Sanding Glazed Ceramics Techniques and Benefits
Sanding glazed ceramics is a crucial step in the finishing process of pottery and ceramic artwork. This practice not only enhances the aesthetic appeal of the pieces but also ensures their functionality. In this article, we will explore the techniques involved in sanding glazed ceramics, the benefits of this practice, and tips for achieving the best results.
Understanding the Importance of Sanding
Glazed ceramics often have a smooth, shiny surface that can sometimes be marred by imperfections such as bumps, drips, or uneven glaze application. Sanding helps to refine these surfaces, creating a more polished and professional finish. Additionally, sanding can improve the tactile experience of ceramic pieces, making them more pleasant to handle.
The process of sanding ceramics involves using abrasive materials to gently remove layers of glaze and rectify imperfections. This can be essential for both aesthetic and functional reasons, as rough spots can harbor bacteria and make cleaning difficult. Moreover, sanding can prepare a surface for additional decorative techniques, such as painting or applying new glazes.
Techniques for Sanding Glazed Ceramics
1. Choosing the Right Sandpaper The first step in sanding glazed ceramics is selecting appropriate sandpaper. It is recommended to start with a finer grit (such as 600 or higher) to avoid damaging the glaze. For more severe imperfections, a coarser grit (between 220 and 400) can be used initially, followed by fine grit for finishing.
sanding glazed ceramics
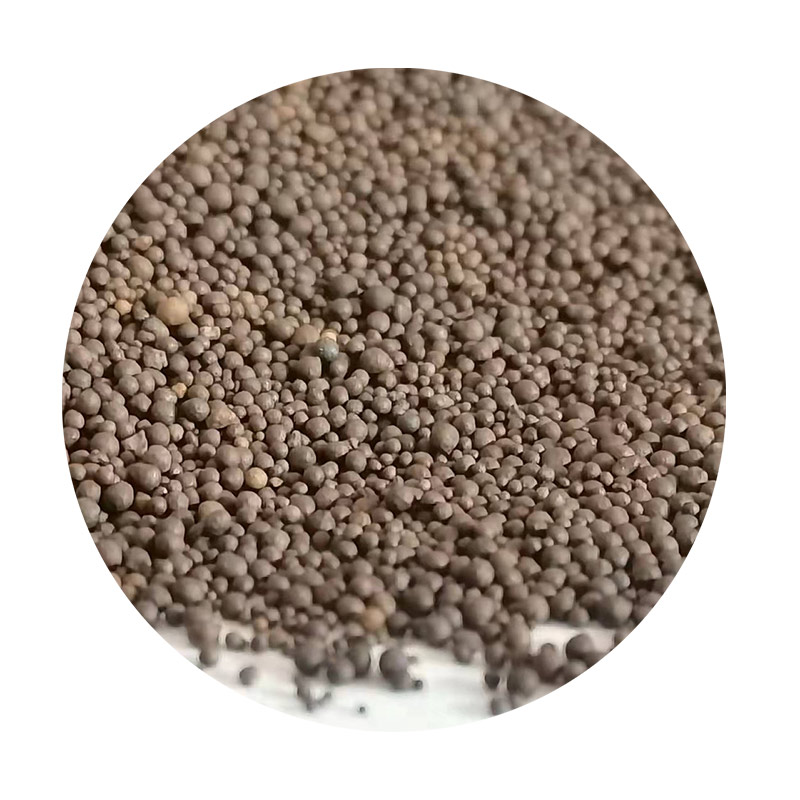
2. Sanding Method When sanding, it is important to apply gentle pressure and use circular or back-and-forth motions. This technique helps to evenly distribute the abrasion and minimizes the risk of deep scratches. Sanding in small, manageable areas allows for better control and more precise results.
3. Wet Sanding To minimize dust and reduce the chance of scratching the surface, wet sanding is recommended. Wetting the sandpaper or the ceramic surface can help to keep the particles of glaze from clogging the abrasive material, providing a smoother finish. Wet sanding also cools the surface and reduces friction, which can be beneficial for delicate pieces.
4. Cleaning Between Grits After using a particular grit, it is essential to clean the piece thoroughly before moving to a finer grit. This removal of dust and debris ensures that the finer sandpaper can effectively smooth the surface without being dulled by particles from the previous sanding.
5. Finishing Touches Once the desired smoothness is achieved, a final polish can be applied to enhance the shine of the glaze. This can be done with a soft cloth or a polishing compound, if necessary. The final result should be a beautifully finished ceramic piece that is both visually appealing and functional.
The Benefits of Sanding Glazed Ceramics
Sanding glazed ceramics not only improves the overall look of the piece but also enhances its durability. A smooth surface is less likely to chip or wear over time, extending the life of the ceramic. Additionally, pieces that have been properly finished through sanding can command higher prices in the market, making this practice advantageous for artisans and hobbyists alike.
In summary, sanding glazed ceramics is an essential technique for achieving high-quality finishes that enhance both beauty and functionality. By understanding the proper methods and benefits of sanding, artists and potters can elevate their work and create stunning ceramic pieces that will stand the test of time. Whether you are an experienced ceramist or a newcomer to the craft, mastering the art of sanding can significantly enhance your ceramic creations.
Post time:Jul . 29, 2024 02:31
Next:Is Sand Casting a Costly Process Compared to Other Manufacturing Methods for Metal Parts?