Sand Casting Iron An Essential Manufacturing Process
Sand casting is a versatile and widely used manufacturing process for producing metal components, particularly iron. This method has been a cornerstone of metallurgy for centuries, and its significance in various industries cannot be overstated. In this article, we will explore the process of sand casting iron, its advantages, applications, and innovations that have emerged over the years.
The Sand Casting Process
The sand casting process begins with the creation of a mold, which is typically made from a mixture of sand, clay, and water. This mixture can easily be shaped and compacted, making it ideal for forming complex geometries. The process begins by creating a pattern of the desired component, usually out of metal, wood, or plastic. This pattern is placed in a sand mixture and compacted to form a mold cavity that replicates the pattern.
Once the mold is ready, it is split into two halves, allowing for the removal of the pattern. The two halves are then joined together and prepared for pouring. Molten iron, heated to its liquid state at high temperatures, is poured into the mold cavity. After adequate cooling, the sand mold is removed, revealing the cast iron component inside. This part can undergo various finishing processes like machining or grinding to achieve the desired specifications.
Advantages of Sand Casting Iron
One of the primary advantages of sand casting is its ability to produce large and complex shapes without significantly increasing production costs. The flexibility of the sand mold allows manufacturers to create intricate designs that may be difficult or impossible with other casting methods. Additionally, sand casting accommodates various sizes, from small components to large industrial parts.
Another significant advantage is the material's properties. Cast iron, known for its excellent fluidity, wear resistance, and vibration-damping qualities, makes it suitable for numerous applications. These characteristics enhance the durability and longevity of components produced through sand casting.
sand casting iron
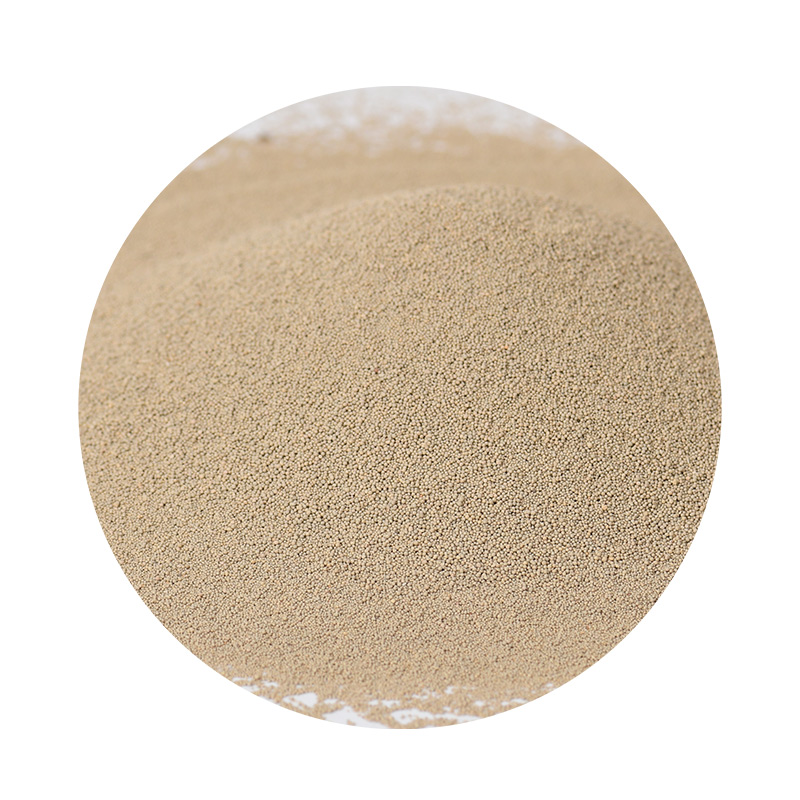
Applications of Sand Casting Iron
The applications of sand casting iron are vast, spanning multiple industries. In the automotive sector, it is utilized to manufacture engine blocks, cylinder heads, and various other components that require high strength and durability. The construction industry also relies on sand-cast iron for items like manhole covers, grates, and decorative architectural features.
In addition, sand casting is popular in the production of machinery parts for heavy equipment, such as agricultural machines, pumps, and compressors. Furthermore, artistic applications, including sculptures and ornamental objects, also benefit from the flexibility and finish quality that sand casting provides.
Innovations and Future Trends
Recent advancements in technology have led to improvements in sand casting processes. Innovations like computer-aided design (CAD) and computer-aided manufacturing (CAM) allow for more precise mold designs and quicker production times. The incorporation of 3D printing technology in mold-making is also transforming the industry, enabling rapid prototyping and reducing lead times for casting projects.
Sustainability is another area of focus. The industry is gradually adopting more eco-friendly practices by recycling sand and using environmentally friendly binders. These changes not only reduce waste but also minimize the industry's overall environmental footprint.
Conclusion
Sand casting remains an essential process for producing iron components that are integral to various sectors. Its advantages in terms of flexibility, cost-effectiveness, and the favorable properties of cast iron make it irreplaceable in modern manufacturing. As technology advances, the sand casting process will likely continue evolving, enhancing its capabilities and aligning with sustainability goals. This enduring technique is a testament to the innovative spirit of the manufacturing industry, ensuring that it meets the demands of contemporary society while honoring its rich historical roots.
Post time:Aug . 17, 2024 15:07
Next:Innovative Techniques for Sand Castings in Modern Manufacturing Practices