The Importance of Molding Sand in Metal Casting
Molding sand plays a vital role in the metal casting process, serving as the primary material for creating molds in which molten metal is poured. Understanding the significance of molding sand, its composition, types, and properties is essential for those involved in foundry operations and metalworking.
At its core, molding sand is a mixture of sand, clay, and water, which forms a sand mold to shape the liquid metal. The choice of sand is crucial, as it must have specific characteristics to ensure the quality and integrity of the casting. Silica sand is the most commonly used type, known for its excellent thermal stability, high melting point, and strength.
The Importance of Molding Sand in Metal Casting
Molding sand can be classified into several types based on its bonding agent and reusable properties. The most common types include green sand, dry sand, and nobake sand. Green sand, which is a mixture of sand, clay, and water, is widely utilized in foundries for its ease of use and cost-effectiveness. It is called green because it contains moisture when used, providing better elasticity and allowing for excellent detail reproduction of the patterns.
molding sand for metal casting
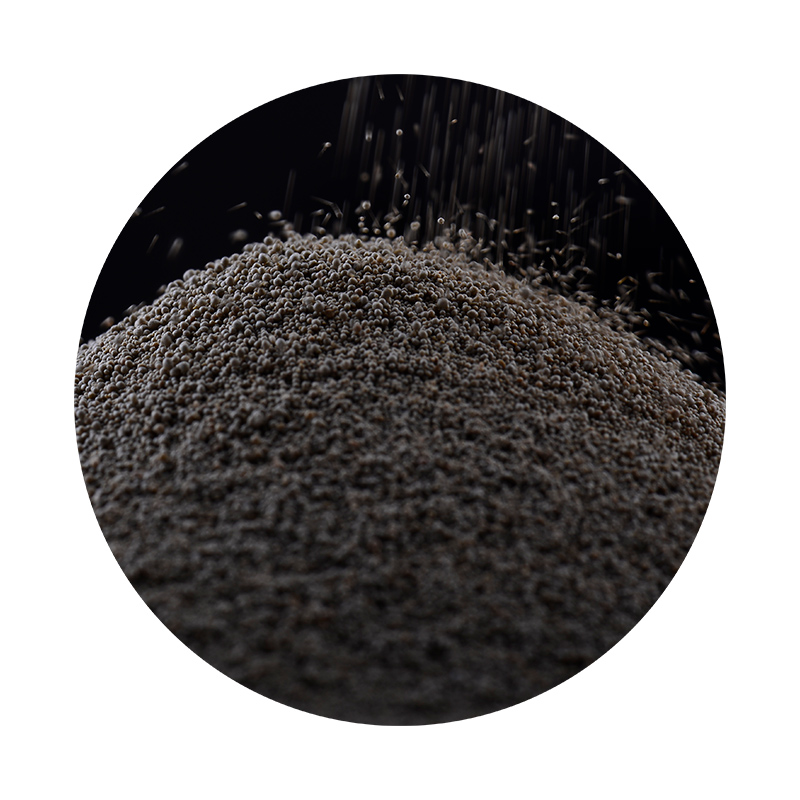
Dry sand, on the other hand, is sand that has been dried and is free from moisture. This helps improve the mold's strength and thermal stability, making it suitable for specific applications where dimensional accuracy is critical. Nobake sand, or chemically bonded sand, uses a resin as a binding agent and does not require water for activation. This type is preferred for its ability to achieve extremely precise molds and is often used for larger castings.
The properties of molding sand can be characterized by several factors, including permeability, strength, and cohesiveness. Permeability is crucial because it allows gases produced during the metal pouring process to escape, preventing defects in the casting. High-quality molding sand should possess sufficient strength to withstand the pressure of the molten metal without deforming. Additionally, cohesiveness ensures that the sand grains stick together, preserving the mold shape during the casting process.
Another important characteristic is the refractoriness of molding sand, which is its ability to withstand high temperatures without breaking down. This property is vital as molten metal can reach extremely high temperatures, and a good molding sand should maintain its integrity during this phase.
In recent years, advancements in technology and material science have led to the development of synthetic molding sands. These new formulations often incorporate various additives to enhance their properties, increase their reusability, and reduce environmental impact. These innovations ensure that foundries can produce high-quality castings while minimizing waste and improving efficiency.
In summary, molding sand is an indispensable component of the metal casting process. Its composition and properties greatly influence the quality of the final product. By understanding the different types of molding sand and their characteristics, foundries can optimize their casting processes and ensure the production of superior metal components. As technology continues to advance, the future of molding sand in metal casting looks promising, paving the way for even higher standards in the foundry industry.
Post time:Aug . 15, 2024 06:04
Next:Techniques and Tips for Effective Sanding in 3D Printing Projects and Models