Understanding Foundry Sand Its Importance and Applications
Foundry sand plays a crucial role in the metal casting industry, serving as a fundamental component in the production of metal parts and components. This specialized sand, usually composed of high-quality silica, is used primarily in the casting of metal alloys, providing a conducive medium for shaping intricate designs and ensuring the smooth flow of molten metal.
What is Foundry Sand?
Foundry sand is a finely graded mineral aggregate that is predominantly composed of silica (SiO2) and is characterized by its high resistance to heat and its optimal grain structure. The sand is derived from natural sources, often through the mining of quartz and is processed to meet strict industry standards. Depending on the casting process and the type of metal being poured, foundry sand can come in different specifications, typically classified into green sand, resin sand, and lost foam sand.
Green Sand is a mixture of sand, clay, and water, creating a moldable consistency that can withstand the heat from molten metal. This traditional method remains popular due to its cost-effectiveness and versatility.
Resin Sand utilizes synthetic resins as a binding agent, resulting in molds that possess superior strength and dimensional accuracy. This type of sand is commonly used for casting complex shapes and finer details.
Lost Foam Sand is employed primarily for the investment casting process, where foam patterns are used to create the mold. This innovative approach enables high-precision casts and minimizes waste.
The Role of Foundry Sand in Metal Casting
what is foundry sand
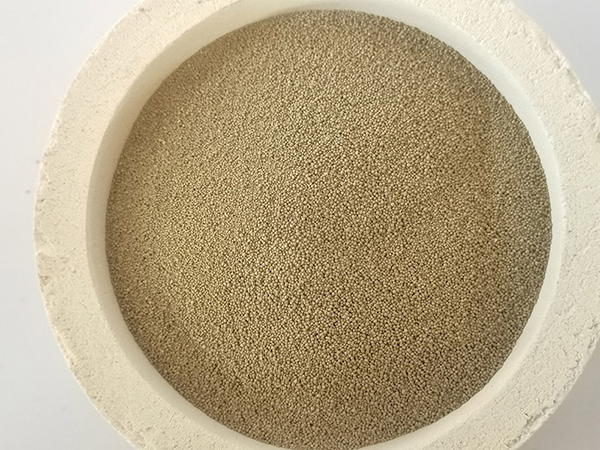
The main function of foundry sand is to form molds that provide the precise shape of the cast metal objects being produced. The properties of foundry sand significantly influence the quality of the final product. Its ability to retain heat, resist deformation, and provide a smooth surface finish is crucial in determining the reliability and durability of the castings.
One significant advantage of using foundry sand is its permeability, which allows gases generated during the metal pouring process to escape, reducing the likelihood of defects such as porosity in the final product. The sand’s thermal stability ensures that it can withstand the high temperatures associated with molten metal, thus preventing the mold from breaking down under stress.
Environmental Considerations
While foundry sand is pivotal in the casting industry, it also poses environmental challenges. The disposal of used foundry sand has raised concerns due to its potential environmental impact. Many foundries are adopting sustainable practices by recycling used sand or finding alternative applications for it in construction materials, roadway bases, or as a soil amendment.
The recycling of foundry sand not only mitigates waste but also contributes to a circular economy within the manufacturing sector. Reprocessed foundry sand retains many of its desirable properties, making it a viable option for various industries, ultimately benefiting both the environment and the economy.
Conclusion
Foundry sand is an indispensable resource in the metal casting industry, enabling the production of high-quality metal components and facilitating various casting processes. Its unique physical properties ensure that molds are both durable and capable of producing intricate designs. As the industry evolves, the adoption of sustainable practices regarding the use and disposal of foundry sand remains crucial. By focusing on recycling and environmentally friendly practices, the foundry sector can not only enhance the quality of castings but also contribute positively to the environment, paving the way for a more sustainable future in manufacturing.
Post time:Aug . 06, 2024 12:36
Next:Exploring the Evolution and Significance of Sand Casting Throughout History and Its Modern Applications