Sand Casting Manufacturing Process An Overview
Sand casting is one of the oldest and most versatile methods of metal casting, widely utilized in various industries to produce complex shapes and components
. The process employs sand as the primary molding material, making it cost-effective and suitable for both small-scale and large-scale productions.The sand casting process begins with pattern making, where a replica of the desired product is crafted from materials such as wood, metal, or plastic. This pattern is typically slightly larger than the final product to account for the shrinkage that occurs when the metal cools and solidifies. Patterns are designed to create a mold cavity that accurately replicates the intended shape.
Once the pattern is completed, the next step is to create the mold. The mold consists of two halves the cope (top half) and the drag (bottom half). Fine sand mixed with a binding agent, commonly clay, is packed around the pattern to form the mold. The quality of the sand is crucial, as it must maintain its shape while allowing gas to escape during pouring. After packing, the two halves are carefully separated, and the pattern is removed, leaving a cavity in the sand that reflects the shape of the desired component.
sand casting manufacturing process
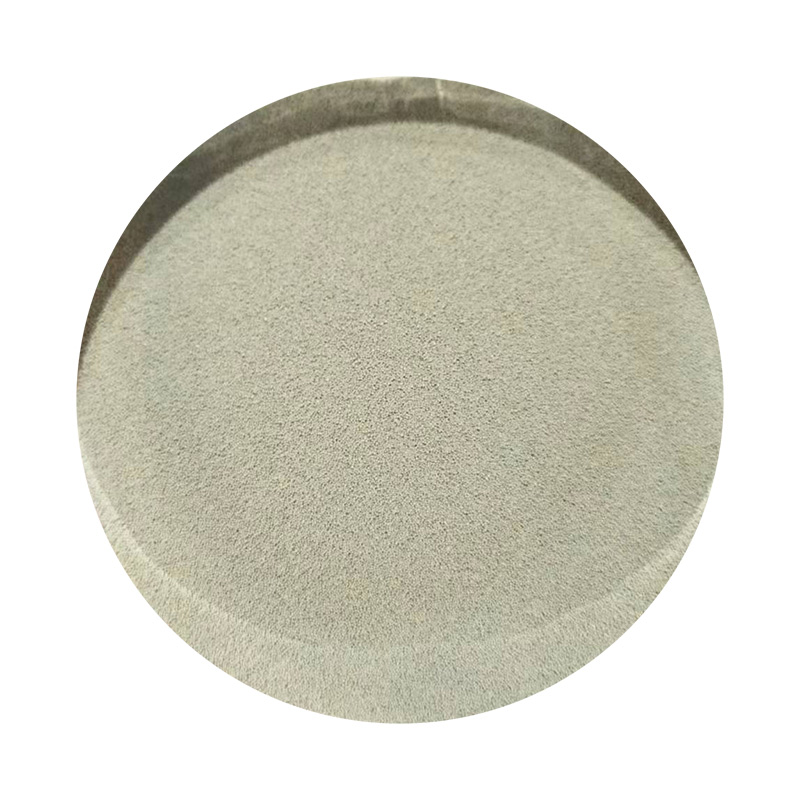
After preparing the mold, the next stage involves pouring molten metal into the mold cavity. This metal is usually heated in a furnace and can vary depending on the requirements of the final product, with common materials including aluminum, iron, and bronze. The molten metal is poured carefully to avoid defects, and it fills the mold, taking on its shape as it cools.
Once the metal has cooled and solidified, the mold is broken apart to retrieve the cast part. This stage often requires additional processing, such as removing excess sand, trimming excess metal, and finishing surfaces to meet required specifications. Secondary operations, like machining or heat treatment, may also be necessary to improve the part's structural integrity and precision.
One of the primary advantages of sand casting is its flexibility in manufacturing. It can produce large components with intricate geometries, making it ideal for industries such as automotive, aerospace, and machinery. Furthermore, the process allows for the use of a wide variety of metals, catering to diverse industrial needs.
In conclusion, the sand casting manufacturing process is a robust method that balances versatility, cost-effectiveness, and complexity in metal fabrication. As industries continue to evolve, sand casting remains a staple technique, providing essential components for numerous applications while adapting to modern advancements in technology and materials.
Post time:Oct . 04, 2024 16:43
Next:bauxite sand