface finish of the final product.
6. Core Materials
In sand casting, cores are often used to create hollow sections within the cast parts. Cores are typically made from sand mixed with a binder, similar to the mold. This allows for complex internal geometries that cannot be achieved with the outer mold alone. The core material must be carefully selected to balance strength and thermal stability, as it will be exposed to high temperatures during casting.
Conclusion
In summary, the materials used in sand casting are pivotal to the success of the process. From the type of sand and bonding agents to the choice of metal alloys and additives, each material contributes to the quality and functionality of the final product. As technology advances, the development of new materials and methods continues to enhance the capabilities of sand casting, ensuring its place as a vital manufacturing method in modern industry.
Post time:Aug . 09, 2024 06:55
Next:Exploring Innovative Techniques and Applications of Lost Foam Casting in Modern Manufacturing Processes