Sand Casting Foundry An Overview
Sand casting, one of the oldest and most widely used metal casting processes, relies on the use of sand as the primary mold material. This method has remained popular due to its versatility, cost-effectiveness, and ability to produce intricate shapes. The sand casting foundry is where these processes take place, and understanding its operations, advantages, and challenges can provide valuable insights into the metalworking industry.
What is Sand Casting?
Sand casting involves the creation of a mold from sand into which molten metal is poured to create a desired shape. The process typically starts with a model of the final object, often made from metal or plastic. This model is embedded in sand mixed with a binding agent, which could be clay or resin. When the mold is formed, it includes a cavity that reflects the shape of the model.
Once the mold is ready, it is subjected to a heating process to strengthen it before molten metal is poured. After the metal cools and solidifies, the sand mold is broken away to reveal the finished casting. This method is particularly capable of producing large and complex shapes, making it suitable for a range of industries, including automotive, aerospace, and art.
Advantages of Sand Casting
One of the primary benefits of sand casting is its flexibility in producing a wide range of shapes and sizes, from small parts to large components. The sand mold can easily accommodate various design specifications, which is essential for custom parts.
Cost-effectiveness is another significant advantage. The materials used in sand casting—primarily sand and a binding agent—are relatively inexpensive compared to other mold materials. Additionally, sand molds can be reused multiple times, which further reduces production costs.
The sand casting process also allows for the use of various metals and alloys. This flexibility means manufacturers can choose materials based on the desired properties of the final product, whether it be strength, weight, or corrosion resistance.
sand casting foundry
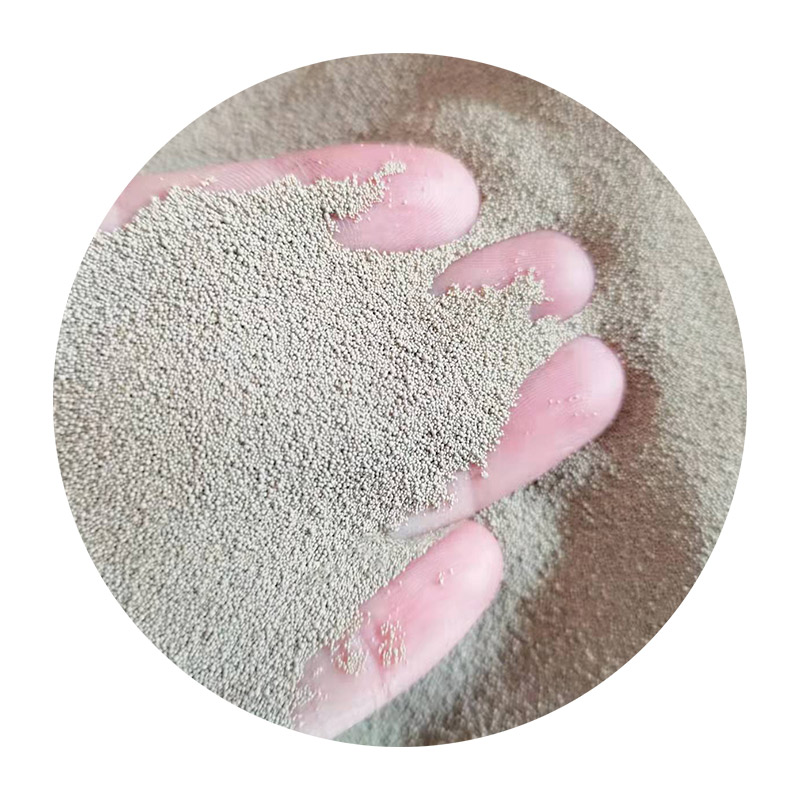
Challenges in Sand Casting
Despite its advantages, sand casting is not without its challenges. One of the main issues is the rough surface finish that often results from the sand mold. While this can be acceptable for many applications, it may require additional machining for parts requiring a smoother finish, thus increasing production time and costs.
Another challenge is the potential for defects in the cast product, such as porosity or incomplete filling of the mold. These defects can arise from several factors, including improper melting temperatures, inadequate mold venting, or poor sand quality. Maintaining strict quality control measures is essential to minimize such issues.
The Role of Technology
With advancements in technology, sand casting foundries are adopting new methods to improve efficiency and accuracy. Computer-Aided Design (CAD) software allows for precise modeling and simulation of the casting process, enabling engineers to predict potential problems before production. Additionally, innovative sand recycling systems help foundries manage waste and reduce costs.
3D printing is also making waves in the sand casting industry. It allows for the rapid production of molds and cores, reducing lead times and enabling quick adjustments to designs. This technology enhances the customization aspect inherent in sand casting, making it a more attractive option for modern manufacturers.
Conclusion
Sand casting foundries play a crucial role in the metal casting industry by providing an efficient way to produce a wide variety of metal components. While there are challenges associated with the process, the advantages of cost-effectiveness, flexibility, and adaptability make sand casting a preferred method for many applications. With ongoing technological advancements, the future of sand casting looks promising, offering opportunities for increased efficiency and product quality. As industries continue to evolve, the sand casting foundry stands firm, contributing to the development of innovative solutions across various sectors.
Post time:Oct . 11, 2024 21:12
Next:Understanding the Basics and Process of Sand Casting in Manufacturing