The Art of Sand Casting A Timeless Manufacturing Process
Sand casting, one of the oldest and most versatile manufacturing processes in the world, has stood the test of time due to its simplicity, cost-effectiveness, and ability to produce complex shapes. This traditional method involves creating a mold from sand, into which molten metal is poured to form a desired object. With applications ranging from automotive parts to artistic sculptures, sand casting remains a vital technique in modern manufacturing.
The Sand Casting Process
The sand casting process begins with the creation of a pattern, which serves as a replica of the final product. Patterns are typically made from materials such as wood, metal, or plastic, depending on the required accuracy and complexity of the design. Once the pattern is finished, it is placed in a sand mixture, which consists of sand, clay, and water. This mixture is compacted around the pattern to form the mold, capturing its shape.
After the sand reaches the desired consistency, the pattern is carefully removed, leaving a cavity that replicates its form. This process requires skill to ensure that the mold will be able to withstand the high temperatures of molten metal without collapsing. Once the mold is prepared, it is assembled, often using multiple pieces to accommodate more complex designs.
The next step is melting the metal, which can vary from aluminum to bronze or even iron, depending on the application. Once the metal reaches a liquid state, it is poured into the mold cavity. Cooling is a critical phase, as the metal must solidify within the shape of the mold. After a cooling period that can range from minutes to hours, the mold is broken apart to reveal the newly formed metal object.
Advantages of Sand Casting
One of the primary advantages of sand casting is its flexibility in producing a wide variety of shapes and sizes. Unlike other manufacturing processes that may require expensive tooling or machinery, sand casting can easily accommodate both small and large production runs. This makes it an ideal method for both prototyping and mass production.
make sand casting
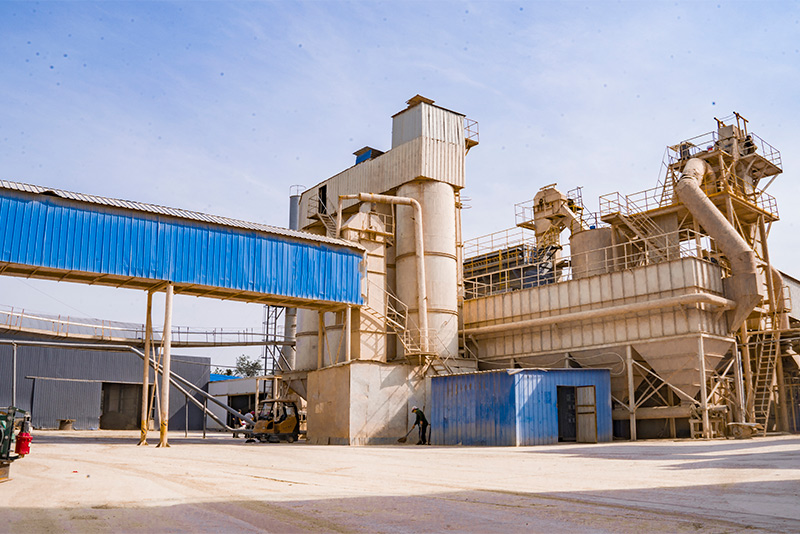
Additionally, sand casting is suitable for a wide range of metal alloys, allowing manufacturers to choose the best material for each specific application. The method also facilitates the production of intricate designs, including internal geometries, which can be challenging to achieve through other casting methods.
Cost is another significant advantage, particularly for low to medium production volumes. The materials used in sand casting, primarily sand and clay, are abundant and inexpensive. Furthermore, the molds can often be reused multiple times, further reducing costs.
Challenges and Innovations
While sand casting has many benefits, it also presents some challenges. The surface finish of sand-cast products may not be as smooth as those produced by other methods, which can require additional machining or finishing processes. Additionally, the accuracy of the dimensions can be affected by factors such as shrinkage and expansion during the cooling process.
Despite these challenges, innovations in sand casting technology continue to emerge. The introduction of computer-aided design (CAD) and computer-aided manufacturing (CAM) has enhanced the precision and efficiency of the casting process. Some modern foundries also employ 3D printing techniques to create more intricate patterns and molds, further pushing the boundaries of what is possible with sand casting.
Conclusion
Sand casting is a remarkable manufacturing process that blends artistry and engineering. Its ability to produce complex shapes, alongside its cost-effectiveness and versatility, ensures that this timeless technique remains relevant in today's fast-evolving industrial landscape. As innovations continue to emerge, the future of sand casting promises even greater possibilities, solidifying its place in the pantheon of manufacturing methods.
Post time:Aug . 08, 2024 00:35
Next:Innovative Uses of Ceramsite Foundry Sand in Modern Casting Applications and Technologies