Understanding the Density of Foundry Sand Importance and Implications
Foundry sand is a critical component in the metal casting industry, primarily due to its ability to provide a shape and support for metal castings during the molding process. One of the most significant characteristics of foundry sand is its density, which plays a vital role in influencing the quality and effectiveness of castings. Understanding the density of foundry sand, its measurement, and its implications can significantly impact the overall success of foundry operations.
What is Foundry Sand?
Foundry sand is composed of a variety of silica grains, pebbles, or other minerals that possess specific characteristics making them suitable for casting processes. The primary function of foundry sand is to create molds that can withstand the heat of molten metal while maintaining the desired shape and surface finish. Its properties, including grain size, shape, and density, determine its performance in various casting operations.
Importance of Density in Foundry Sand
Density, which is defined as mass per unit volume, is essential in determining how well foundry sand can pack and resist deformation under pressure
. The density of foundry sand directly affects several facets of the casting process, including1. Mold Strength Higher density sand can produce stronger molds that can withstand the aggressive conditions present during metal pouring. This strength is critical to preventing mold collapse, which can lead to defects in castings.
2. Thermal Conductivity The density of sand impacts its thermal properties. Denser sand tends to have better thermal conductivity, enabling it to dissipate heat more effectively. This characteristic is essential for controlling solidification rates in metal castings and ensuring uniform cooling.
density of foundry sand
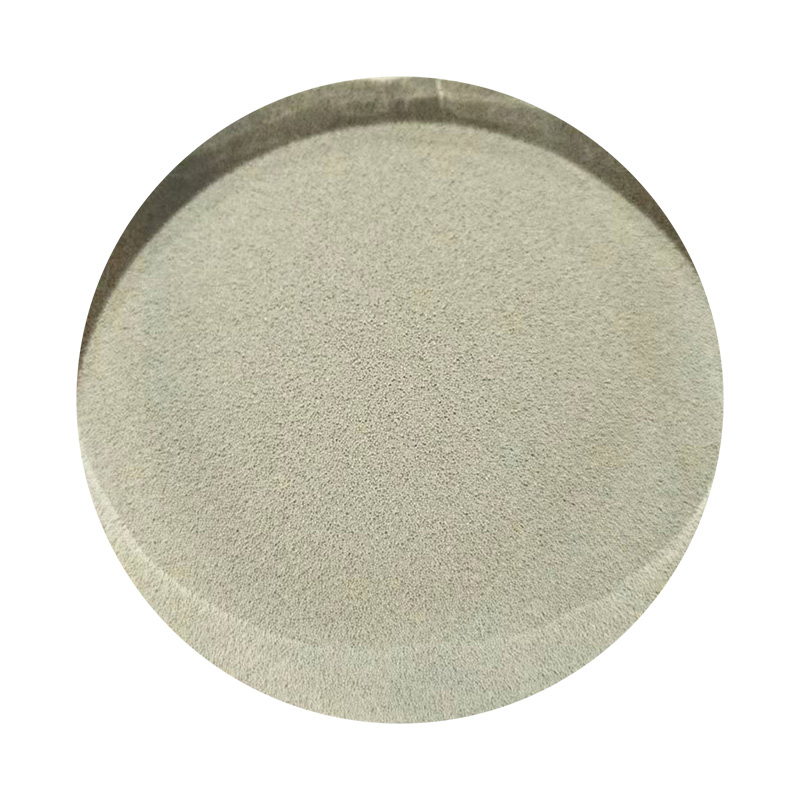
3. Permeability The density of foundry sand also influences its permeability, which refers to the sand's ability to allow gases to escape during the metal pouring process. High-density sand may reduce permeability, leading to gas defects in the final casting if not properly managed.
4. Cost Efficiency Using sand with an optimal density can result in cost savings. Sand that is too dense may require additional processing, while sand that is too light may result in poor mold quality and wasted materials. Striking a balance in sand density can lead to more efficient use of resources and lower production costs.
Measuring Density of Foundry Sand
The density of foundry sand can be measured using various methods, including the bulk density test, which evaluates the weight of dry sand per unit volume, including the space between grains. This measurement can help foundry operators make informed choices about sand selection and processing.
Moreover, specific gravity testing, which measures the ratio of the density of the sand to the density of water, can be employed to assess the quality and suitability of the sand for specific casting applications.
Conclusion
In conclusion, the density of foundry sand is a vital parameter that influences many aspects of the metal casting process. By ensuring that the sand used meets the desired density requirements, foundries can enhance mold strength, improve thermal management, and increase overall casting quality while optimizing costs. As the casting industry continues to evolve, a deeper understanding of foundry sand characteristics, including density, will be essential for achieving high-quality results and maintaining competitive advantage in the marketplace. The careful selection and measurement of foundry sand density will undoubtedly remain a cornerstone of effective foundry operations.
Post time:Jul . 25, 2024 14:09
Next:Exploring the Unique Properties and Applications of Innovative Ceramic Sand Materials in Modern Engineering