What is Sand Casting?
Sand casting, also known as sand mold casting, is one of the oldest and most widely used manufacturing processes for creating metal parts. This versatile technique holds significant importance in industrial production, allowing for complex shapes and a variety of metals to be cast effectively.
The Process of Sand Casting
The sand casting process begins with the creation of a mold, which is typically made from a mixture of sand, clay, and water. The sand acts as a primary material due to its ability to withstand high temperatures and its capacity to form intricate shapes. The first step is to create a pattern, which is a replica of the final object to be produced. Patterns can be made from various materials, including metal, plastic, or wood, depending on the application and desired finish.
Once the pattern is prepared, it is placed in a molding box made of metal or wood. The sand mixture is then packed around the pattern, and ample pressure is applied to ensure the sand conforms to the shape of the pattern. After the sand is compacted, the pattern is removed, leaving a cavity in the shape of the desired object. This cavity is known as the mold.
Next, the mold is heated to improve its strength, and molten metal is poured into the void. Once the metal cools and solidifies, the mold is broken apart, and the finished casting is retrieved. The casting may require further finishing processes, such as machining, grinding, or polishing, to achieve the desired surface finish or specifications.
Advantages of Sand Casting
Sand casting offers several notable advantages, making it a preferred choice for various applications. Firstly, it is highly adaptable to different metal types, including aluminum, brass, iron, and steel. This flexibility allows manufacturers to produce diverse products, from automotive components to intricate artistic sculptures.
what is a sand casting
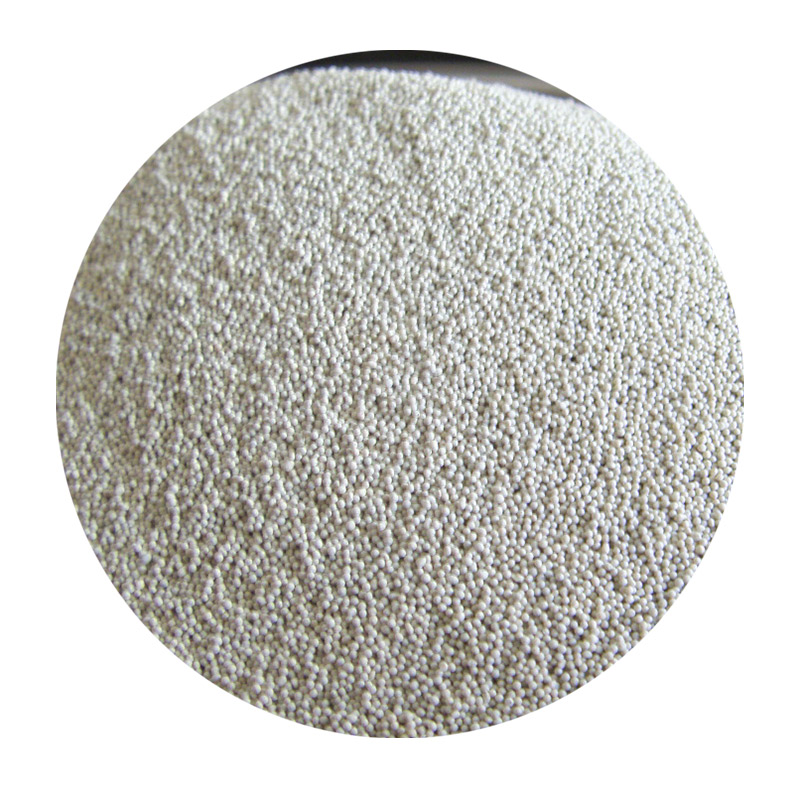
Secondly, the sand casting process can accommodate large and complex shapes that would be difficult or impossible to achieve using other methods. This capability is especially valuable in industries where precision and detail are critical.
Moreover, sand casting is generally cost-effective for low to medium production runs. The initial investment in creating the patterns can be high, but the low cost of materials and the simplicity of the process make it economical, especially when producing large parts.
Limitations of Sand Casting
Despite its advantages, sand casting does have some limitations. One primary concern is the surface finish; the surface of sand cast parts is often rough, which may require additional machining to achieve a smoother finish. Additionally, the dimensional accuracy of sand cast parts may not be as high as that of parts produced using other techniques, such as investment casting or die casting. This lack of precision can be a drawback for applications requiring stringent tolerances.
Another consideration is the time it takes to set up sand casting operations. Creating the patterns and molds can be time-consuming, which may affect production timelines, especially for urgent projects.
Conclusion
In conclusion, sand casting is a well-established manufacturing process that plays a critical role in producing a wide range of metal components. Its adaptability, cost-effectiveness, and ability to create complex shapes make it a popular choice in many industries. While it does have its limitations in terms of surface finish and precision, the advantages often outweigh these drawbacks, ensuring that sand casting remains a vital technique in modern manufacturing. As technology advances, improvements in materials and processes will likely continue to enhance the capabilities of sand casting, further solidifying its place in the production landscape.
Post time:Aug . 10, 2024 05:15
Next:Exploring the Diverse Applications and Benefits of Lost Foam Casting in Manufacturing Processes