The Role of Sand for Casting in Metalworking
Casting is one of the oldest manufacturing processes known to humankind, with roots dating back thousands of years. Among the various materials used in casting, sand has emerged as one of the most popular and essential mediums, particularly for metalworking. The unique properties of sand make it an ideal material for creating molds that produce intricate and detailed metal components.
Types of Casting Sand
There are several types of sand used for casting, but the most common is silica sand due to its heat resistance and abundant availability. Silica sand consists mainly of quartz, which can withstand high temperatures and does not react with molten metals. In addition to silica, other materials, such as clay and additives, may be mixed with sand to improve the properties of the mold.
Green sand, a mixture of silica sand, clay, and water, is extensively used in casting processes. This type of sand retains moisture, which helps bind the grains together, creating a sturdy mold. The advantages of green sand casting include its cost-effectiveness, recyclability, and the ability to produce complex shapes with high accuracy.
Another form is resin-bonded sand, which uses synthetic resins to bond sand grains. This type of sand can produce molds with finer details and smoother surfaces compared to green sand. However, it comes at a higher cost and requires careful handling of the resins to ensure a safe working environment.
The Casting Process
The casting process begins with preparing the sand mold. First, patterns are made, typically from metal or plastic, which represent the final product's shape. These patterns are placed in a mold box and covered with sand. The sand is compacted around the pattern, creating a cavity that will hold the molten metal.
Once the mold is prepared, the pattern is removed, leaving a hollow space. Molten metal is then poured into this space, filling the mold to create the desired shape. After the metal has cooled and solidified, the sand mold is broken away, revealing the final cast component.
sand for casting
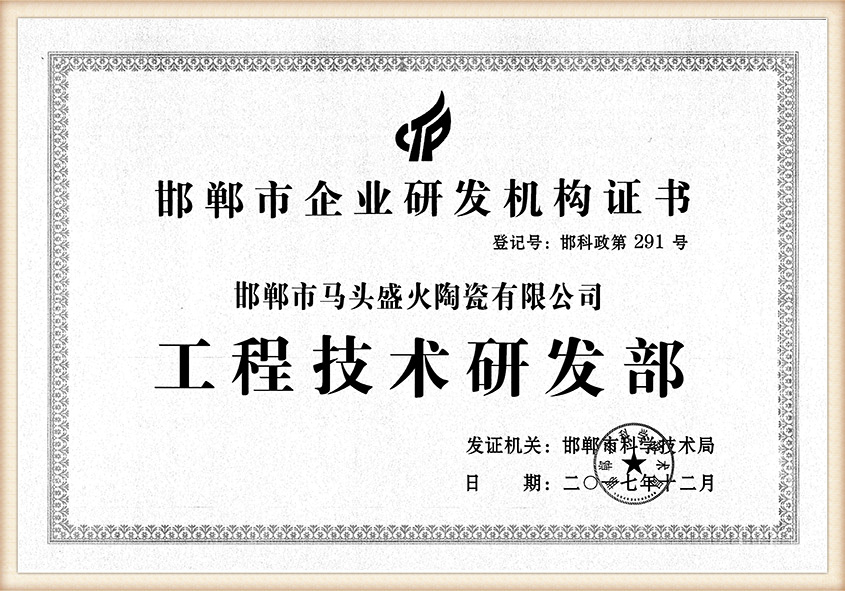
Advantages of Sand Casting
One of the primary advantages of sand casting is its flexibility. It allows for the production of both small batches and large quantities of parts, making it suitable for various industries, including automotive, aerospace, and construction. The process also permits the use of a wide range of metals, including aluminum, steel, bronze, and iron, leading to diverse applications.
Furthermore, sand casting can cater to complex designs that require intricate details. The ability of sand to adapt to various shapes enables manufacturers to produce customized parts that meet specific requirements. This versatility is particularly valuable in industries where bespoke components are needed.
Environmental Considerations
Sand casting is often seen as a more environmentally friendly option compared to other casting methods. The sand used can be reused multiple times, reducing waste and minimizing the need for new materials. Additionally, advancements in sand recycling technologies have made it easier to reclaim and purify used sand, thus lowering the environmental footprint associated with the process.
However, the casting industry still faces challenges regarding the handling of binders and additives that may contain harmful substances. Ongoing research and innovations are focused on developing eco-friendly alternatives to synthetic binders, further enhancing the sustainability of sand casting.
Conclusion
In summary, sand for casting plays a crucial role in the metalworking industry, offering versatility, cost-effectiveness, and the ability to create complex shapes. As technology and materials continue to evolve, sand casting remains a fundamental process in manufacturing, balancing efficiency with environmental responsibility. The unique properties of sand, along with its adaptability to various applications, ensure that it will remain a preferred choice in the metalworking domain for years to come.
Post time:Nov . 07, 2024 15:07
Next:Top Suppliers for Sand Casting Services and Solutions Worldwide