Sand Casting 101 An Overview of the Basics
Sand casting, also known as sand mold casting, is one of the oldest and most widely used metal casting processes. It involves creating a mold from sand in which molten metal is poured to form a specific shape. This technique is favored for its simplicity, cost-effectiveness, and versatility, making it an ideal choice for both small and large-scale production.
The Sand Casting Process
The sand casting process begins with the preparation of a mold. The first step involves creating a pattern, which is an exact replica of the final product. Patterns are typically made from materials such as wood or metal and are designed to allow for the expansion of metal when it solidifies. The pattern is then placed into a mold box, which is filled with a mixture of sand and a binding agent—usually clay or resin.
Once the sand is compacted around the pattern, it forms a mold cavity. The pattern is removed carefully, leaving behind a hollow shape that mirrors the desired object. The next step is to create a gating system, which includes channels that allow the molten metal to flow into the mold cavity.
After preparing the mold, the metal is melted in a furnace. Common metals used in sand casting include aluminum, iron, and bronze, chosen based on the specific requirements of the finished product. Once the metal reaches the appropriate temperature, it is poured into the mold through the gating system.
After the molten metal has cooled and solidified, the mold is broken away to reveal the cast part. This step might involve shaking out the sand or using a vibrating table to dislodge the casting. The final product may require additional finishing processes, such as grinding, machining, or surface treatment.
Advantages of Sand Casting
sand casting 101
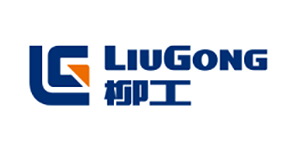
One of the primary advantages of sand casting is its ability to produce complex shapes with intricate details. The flexibility of the sand mold allows for easy modifications, making it suitable for low-volume production runs and prototyping. Additionally, sand is a readily available and inexpensive material, contributing to the overall cost-effectiveness of the process.
Sand casting also supports the use of a wide range of metals and alloys, allowing manufacturers to select materials based on specific mechanical properties, corrosion resistance, or other characteristics relevant to the application. The process is scalable, which means it can accommodate both small and large castings, from intricate components in machinery to large parts in automotive or aerospace industries.
Challenges and Considerations
Despite its many advantages, sand casting does have some challenges. The dimensional accuracy of cast parts can sometimes be affected by the sand mold's ability to hold its shape during pouring. Additionally, the surface finish of sand cast parts may not meet the standards required for certain applications without additional processing.
Moreover, the labor-intensive nature of creating patterns and molds can lead to longer lead times compared to other manufacturing processes. Therefore, careful planning and design considerations are crucial to maximizing efficiency and minimizing waste during the casting process.
Conclusion
Sand casting is a time-honored method that remains relevant in modern manufacturing due to its adaptability and cost-efficiency. By understanding the fundamentals of sand casting, manufacturers can harness its benefits and produce high-quality components tailored to a variety of industries. As technology progresses, innovations in sand casting will likely continue to enhance its capabilities and applications, ensuring its place in the future of manufacturing.
Post time:Nov . 24, 2024 13:53
Next:Understanding the Role of Foundry Casting Sand in Metal Fabrication Processes