How to Make Foundry Sand
Foundry sand is an essential ingredient in the metal casting process, providing the mold for molten metal to take shape. It is known for its ability to withstand high temperatures and retain its form, making it ideal for casting various metal products. Creating high-quality foundry sand is crucial for reliable and efficient foundry operations. This article outlines the steps involved in making foundry sand, including the materials needed and the process itself.
Materials Needed
To create foundry sand, you will need the following materials
1. Silica Sand This is the primary component of foundry sand. Crushed and graded silica sand is preferred due to its ability to withstand high temperatures and its excellent flowability.
2. Clay Clay serves as a binding agent, helping to hold the sand grains together. Common types of clay used in foundry sand include bentonite and kaolin due to their high plasticity and thermal properties.
3. Water Water is added to the mixture to activate the clay, making the sand malleable and easier to mold.
4. Additives (Optional) Various additives can be included to enhance the properties of the sand. These may include organic binders, pigments for coloring, or other chemical agents to improve sand performance.
The Process of Making Foundry Sand
how to make foundry sand
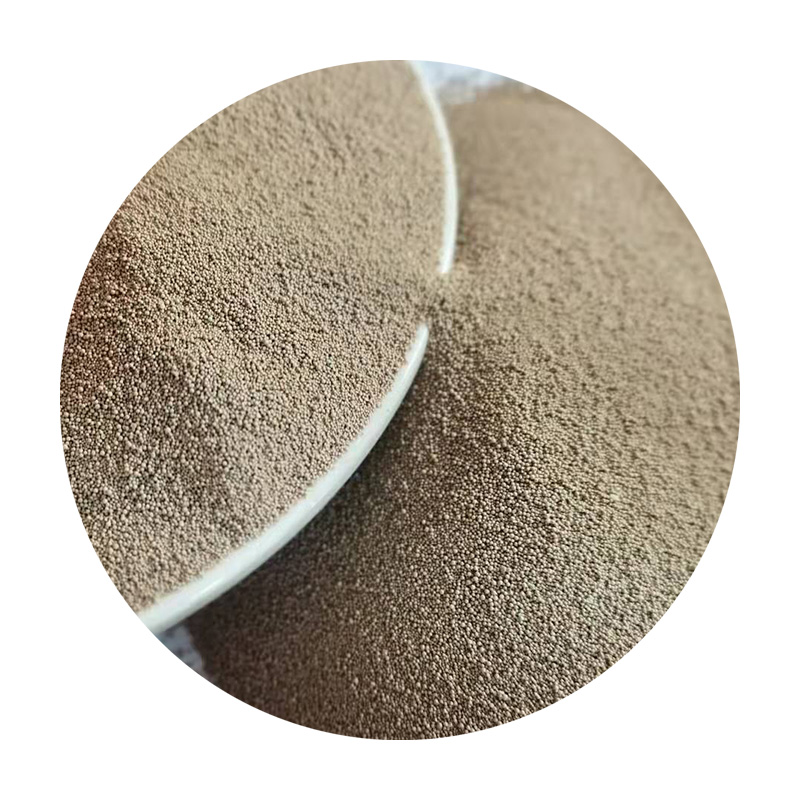
The process of making foundry sand involves several steps, each aimed at ensuring the right composition and quality of the final product.
1. Selection of Silica Sand Begin by sourcing high-quality silica sand. Look for sand with well-rounded grains and minimal impurities. The grain size distribution is also important; it should be within the range of 0.1 to 0.5 mm for optimal performance.
2. Mixing with Clay In a clean mixing container, combine the silica sand with the selected clay. The typical ratio is about 90-95% sand to 5-10% clay, depending on the specific requirements of the casting process. The clay must be thoroughly dispersed throughout the sand to ensure a uniform mixture.
3. Adding Water Gradually add water to the sand-clay mixture. The amount of water required varies based on the type of clay used and the desired consistency of the sand. Aim for a slightly damp mixture that can hold its shape when molded but stops short of being overly wet.
4. Mixing the Components Use a mechanical mixer or a shovel to mix the sand, clay, and water thoroughly. This step is crucial, as proper mixing ensures even coating of the sand grains with clay, resulting in better binding properties.
5. Testing the Sand Before using the sand in production, conduct several tests to check its quality. These may include tests for permeability, plasticity, and compressive strength. Adjust the mix as necessary by adding more clay or water until the desired properties are achieved.
6. Storage Once the foundry sand is ready, store it in a dry, ventilated area to prevent moisture absorption and maintain its quality. Proper storage conditions are essential for keeping the sand usable over time.
Conclusion
Making foundry sand is a systematic process that requires careful attention to material selection and mixing techniques. By following these steps, foundries can produce high-quality sand tailored to their specific casting needs. Consistent quality of foundry sand is critical for the efficiency of metal casting processes, leading to better product integrity and reduced defects in the final cast products. With the right knowledge and practices, foundries can ensure optimal performance and sustainability in their operations.
Post time:Aug . 14, 2024 07:16
Next:Techniques for Achieving a Smooth Finish on Ceramics Through Wet Sanding Methods and Tips