The Art and Science of Steel Sand Casting in Foundries
Steel sand casting is a foundational process in the manufacturing industry, playing a vital role in producing intricate metal components required for various applications. This method combines the age-old craft of casting with modern technological advancements, resulting in high-quality steel products. In this article, we’ll explore the fundamentals of steel sand casting, its advantages, and its applications in contemporary foundries.
At its core, sand casting involves creating a mold from sand, into which molten steel is poured. The process begins with creating a pattern, typically made from metal or wood, that resembles the final product. The pattern is pressed into a mixture of sand and a binding agent, creating a mold cavity. Once the mold is prepared, the pattern is removed, leaving behind an impression of the desired shape.
The Art and Science of Steel Sand Casting in Foundries
The advantages of steel sand casting are manifold. Firstly, the use of sand as a primary material offers excellent thermal properties, allowing for even cooling and solidification of the molten steel. This results in reduced internal stresses within the cast product, leading to improved mechanical properties. Moreover, the sand mold can be easily reused or recycled, making it a cost-effective solution for foundries.
steel sand casting foundry
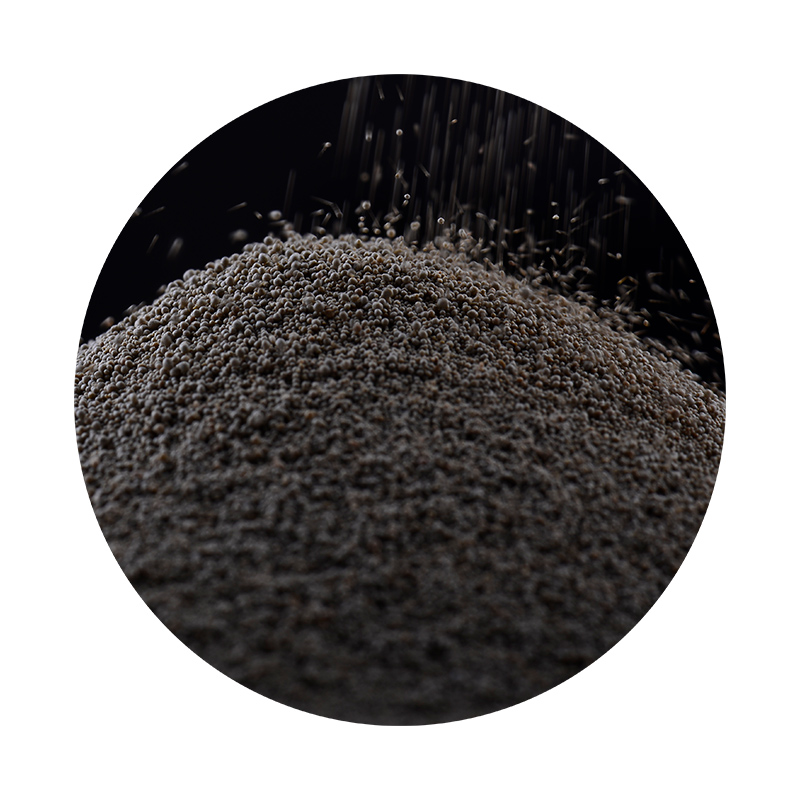
Steel sand casting also enables the production of components with outstanding surface finishes and dimensional accuracy. With advancements in mold-making techniques and technology, foundries can now achieve tighter tolerances, reducing the need for extensive machining after casting. This efficiency not only saves time but also cuts down on material waste, contributing to a more sustainable manufacturing process.
In terms of applications, steel sand casting is vital across numerous industries. In the automotive sector, it is used to produce critical components such as engine blocks and transmission cases. The strength and durability of steel make it an ideal choice for parts that must withstand high stresses and repetitive loads. In the aerospace industry, steel castings are utilized for engine components, landing gear, and various structural elements, where reliability and safety are paramount.
The oil and gas industry also leverages steel sand casting to manufacture essential components like valve bodies, fittings, and pumps. These parts must endure harsh conditions, and the robustness of steel ensures they maintain functionality over extended periods. Additionally, in construction, steel sand casting is used to produce various fittings and structures, contributing to the durability of buildings and infrastructure.
As the demand for high-quality, reliable components continues to grow, steel sand casting in foundries remains a crucial method of production. With ongoing advancements in technology—such as automation, computer-aided design (CAD), and 3D printing—foundries are poised to enhance the efficiency and capabilities of the sand casting process. These innovations will not only improve productivity but also foster a new generation of designs that were previously unattainable.
In conclusion, steel sand casting is a time-tested yet evolving method that lies at the intersection of art and engineering. Its ability to produce complex, durable components makes it an indispensable technique in modern manufacturing. As industries continue to embrace innovation, the future of steel sand casting looks promising, ensuring its place as a key player in the realm of foundry production.
Post time:Aug . 20, 2024 10:00
Next:Nisip ultra hidro pentru construcții eficiente și durabile