The Art of Sanding Glazed Ceramics
Sanding glazed ceramics is a crucial technique in the field of pottery and ceramics, playing an essential role in the finishing process of various ceramic pieces
. This procedure not only enhances the aesthetics of the object but also improves its functionality. The art of sanding glazed ceramics involves a series of steps that require skillful execution, understanding of materials, and an appreciation of the final product's form and texture.Glazed ceramics are often celebrated for their vibrant colors and smooth finishes, achieved through the application of a glass-like layer of glaze. However, imperfections during the glazing process—such as uneven surfaces, drips, or bumps—can detract from the overall appearance and tactile experience of the piece. Sanding is the method used to correct these flaws, resulting in a polished, refined item that showcases the artist's craftsmanship.
The sanding process typically begins after the ceramic piece has gone through its initial firing and glazing. At this stage, the glaze is often still somewhat fragile but adequately hardened to withstand sanding. It is essential to use the right type of sandpaper to avoid damaging the glaze. Generally, finer grits—like 400 to 600—are employed to delicately erase blemishes while preventing deep scratches on the surface. For more pronounced imperfections, coarser grits may be utilized initially, followed by finer grits to achieve a smooth finish.
Technique plays a vital role when sanding glazed ceramics. Potters often recommend a gentle, circular motion rather than a back-and-forth stroke, which can create deeper grooves in the glaze. This circular technique allows for a more even removal of material, ensuring that the lustrous surface remains intact after the sanding process is complete. It is also advisable to regularly check the surface’s progress to assess the effectiveness of the sanding and to avoid over-sanding, which could compromise the glaze altogether.
sanding glazed ceramics
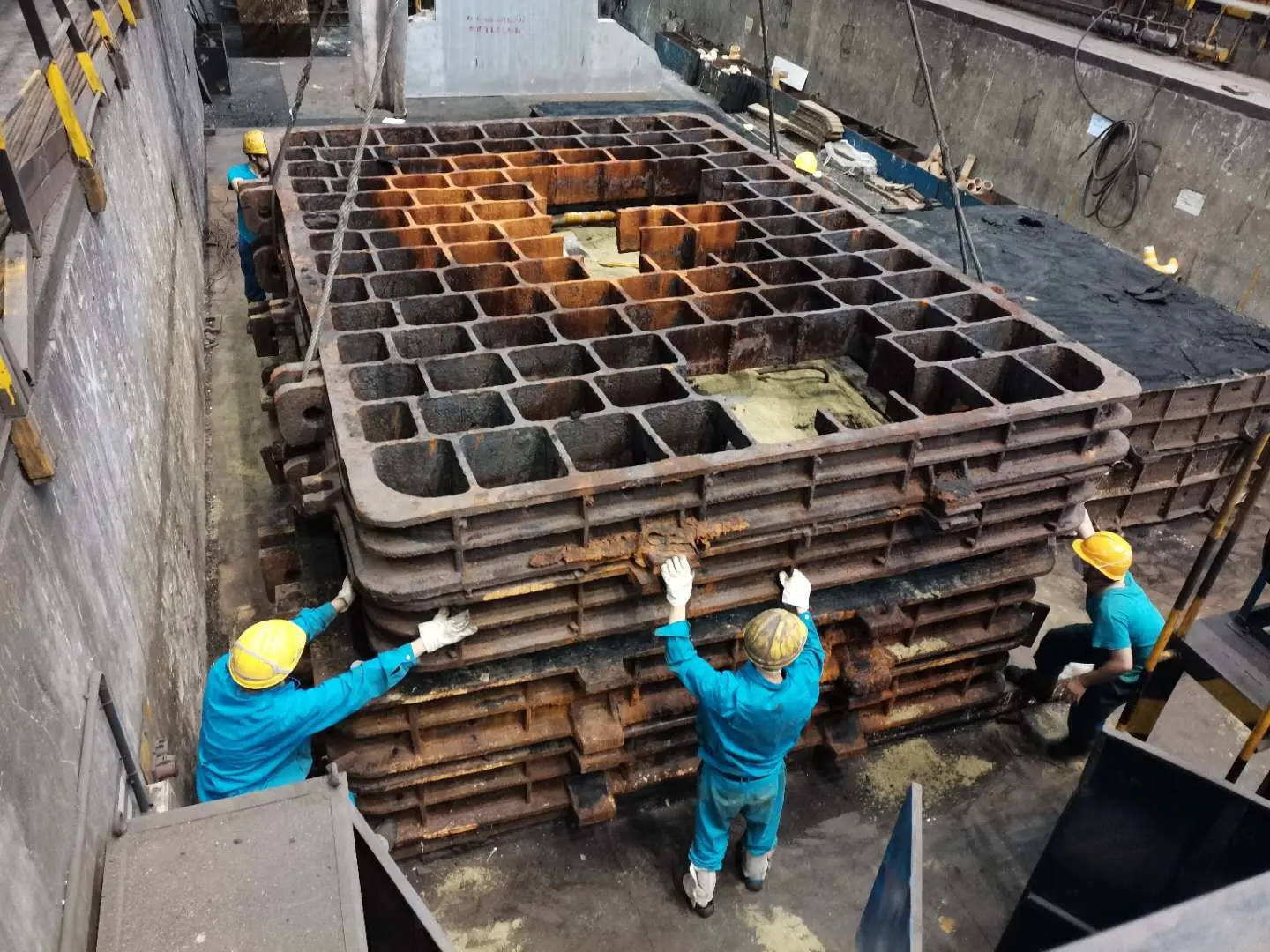
Water can be a useful companion in the sanding process. Wet sanding, which involves using a damp sponge or applying water directly to the sandpaper, helps reduce dust and provides a smoother finish. The moisture allows the sandpaper to glide over the surface more easily, minimizes the risk of heat buildup that can damage the glaze, and helps to achieve a finer polish.
In addition to improving the visual appeal of glazed ceramics, sanding also contributes to the overall feel of the piece. A well-sanded surface can transform a rough, unattractive item into a tactile delight, inviting touch and interaction. This is particularly important for functional ceramics, such as mugs and plates, where the user experience is paramount.
Moreover, this technique is not solely for correcting imperfections. Many artists choose to sand their glazed works intentionally, creating unique textures and finishes that enhance the character of the piece. By selectively sanding areas of a ceramic item, artists can reveal the underlying clay body, adding depth and contrast to the overall design.
In conclusion, sanding glazed ceramics is more than just a remedial process; it is an art form in its own right. This meticulous technique allows potters and ceramic artists to refine their creations, providing them with the opportunity to present the best version of their work. As technology and materials evolve, the fundamentals of sanding remain an indispensable skill in the ceramics community, exemplifying the artist's dedication to quality and aesthetics. Through sanding, glazed ceramics attain not only beauty but also a tactile richness that enhances their value in both artistic and functional realms.
Post time:Jul . 22, 2024 01:02
Next:Techniques for Smoothing and Finishing 3D Print Surfaces for Optimal Painting Results