Why is Sand Casting Used?
Sand casting is one of the oldest and most versatile methods of metal casting, widely used in the manufacturing industry today. This process, which involves creating a mold from sand to shape molten metal, has gained popularity due to its numerous advantages, making it suitable for various applications. This article explores the reasons why sand casting is favored by engineers and manufacturers alike.
Cost-Effectiveness
One of the primary reasons for the widespread use of sand casting is its cost-effectiveness. The materials required for sand casting are relatively inexpensive compared to other casting methods. The sand used for the molds can often be reused, minimizing waste and material costs. Additionally, the equipment required for sand casting is generally less complex and cheaper than that needed for processes like die casting or investment casting, allowing manufacturers to save on initial investments.
Versatility in Design
Sand casting is highly versatile, accommodating a wide range of complex shapes and sizes. Unlike some casting methods that limit part dimensions, sand casting can produce large and heavy components, making it suitable for various industries, including automotive, aerospace, and heavy machinery. The adaptability to create intricate designs with detailed features is a significant benefit, enabling manufacturers to meet specific project requirements without extensive modifications.
Flexibility with Materials
Another key advantage of sand casting is its compatibility with a broad spectrum of materials. This process can cast various metals, including aluminum, bronze, iron, and steel. By adjusting the composition of the metal, manufacturers can achieve different mechanical properties, making sand casting an ideal choice for producing components with specific characteristics, such as strength, weight, or corrosion resistance.
why is sand casting used
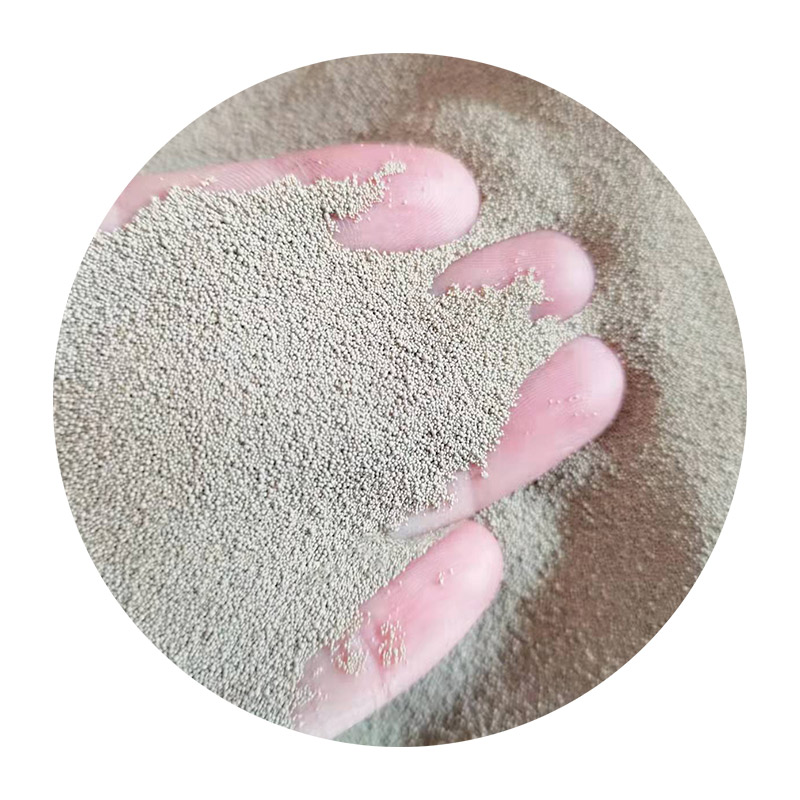
Ability to Produce Large Quantities
While sand casting is often used for one-off prototypes or small production runs, it can be efficiently adapted for mass production as well. Automated sand casting processes can produce large quantities of parts with consistent quality. This scalability allows businesses to meet high-demand requirements without compromising on the integrity of the components produced.
Ease of Modification and Repair
The sand casting process is relatively straightforward, making it easier to modify existing designs or recipes. When changes are necessary, adjustments can be made to the pattern or mold without a complete overhaul of the production process. This flexibility is crucial in industries where design iterations are common, allowing companies to adapt quickly to customer needs.
Quality of Finished Products
Despite being a traditional method, sand casting has advanced significantly in quality control measures. With modern techniques, such as computer-aided design (CAD) and simulation software, manufacturers can enhance the accuracy and quality of the final products. The ability to create detailed surfaces and designs leads to customizable and high-quality components that meet stringent industry standards.
Conclusion
In summary, sand casting is a highly respected manufacturing process due to its cost-effectiveness, versatility, and ability to accommodate a variety of materials. The process's flexibility in design, combined with its capability to produce both small and large quantities of components, makes it an invaluable method in various industries. As technological advancements continue to enhance quality control and production efficiency, sand casting will likely remain a pivotal technique in metalworking for years to come. Whether for simple prototypes or complex industrial components, sand casting serves as a foundation for effective manufacturing solutions.
Post time:Aug . 21, 2024 14:50
Next:Exploring the Art and Techniques of Sand Casting in Modern Manufacturing