Sand Casting Process An Overview
Sand casting is one of the oldest and most versatile methods of metal casting, used extensively in various industries for producing intricate metal parts. The fundamental principle of sand casting involves creating a mold from sand and then pouring molten metal into that mold to form a solid object upon cooling. This process is characterized by its affordability, simplicity, and ability to produce complex shapes, making it highly popular among manufacturers.
The sand casting process begins with the preparation of the sand mixture. This mixture typically consists of silica sand, a binder (such as clay), and water. The proportions are crucial as they determine the strength of the mold, its ability to withstand the heat of molten metal, and the detail level of the final cast. The sand must be fine enough to capture intricate details but coarse enough to allow for good drainage of gases during the pouring process.
Next, a pattern is created that reflects the shape of the final product. Patterns can be made from various materials, including wood, metal, or plastic, depending on the desired finish and production volume. The pattern is then used to form a mold. The mold-making process involves packing the sand mixture around the pattern to create a cavity. Once the sand is adequately compacted, the pattern is removed, leaving a hollow impression that serves as the mold for pouring the molten metal.
sand casting process
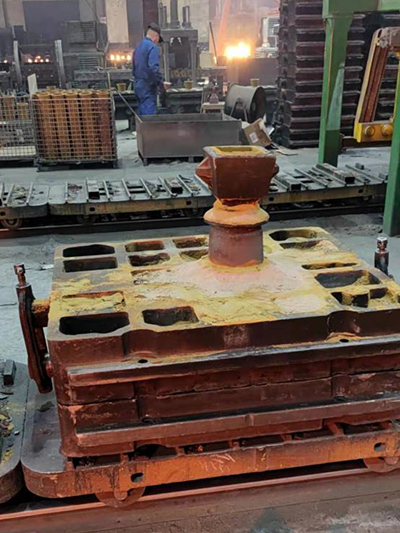
After preparing the mold, the next step involves melting the metal. Various metals can be used in sand casting, including aluminum, bronze, iron, and steel, each selected based on the application and desired characteristics of the final product. Once the metal reaches its molten state, it is carefully poured into the mold cavity through a system of channels known as gates. This stage must be executed with precision to minimize defects such as air bubbles or inclusions, which can compromise the integrity of the final component.
Once the molten metal fills the mold, it is allowed to cool and solidify. Cooling time can vary based on the metal used and the thickness of the casting. After solidification, the sand mold is broken away to reveal the cast part. This process often requires additional finishing work, such as grinding, sanding, or machining, to achieve the desired surface finish and tolerance levels.
One of the significant advantages of sand casting is its scalability and adaptability. It can accommodate small-batch production or large-scale manufacturing, depending on the specific needs of the project. Furthermore, complex geometries can be achieved without the need for costly tooling, making it an attractive option for prototypes and custom parts.
In conclusion, the sand casting process stands out as a time-tested method for producing metal components. Its simplicity, cost-effectiveness, and ability to create detailed designs make it a preferred choice for various industries, including automotive and aerospace. As technology advances, the traditional sand casting process continues to evolve, incorporating modern innovations to enhance efficiency and product quality.
Post time:Oct . 13, 2024 21:55
Next:Affordable Sand Casting Solutions for Your Business Needs and Projects