Understanding Foundry Sand An Essential Component in Metal Casting
Foundry sand is a crucial material used in the metal casting industry, playing a vital role in the production of metal components for various applications, from automotive parts to complex machinery. This article delves into what foundry sand is, its types, properties, and its importance in manufacturing processes.
What is Foundry Sand?
Foundry sand, primarily composed of silica, is a fine granular material used in the casting process where molten metal is poured into a sand mold to produce desired shapes and components. The sand acts as a medium for creating molds that hold molten metal, allowing it to cool and solidify into the final product. The typical foundry sand is high-quality silica sand, but some foundries may use synthetic alternatives or recycled materials to enhance performance and promote sustainability.
Types of Foundry Sand
The most common type of foundry sand is silica sand, which is known for its high melting point and resistance to thermal shock. However, different foundries may use various types depending on specific casting requirements
1. Green Sand This is a mixture of silica sand, clay, water, and additives. It is called green because it contains moisture, which helps in bonding the sand particles together. Green sand molds are easy to produce, making them popular for high-volume production in the foundry industry.
2. Dry Sand Unlike green sand, dry sand is made without moisture, providing a dry and loose mold that can be reused. Dry sand provides better surface finishes and is generally used for more intricate molds.
3. Resin-coated Sand This type of sand is treated with synthetic resins that enhance strength and reduce the amount of binder required. Resin-coated sand is known for producing very high-quality molds with excellent precision.
Properties of Foundry Sand
what is foundry sand
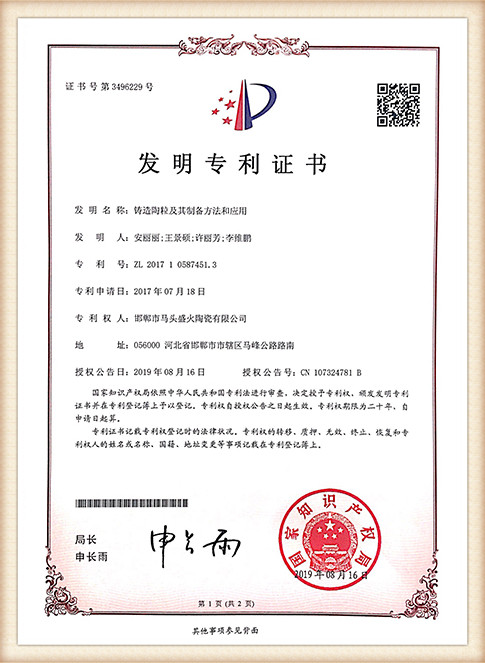
To be effective in metal casting, foundry sand must possess certain characteristics
- Grain Size and Distribution The grain size and distribution of foundry sand affect the mold's permeability and the final finish of the casted metal. The ideal sand grain should be uniform to ensure a smooth surface.
- Refractoriness Foundry sand must withstand high temperatures without breaking down or fusing with the molten metal. A high melting point is essential to maintain mold integrity during the casting process.
- Cohesiveness and Plasticity These properties allow the sand to hold its shape and support the weight of molten metal. Good cohesion between sand grains helps in producing strong molds that can withstand the pressures of casting.
Importance of Foundry Sand in Manufacturing Processes
Foundry sand is indispensable in metal casting for several reasons
- Cost-Effectiveness The use of foundry sand allows for the efficient manufacturing of complex metal shapes at a relatively lower cost compared to other materials and methods.
- Recyclability Foundry sand can often be recycled and reused multiple times, reducing waste and promoting environmental sustainability in manufacturing processes.
- Versatility Foundry sand can be used in various casting processes, including sand casting, investment casting, and shell molding, making it a versatile choice for different industries.
In conclusion, foundry sand is an essential component in the metal casting industry, enabling the production of high-quality metal components. Its unique properties, types, and the ability to recycle make it an invaluable material in manufacturing processes, highlighting its importance in modern industrial applications. As industries continue to evolve, the role of foundry sand remains critical in meeting the demands for precision and efficiency in metal casting.
Post time:Aug . 17, 2024 16:48
Next:Effective Techniques for Smoothing Your 3D Printed Models for a Professional Finish