Lost Foam Casting Coating An Overview
Lost foam casting is an innovative process that has gained traction in the metal casting industry due to its ability to produce complex shapes with excellent surface finish and dimensional accuracy. A critical aspect of this technique is the choice and application of coatings, which play a vital role in determining the quality of the final product. This article delves into the significance, types, and application methods of lost foam casting coatings.
What is Lost Foam Casting?
Lost foam casting (LFC) is a variation of the investment casting process, but instead of using wax patterns, it employs foam patterns—typically made of expanded polystyrene (EPS). The foam is coated with a layer of sand and a suitable binder, creating a mold that is then filled with molten metal. As the metal is poured, the foam evaporates, leaving behind only the solidified metal part. This method allows for the production of intricate shapes that traditional casting methods may struggle to achieve.
The Role of Coatings
The coating used in lost foam casting serves multiple purposes, all of which are crucial for ensuring a high-quality final product. Firstly, coatings enhance the thermal resistance of the foam pattern, allowing it to withstand the high temperatures of molten metal without deforming or reacting adversely. Secondly, they provide a barrier that helps reduce the potential for defects such as gas porosity, which can occur when gases are trapped within the casting. Lastly, coatings can improve the surface finish of the final product and facilitate the smooth release of the metal from the mold.
Types of Coatings
There are several types of coatings used in lost foam casting, each designed to suit specific requirements and applications
1. Aqueous Coatings These are water-based coatings that are easy to apply and remove. They generally contain fine sand and clay, providing a good surface finish and are less toxic to handle.
2. Alcohol-based Coatings These coatings are made using organic solvents, offering excellent adhesion and thermal resistance. They are particularly effective for larger castings where the thermal shock is more significant.
lost foam casting coating
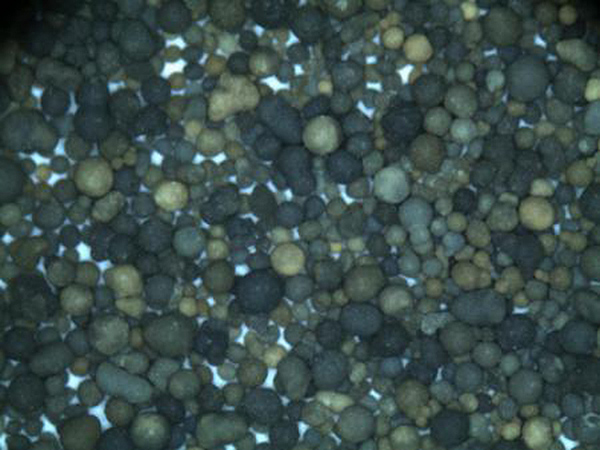
3. Oil-based Coatings These provide enhanced flexibility and durability, making them suitable for complex patterns where abrasion resistance is essential. However, they can be more challenging to handle and may involve more stringent disposal requirements.
4. Specialty Coatings These coatings may include additives specifically designed to enhance certain properties, such as higher thermal stability or improved gas permeability. They are often tailored for unique applications or specific metal alloys.
Application Methods
The application of coatings in lost foam casting typically involves either brushing, spraying, or dipping the foam patterns into the coating mixture. Each method has its advantages depending on the size and complexity of the patterns. For instance
- Brushing Useful for smaller or more intricate patterns where precision is critical. - Spraying Ideal for larger patterns, ensuring an even distribution of coating material.
- Dipping Often used for patterns of various sizes, allowing for uniform coating thickness.
Proper curing of the coatings is also essential to achieve the desired properties and performance. The coated foam patterns are allowed to dry thoroughly before being assembled into molds.
Conclusion
In conclusion, the choice of coating in lost foam casting is a pivotal factor that impacts the process's overall success. As the industry continues to evolve, advancements in coating technologies will further enhance the capabilities of lost foam casting, rendering it an even more attractive option for manufacturers seeking to produce high-quality, complex metal components. In a market demanding efficiency and precision, understanding and optimizing the coating process becomes an integral part of the lost foam casting paradigm.
Post time:Aug . 07, 2024 08:00
Next:Understanding Gold Sand and Its Characteristics in Nature and Industry Applications